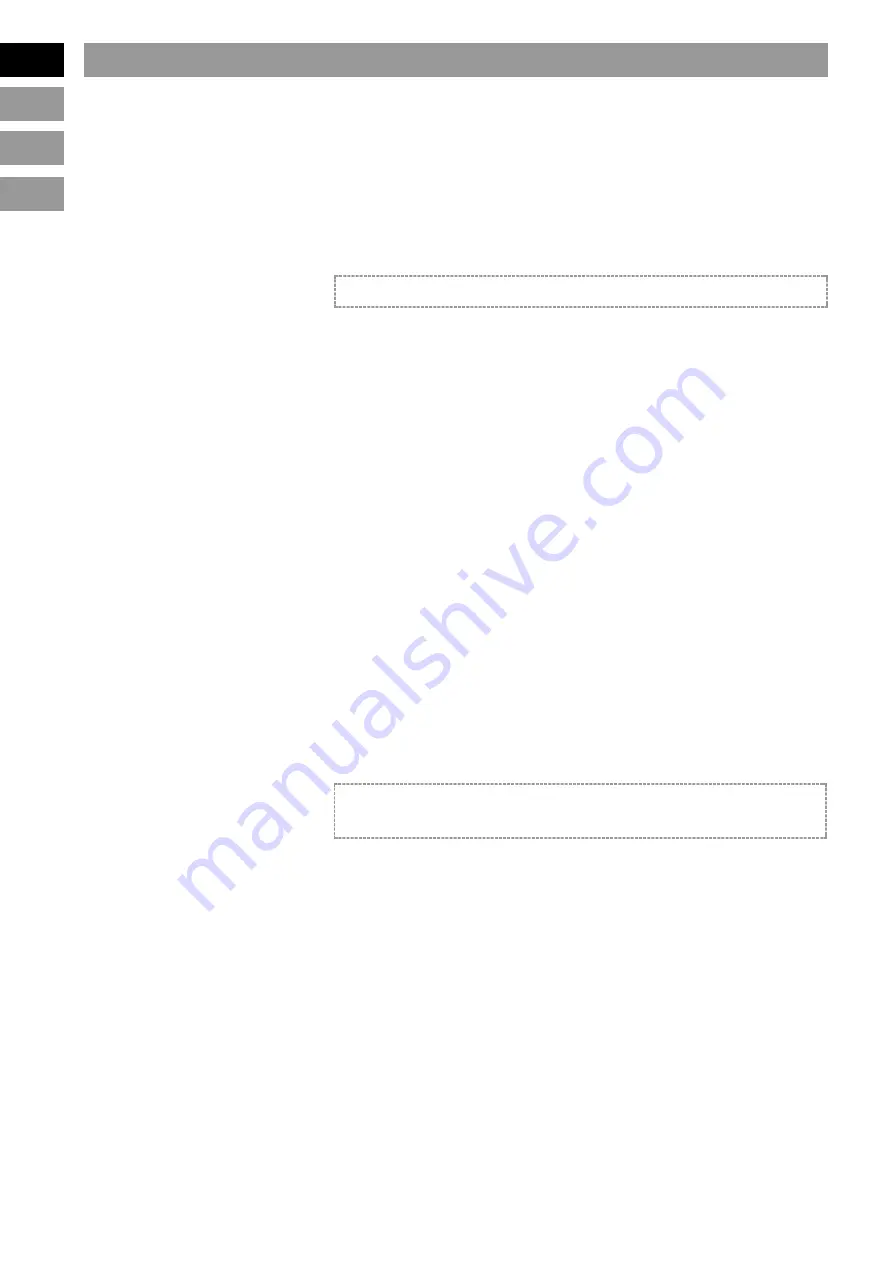
12
GB
D
F
I
A
dequate maintenance is an important factor to ensure the long life and optimum
performance of the unit and the safety conditions required by the Manufacturer.
9.1 General maintenance
It is essential to clean the condenser which is located in the front of the compressor unit
(externally to the cell) in an easily accessible position. The condenser is used to cool
the refrigerating gas and it will work more effectively if it is kept free of dust.
The unit can be cleaned by simply using a dry brush and reaching deep between
the condenser’s fins or, better still, by using an air jet and blowing from the inside
out. This operation must be carried out while the unit is switched off.
If there are traces of oil on the condenser, check where they come from and,
having repaired the leak, clean using a detergent such as alcohol or petrol.
WARNING:
To avoid cutting your hands, use protective gloves.
9.2 Special maintenance operations
Periodically check the wear of electrical contacts and remote control switches
and replace if necessary.
9.3 Operations to be carried out
Below is a list of maintenance operations that require specific technical compe-
by qualified personnel or by
tencies and must therefore be carried out by qualified personnel or by the
the Manufacturer
Manufacturer.
The User must on no account:
- replace electrical components
- tamper with the electric system
- make repairs on mechanical parts
- tamper with the refrigerating system
- tamper with the control panel
- tamper with safety and protection devices
9.4 Troubleshooting guide
Technical problems that may occur during the operation of the machine:
1.
In case of
malfunction of the system
, check the refrigerating gas through the flow
indicator located on all units (this must be checked when the unit is operating and the
cell temperature is close to the required temperature). Normally the indicator is clear,
while, in the absence of gas, gas bubbles will appear.
2.
If the
compressor or fan stop
, check the following:
- whether the safety fuses of the main and auxiliary circuit have been blown, in
which case they should be replaced, after checking the suitability of the mains
tension and ensuring that phase polarity is correct.
- if the compressor unit has stopped working (the indicator light on the panel is
on) it is necessary to reset the thermal relay manually, having first identified the
causes of the malfunction.
WARNING:
It absolutely forbidden to remove the safety devices provided by the anufacturer
to protect operators while the machine is in operation.
3.
Other malfunctions may be due to the triggering of the following electrical
safety devices:
a) Fan thermal protection
(incorporated in the motor) - automatic resetting. This devi-
ce is designed to safeguard electrical fans against excessive current absorption due to:
- overheating
- lack of one phase (only for three phase models)
- dirt in the condenser
b) High pressure switch
- manual resetting
It is designed to protect the compressor from excessive pressure, which cause
the pressure switch to be triggered too often, deriving from:
- dirt in the condenser
- condenser fans not working
- excessive temperature in the room where the system is located
- use of the system in unsuitable conditions or with inappropriate products.
To reset press the button on the pressure switch.
c) Low pressure switch
- automatic resetting
It is generally used to stop the unit working in pump-down mode.
The triggering of the pressure switch can also indicate excessively low pressure
99.. M
MAAIIN
NTTEEN
NAAN
NC
CEE AAN
ND
D RREEPPAAIIRRSS
99.. M
MAAIIN
NTTEEN
NAAN
NC
CEE AAN
ND
D RREEPPAAIIRRSS
Summary of Contents for CU-S 401
Page 21: ...57...
Page 24: ...0MAN126A 04 2 2 001...