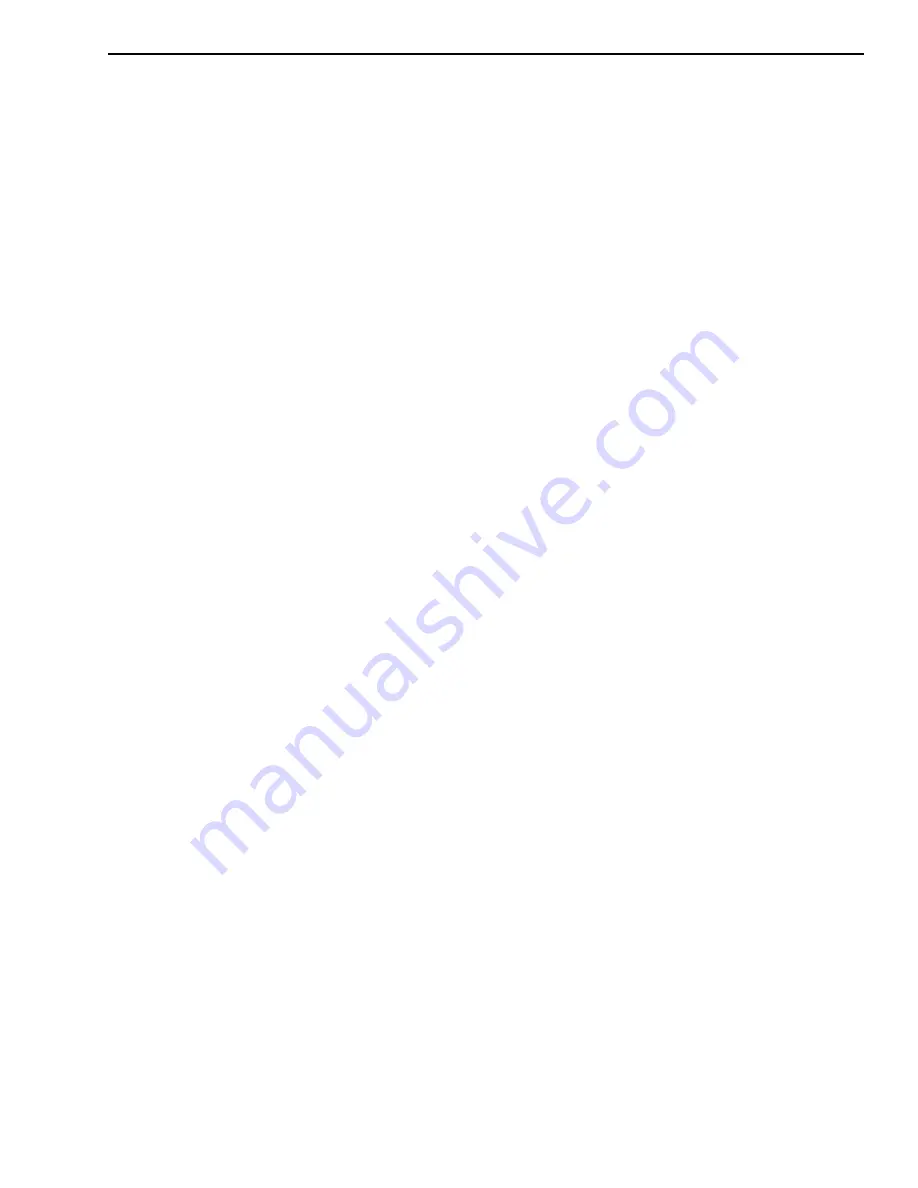
CHAPTER 8 - SPECIFICATIONS
8-3
6-34551NA
Issued 8-04 Bur
ENGINES
CX75SR, CX80
Make ................................................................................................................................................................. ISUZU
Type .............................................................................................................................................................. CC-4JG1
Number of cylinders................................................................................................................................................... 4
Bore/stroke ............................................................................................................ 95.4mm x 107 mm (3.76” x 4.21”)
Displacement.............................................................................................................................. 3059 cm3 (187 CID)
Power EEC 80/1269 ............................................................................................................................39.1 kW/53 HP
Speed rating .................................................................................................................................................2100 rpm
CX135SR
Make ................................................................................................................................................................. ISUZU
Type ........................................................................................................................................................... BB-4BG1T
Turbo...................................................................................................................................................................... yes
Electronically controlled ..................................................................................................................................injection
Number of cylinders................................................................................................................................................... 4
Bore/stroke ............................................................................................................ 105 mm x 125 mm (4.13” x 4.92”)
Displacement.............................................................................................................................. 4329 cm3 (264 CID)
Power EEC 80/1269 ............................................................................................................................65.6 kW/89 HP
Speed rating .................................................................................................................................................2100 rpm
ELECTRICAL SYSTEMS
CX75SR, CX80
Circuit ..............................................................................................................................................................12 volts
Battery ............................................................................................................................................ 1 x 12 volts/72 Ah
Alternator ............................................................................................................................................................. 50 A
CX135SR
Circuit ..............................................................................................................................................................24 volts
Batteries ......................................................................................................................................... 2 x 12 volts/64 Ah
Alternator .............................................................................................................................................. 24 volts/50 Ah
Circuit fitted with watertight connectors.
Summary of Contents for CX135SR
Page 6: ...IV Issued 8 04 Bur 6 34551NA CHAPTER 9 INDEX...
Page 12: ...CHAPTER 1 GENERAL INFORMATION 1 6 Issued 8 04 Bur 6 34551NA NOTES...
Page 14: ...CHAPTER 2 SAFETY DECALS AND HAND SIGNALS 2 2 Issued 8 04 Bur 6 34551NA NOTES...
Page 60: ...CHAPTER 3 INSTRUMENTS AND CONTROLS 3 32 Issued 8 04 Bur 6 34551NA...
Page 62: ...CHAPTER 4 OPERATING INSTRUCTIONS 4 2 Issued 8 04 Bur 6 34551NA...
Page 82: ...CHAPTER 4 OPERATING INSTRUCTIONS 4 22 Issued 8 04 Bur 6 34551NA NOTES...
Page 132: ...CHAPTER 5 LUBRICATION FILTERS AND FLUIDS 5 50 Issued 8 04 Bur 6 34551NA NOTES...
Page 134: ...CHAPTER 6 MAINTENANCE AND ADJUSTMENTS 6 2 Issued 8 04 Bur 6 34551NA...
Page 152: ...CHAPTER 6 MAINTENANCE AND ADJUSTMENTS 6 20 Issued 8 04 Bur 6 34551NA NOTES...
Page 154: ...CHAPTER 7 ELECTRICAL 7 2 Issued 8 04 Bur 6 34551NA NOTES...
Page 164: ...CHAPTER 8 SPECIFICATIONS 8 2 Issued 8 04 Bur 6 34551NA...
Page 183: ...CHAPTER 8 SPECIFICATIONS 8 21 6 34551NA Issued 8 04 Bur NOTES...
Page 184: ...CHAPTER 8 SPECIFICATIONS 8 22 Issued 8 04 Bur 6 34551NA...