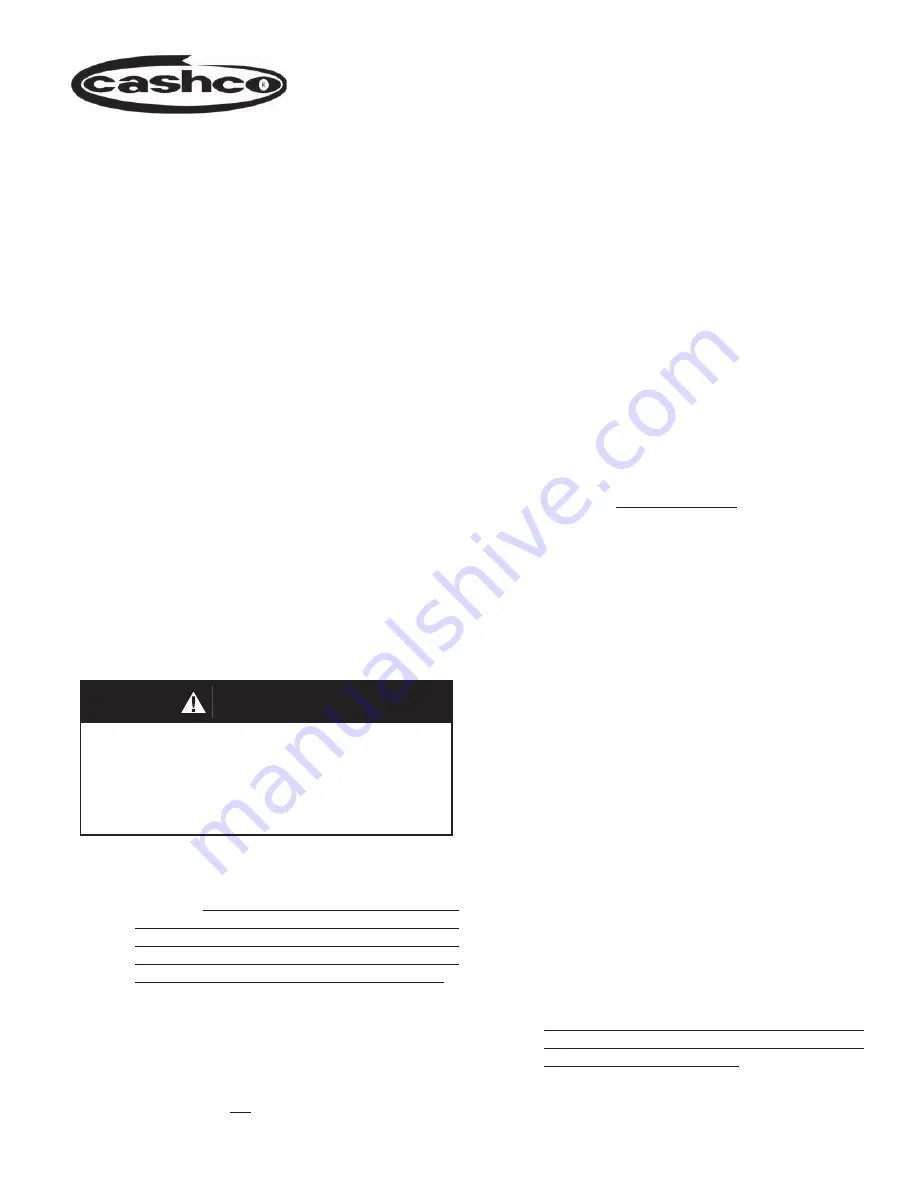
INSTALLATION, OPERATION & MAINTENANCE MANUAL (IOM)
IOM-DA8
01-17
I. DESCRIPTION AND SCOPE
The Model DA8 is a differential back pressure regulator used to control differential pressure between the upstream
(inlet or P1) pressure and a loading (PLoad) pressure to the spring chamber. Available in sizes 1/2" (DN15), 3/4"
(DN20), 1" (DN25), 1-1/4" (DN32), 1-1/2" (DN40), 2" (DN50), 2-1/2" (DN65), 3" (DN80) and 4" (DN100). With proper
trim uti li za tion, the unit is suitable for liquid, gaseous, or steam service. Model DA8 is assembled in the “reverse”
flow direction arrangement that is balanced (to outlet).
MODEL DA8
(Formerly DA8/9)
DIRECT-ACTING, POSITIVE BIAS DIFFERENTIAL
BACK PRESSURE REGULATOR
SECTION I
II. REFERENCES
Refer to Technical Bulletin DA8-TB for tech ni cal
specifications.
ABBREVIATIONS
CCW – Counter
Clockwise
CW –
Clockwise
ITA
– Inner Trim Assembly
III. INSTALLATION
4. An inlet pressure gauge should be located ap-
prox i mate ly ten pipe diameters upstream, and
within sight. A loading pressure (or differential
pressure) gauge is rec om mend ed.
5. Clean the piping of all foreign material including
chips, welding scale, oil, grease and dirt before in-
stall ing the regulator. Strainers are rec om mend ed.
6. In placing thread sealant on pipe ends prior to
en gage ment, ensure that excess material is re-
moved and not allowed to enter the regulator upon
startup.
7. Flow Direction: Install so the flow direction match es
the arrow cast on the body or other markings such
as "in" and "out".
8. Precaution for Standard Diaphragm Construction:
The loading pressure should be lowered sufficiently
prior to shutting off the process fluid supply, to pre-
vent change to the diaphragm. Startup, shutdown,
and emergency operating procedures should be
reviewed to ensure that the loading pressure is
less than 50% of the Diaphragm Proof Rating (See
SECTION III
SECTION II
CAUTION
For welded installations, all internal trim parts, seals
and diaphragm(s) must be removed from reg u la-
tor body prior to welding into pipeline. The heat of
fusion welding will dam age non-metallic parts if
not re moved. NOTE: This does not apply to units
equipped with extended pipe nip ples.
1. Regulator may be rotated around pipe axis 360
degrees. For ease of maintenance, the recom-
mended position is with the spring chamber (4)
upwards. In liquid service it is recommended that
the spring cham ber (4) be oriented downwards, and
that a cus tom er supplied and installed vent valve
be pro vid ed at the external sensing con nec tion to
bleed-off trapped gas/air under the di a phragm.
2. Provide space below, above, and around reg u la tor
for removal of parts during maintenance.
3. Install block valves and pressure gauges to pro-
vide means for adjustment, operation, bypass, or
removal of the regulator. An isolation valve on the
loading line is not rec om mend ed.
ISO Registered Company