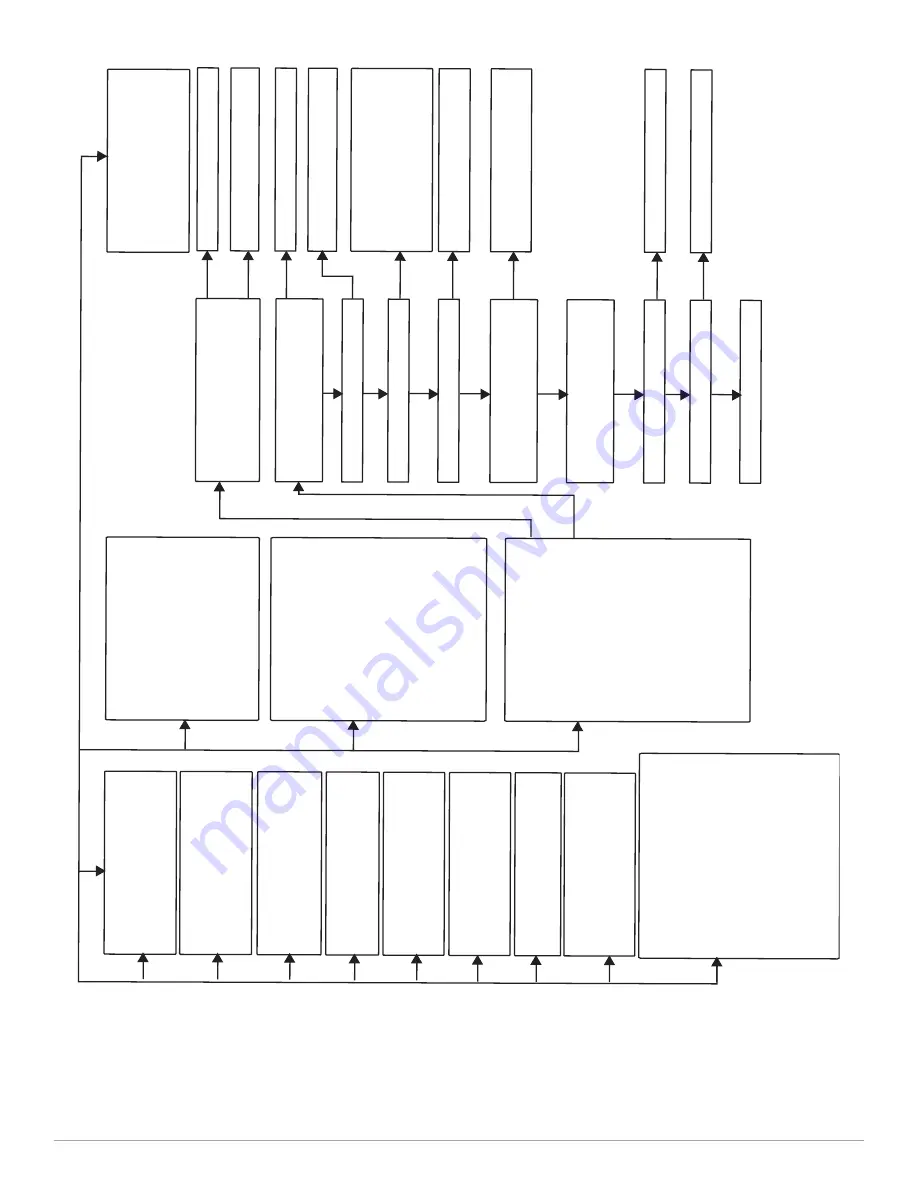
58SP0A/58SP1A: Installation, Start–Up, Operating and Service and Maintenance Instructions
Manufacturer reserves the right to change, at any time, specifications and designs without notice and without obligations.
43
A200304
Fig. 52 – Troubleshooting Guide
11
NO PREVIOUS CODE – Stored codes
are erased
after 72 hours
. On RED LED
boards stored status codes can also be
erased whene
v
er po
wer (115V or 24V
)
is interr
upted.
