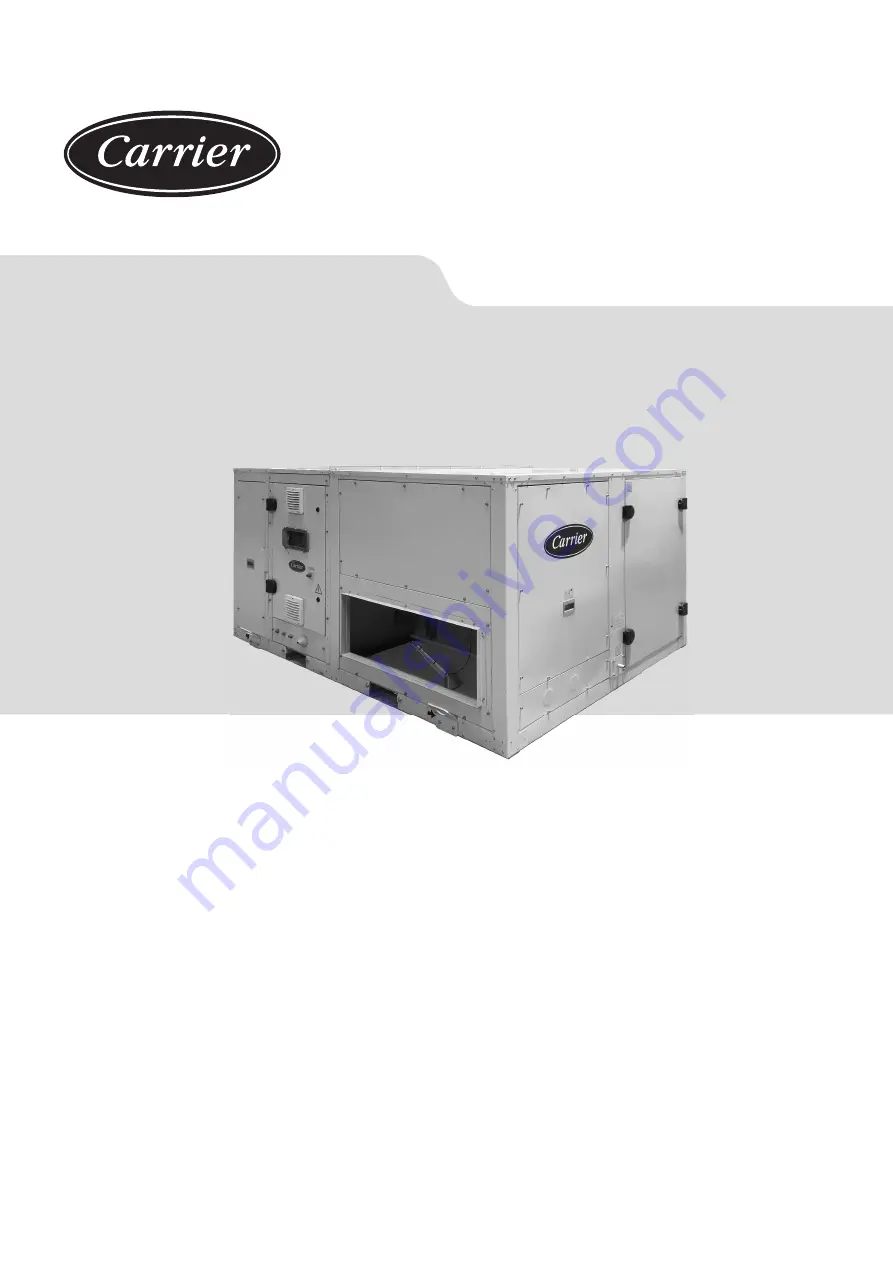
I N S TA L L AT I O N, O P E R AT I O N A N D
M A I N T E N A N C E I N S T R U C T I O N S
Translation of the original document 80185, 09.2022
Packaged rooftop units
Nominal cooling capacity R-410A 22.3 - 97.0 kW
Nominal heating capacity R-410A 21.9 - 99.6 kW
Nominal cooling capacity R-454B 36.0 - 90.4 kW
Nominal heating capacity R-454B 35.9 - 89.6 kW
50FF 020-093
50FC 020-099
Summary of Contents for 50FC 020-099
Page 78: ...78 Notes ...
Page 79: ......