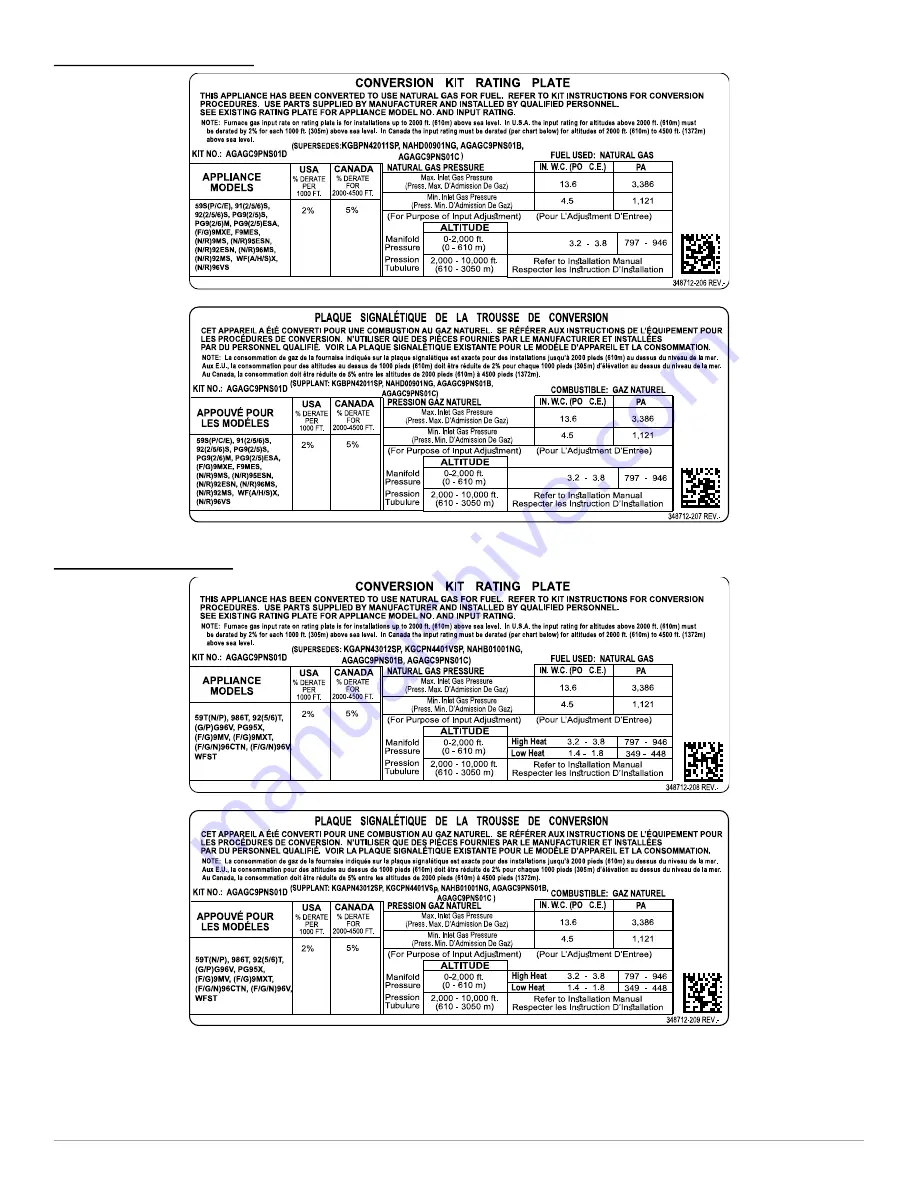
AGAGC9PNS01D Gas Conversion Kit, Propane to Natural: Installation Instructions
Manufacturer reserves the right to change, at any time, specifications and designs without notice and without obligations.
6
SINGLE-STAGE GAS VALVE
A221025
A221025FR
Fig. 5 – Conversion Kit Rating Plate (40,000 BTUh to 140,000 BTUh ONLY) Single-Stage Furnace
TWO-STAGE GAS VALVE
A221024
A221024FR
Fig. 6 – Conversion Kit Rating Plate (40,000 BTUh to 140,000 BTUh ONLY) Two-Stage Furnace