Run system through a
heating or cooling cycle to chec
k system.
12
BLO
WER ON AFTER PO
WER UP –
(115V OR 24V) – Nor
mal operation.
Bl
o
w
er r
uns f
or 90 seconds
, if unit is
po
wered up dur
ing a call f
or heat (R-W
closed) or when (R-W opens) dur
ing
the
b
lo
w
er on-dela
y per
iod.
1
3
LIMIT CIRCUIT LOCK
OUT – Loc
kout
occurs if the limit, draft saf
eguard, flam
e
rollout, or b
loc
ked v
ent s
witch*(if used) is
open longer than 3 minutes
. Control will
auto-reset after 3 hours
. See code 33.
1
4
IGNITION LOCK
OUT – System f
ailed to
ignite gas and pro
ve flame in 4 attempts
.
Control will auto-reset after 3 hours
.
See status code 34.
21
GAS HEA
TING LOCK
OUT –
T
ur
n off
po
wer and w
ait 5 minutes to retr
y.
Chec
k f
or
:
-S
tu
ck
c
losed gas v
alv
e rela
y on control.
-
M
is
wire or shor
t to gas v
alv
e wire
.
2
2
ABNORMAL FLAME-PR
O
VING SIGNAL
Flame is pro
v
ed while gas v
alv
e is de-
energiz
ed.
Inducer will r
un until f
ault is
cleared.
Chec
k f
or
:
-
S
tuc
k open or leaky gas v
alv
e
.
23
PRESSURE SWITCH DID NO
T OPEN
Chec
k f
or
:
-
O
bstr
ucted pressure tube
.
-
P
ressure s
witch stuc
k closed.
2
4
SECOND
AR
Y V
O
LTA
GE FUSE IS OPEN
Chec
k f
or
:
-
S
hor
t circuit in secondar
y v
oltage (24V)
wir
ing including ther
mostat leads
.
Disconnect ther
mostat leads to isolate
shor
t circuit.
3
1
PRESSURE SWITCH DID NO
T CLOSE
OR REOPENED – If open longer than
5
minute
s
, inducer shuts off f
or 15 minute
s
bef
ore retr
y.
If opens dur
ing b
lo
w
er on-
dela
y
per
iod,
b
lo
w
er will come on
fo
r th
e
selected b
lo
w
er off-dela
y.
Chec
k f
or
:
-
Proper v
ent sizing.
-
Lo
w inducer v
oltage (115V).
-
Lo
w inlet gas pressure (if LGPS used).
-
Inadequate comb
ustion air supply
.
-
D
isconnected or obstr
ucted pressur
e
tubing.
-
Def
ectiv
e inducer motor
.
-
Def
ectiv
e pressure s
witch.
-
Excessiv
e wind.
-
Restr
icted v
ent.
33
LIMIT CIRCUIT F
A
UL
T – Indicates the
limit, draft saf
eguard, flame rollout, or
b
loc
k
ed v
ent shutoff s
witch* (if used) is
open.
Blo
w
er will r
un f
or 4 minutes or
until open s
witch remak
es whiche
v
er is
longer
. If open longer than 3 minutes
,
code changes to loc
k
out #13.
If open
less than 3 min.
status code #33
continues to flash until b
lo
w
er shuts off
.
Flame rollout s
w
itch and BVSS requires
manual reset.
Chec
k f
or
:
-
Dir
ty filter or restr
icted duct system.
-
Loose b
lo
w
er wheel.
-
Def
ectiv
e s
witch or connections
.
-
Def
ectiv
e b
lo
w
er motor or capacitor
.
-
Inadequate comb
ustion air supply
(flame rollout s
witch open).
-
Restr
icted v
ent.
-
Proper v
ent sizing.
-
Excessiv
e wind.
3
4
IGNITION PR
O
VING F
AILURE – If flame
is not sensed dur
ing the tr
ial f
or ignition
per
iod,
the control will repeat the ignition
sequence 3 more times bef
ore loc
k
out
#14 occurs
. If flame signal is lost during
the b
lo
w
er on-dela
y per
iod, b
lo
w
er will
come on f
or the selected b
lo
w
er off-dela
y.
