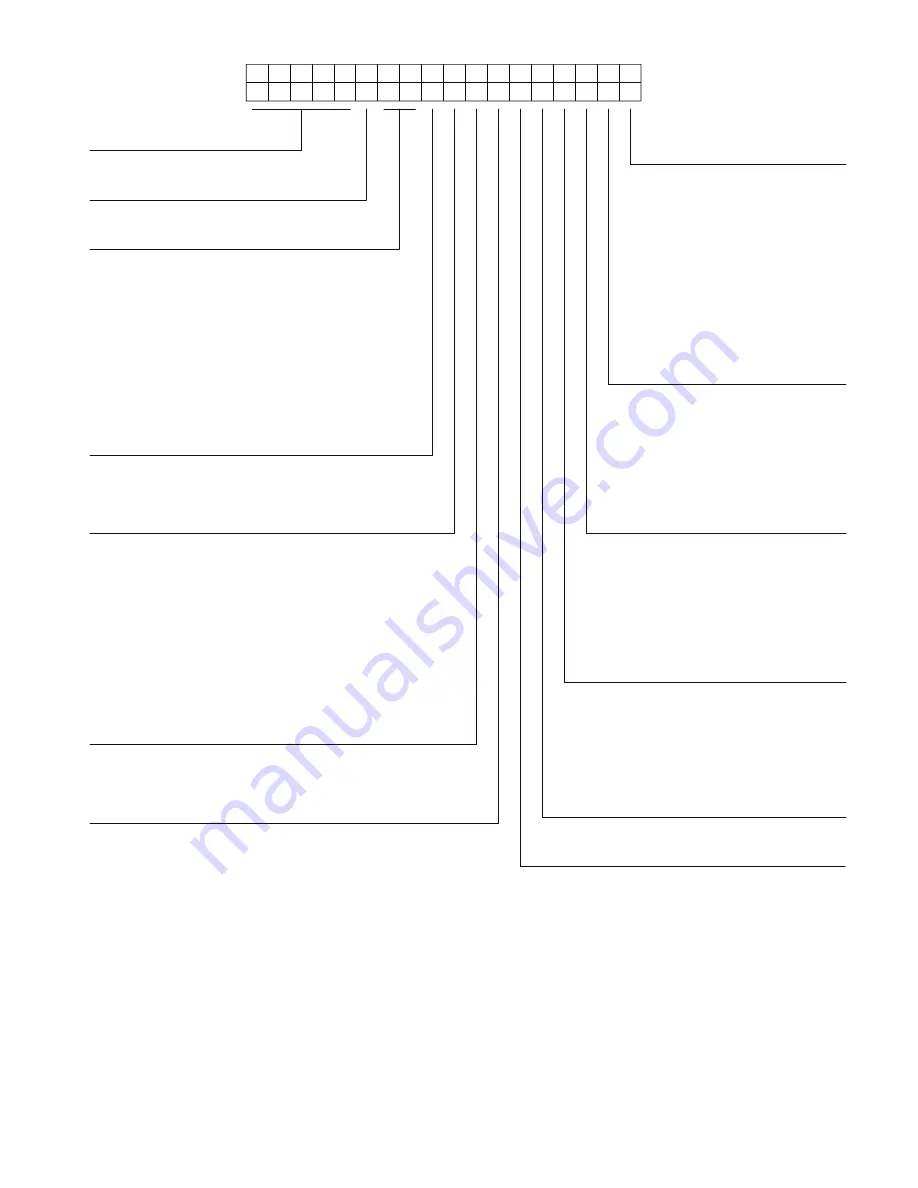
3
Fig. 1 —
50HCQ12 Model Number Nomenclature (Example)
5
0
H
C
Q
D
1
2
A
1
A
6
–
0
B
2
A
0
Cooling Tons
12 - 10 ton
1
Example:
Position:
2
3
4
5
6
7
8
9
10 11 12 13 14 15 16 17 18
Sensor Options
A = None
B = RA Smoke Detector
C = SA Smoke Detector
D = RA + SA Smoke Detector
E = CO
2
F = RA Smoke Detector and CO
2
G = SA Smoke Detector and CO
2
H = RA + SA Smoke Detector and CO
2
J = Condensate Overflow Switch
K = Condensate Overflow Switch and RA Smoke Detectors
L = Condensate Overflow Switch and
RA and SA Smoke Detectors
Indoor Fan Options
1 = Standard Static Option – Belt Drive
2 = Medium Static Option – Belt Drive
C = High Static Option with High Efficiency Motor – Belt Drive
Coil Options (Outdoor – Indoor – Hail Guard)
A = Al/Cu – Al/Cu
B = Precoat Al/Cu – Al/Cu
C = E-coat Al/Cu – Al/Cu
D = E-coat Al/Cu – E-coat Al/Cu
E = Cu/Cu – Al/Cu
F = Cu/Cu – Cu/Cu
M = Al/Cu – Al/Cu – Louvered Hail Guard
N = Precoat Al/Cu – Al/Cu – Louvered Hail Guard
P = E-coat Al/Cu – Al/Cu – Louvered Hail Guard
Q = E-coat Al/Cu – E-coat Al/Cu – Louvered Hail Guard
R = Cu/Cu – Al/Cu – Louvered Hail Guard
S = Cu/Cu – Cu/Cu – Louvered Hail Guard
Voltage
1 = 575/3/60
5 = 208-230/3/60
6 = 460/3/60
Design Revision
– = Factory Design Revision
Base Unit Controls
0 = Electro-mechanical Controls can be used with W7212
EconoMi$er
®
IV (Non-Fault Detection and Diagnostic)
1 = PremierLink
TM
Controller
2 = RTU Open Multi-Protocol Controller
6 = Electro-mechanical with W7220 Economizer
controller Controls. Can be used with W7220