Chec
k the f
ollo
w
ing items first bef
ore
proceeding to the ne
xt step
.
-G
a
s
v
alv
e tur
ned off
.
-
Manual shut-off v
al
ve
.
-
G
reen/Y
ello
w
wire MUST
be connected
to fur
nace sheet metal.
-
F
lame sensor must not be grounded.
T
o deter
mine whether the prob
lem is in
the gas v
a
lv
e
, igniter
, or flame sensor the
system can be operated
in the component
test mode to chec
k the igniter
. First
remo
ve the R ther
mostat connection from
the control and initiate the component
test sequence
. Does the igniter glo
w
orange/white
b
y the end of the 15 second
w
ar
m
-up per
iod?
Unplug igniter har
ness f
rom control and
initiate
another component test sequence
. Chec
k
for 115V between
pin 1 and
NEUTRAL-L2 on
the control.
W
as 115V present f
or the 15
second per
iod?
Reconnect the R ther
mostat lead and set
ther
mostat to call f
or heat.
Connect v
oltmeter
across gas v
alv
e connections
. Does gas v
a
lv
e
receiv
e 24V?
Does gas v
alv
e open and allo
w gas to flo
w?
Do the main b
ur
ners ignite?
Do the main b
ur
ners sta
y on?
Repeat call f
or heat and chec
k flame sensor
current dur
ing tr
ial f
or ignition per
iod.
Is the
DC microamps belo
w 0.5?
Is current near typical v
alue?
Will main b
ur
ners ignite and sta
y on?
Fix
ed.
Clean flame sensor with fine steel wool and
rechec
k current.
Nominal current is 4.0 to 6.0
microamps
.
45
CONTR
OL CIRCUITR
Y LOCK
OUT
A
uto-reset after 1 hour loc
k
out due to:
-
Flame circuit f
ailure
.
-
Gas v
alv
e rela
y stuc
k open.
-
Softw
are chec
k error
.
Reset po
wer to clear lo
c
k
out.
Replace
control if code repeats
.
Replace fur
nace control.
Chec
k f
or continuity
in the har
ness and igniter
.
Replace def
ectiv
e component.
Chec
k connections
. If OK, replace control
.
Chec
k that all gas v
alv
es are tur
ned on.
Replace v
alv
e
.
Chec
k f
or
:
-
Inadequate flame carr
y
o
v
er or rough
ignition.
-
Lo
w
inlet gas pressure
.
-
P
roper fir
ing rate
.
-
Bloc
k
ed or incorrect carr
y- o
v
er gap
.
(.045”
nominal)
All
ow
b
lo
w
er to come on and repeat test to
chec
k f
or inter
mittent operation.
Chec
k connections and retr
y.
If current is
near typical v
alue (4.0-6.0 nominal) and
b
ur
ners will not sta
y on, replace control.
Replace electrode
.
Replace fur
nace control.
* Bloc
k
ed v
ent shutoff s
witch used in Chimne
y Adapter Kit
YES
YES
YES
YES
NO
YES
YES
YES
NO
YES
NO
NO
NO
YES
NO
NO
NO
NO
25 - INV
ALID MODEL
SELECTION OR SETUP
ERROR - If status
code 25 only flashes 4 times on power-up the
control is missing its model plug PL4 and is
defaulting to the model selection stored in
memory
. If status code 25 flashes continu-
ously it could indicate any of the following:
Model plug PL4 is missing and there is no
valid model stored in permanent memory
.
This
will happen if you forget to install the model
plg PL4 on a service replacement control.
-
Thermostat call with SW1-1 ON.
-
Thermostat call with SW1-6 ON.
- SW1-1 and SW1-6 both ON.
-
T
wo dif
ferent furnace models twinned.
- If replacing a control, be sure to use correct
version (V##) located on control board
Models supported should be listed.