EconoMi$er X (with Fault Detection and Diagnostic)
Intake / Exhaust Options
A = None
B = Temperature Economizer w/ Barometric Relief
F = Enthalpy Economizer w/ Barometric Relief
K = 2-Position Damper
U = Temperature Ultra Low Leak Economizer w/
Barometric
Relief
W = Enthalpy Ultra Low Leak Economizer w/
Barometric
Relief
Service Options
0 = None
1 = Unpowered Convenience Outlet
2 = Powered Convenience Outlet
3 = Hinged Panels
4 = Hinged Panels and
Unpowered Convenience Outlet
5 = Hinged Panels and
Powered Convenience Outlet
Packaging Options
0 = Standard
1 = LTL
Electrical Options
A = None
C = Non-Fused Disconnect
D = Thru-The-Base Connections
F = Non-Fused Disconnect and
Thru-The-Base
Connections
G = 2-Speed Indoor Fan (VFD) Controller
J = 2-Speed Indoor Fan (VFD) Controller
and Non-Fused Disconnect
K = 2-Speed Indoor Fan (VFD) Controller
and Thru-The-Base Connections
M = 2-Speed Indoor Fan (VFD) Controller
with Non-Fused Disconnect and
Thru-The-Base
Connections
Refrig. Systems Options
D = Two Stage Cooling Models
Unit/Series/Model
50HCQ - Packaged Rooftop Heat Pump
Summary of Contents for 50HCQ12
Page 4: ...4 Fig 2 Unit Dimensional Drawing Size 12 Units ...
Page 5: ...5 Fig 2 Unit Dimensional Drawing Size 12 Units cont ...
Page 9: ...9 Fig 6 Roof Curb Details REV 50TM500827 ...
Page 25: ...25 Fig 42 Typical 50HCQ Control Wiring Diagram ...
Page 26: ...26 Fig 43 Typical 50HCQ Power Wiring Diagram 208 230 3 60 unit shown ...
Page 27: ...27 Fig 44 PremierLink Controller Wiring Schematic ...
Page 28: ...28 Fig 45 RTU Open Controller System Wiring Diagram ...