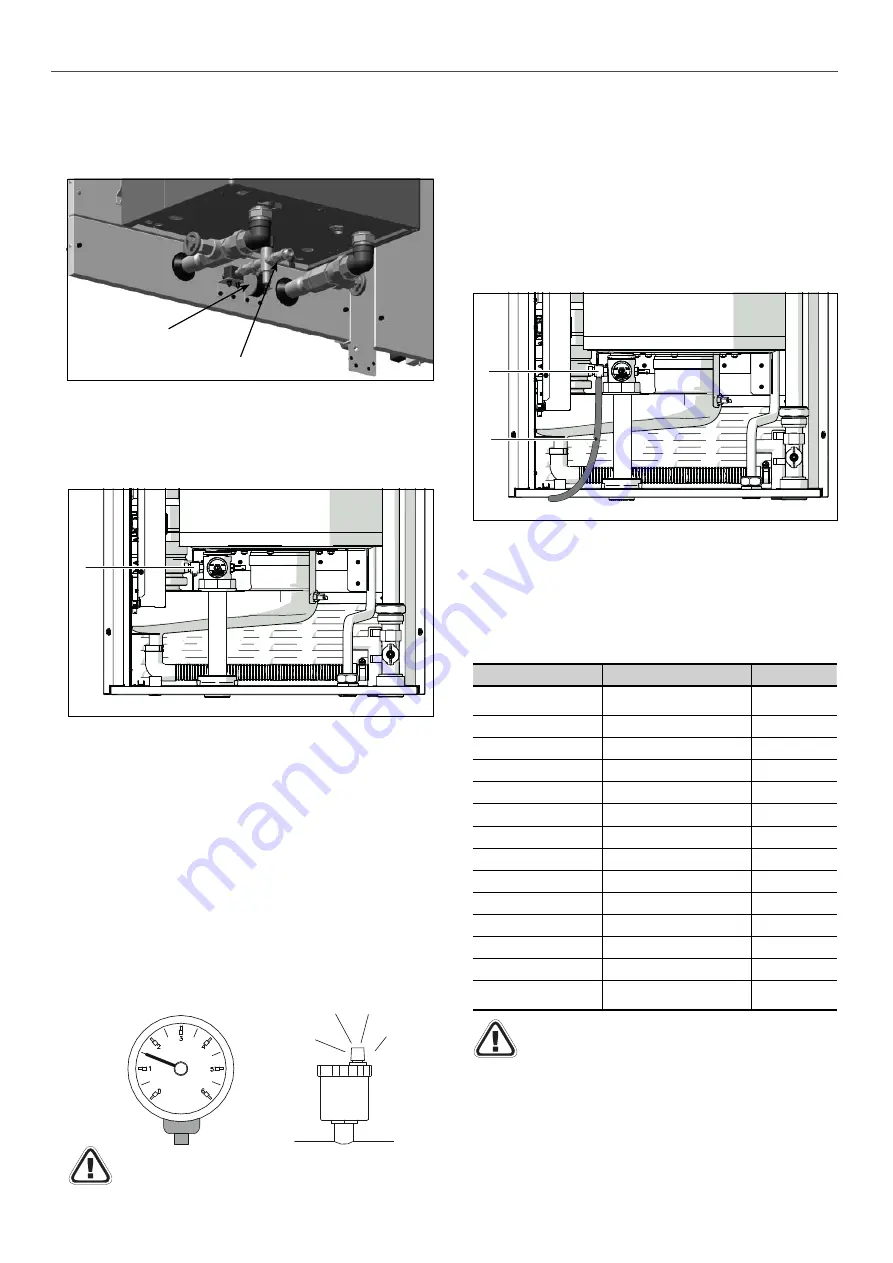
54
Hydraulic circuit
■
Circuit
fi
lling
The charging system is connected to the boiler’s return line.
Automatic
fi
lling valve 1/2”.
■
Circuit emptying
In case of long unit stops, and forcibly if they happen in the
winter season, the circuit must be emptied.
- Before emptying the system, switch-o
ff
the thermal module’s
switch (0) and switch-o
ff
the magnetothermic switch placed
in the electrical cabinet of the 50FF/FC unit.
- Close the water supply shut-o
ff
cocks.
- In order to empty the boiler,
fi
t a rubber hose (5) (inner
diameter int. Ø = 12 mm) to the thermal module’s discharge
valve (1).
Filling valve
Pressure gauge
- Before
fi
lling the system, switch-o
ff
the thermal module’s
switch (0) and switch-o
ff
the magnetothermic switch placed
in the electrical cabinet of the 50FF/FC unit.
- Make sure that drain cocks (1) are closed before to start the
load of the system.
Immediately repair any leaks or drips that could result
in air entering the system.
1
IIII
FID
FID
FFFID
FID
FID
FID
FID
FID
FID
- Unscrew the vent valve’s release cap.
- Open the shut-o
ff
cocks in order to slowly
fi
ll the system.
- Use the pressure gauge to check that the pressure is rising
and the water is exiting through the vent valves.
- Close the shut-o
ff
cocks after the pressure reaches 1.5 bar.
- Start-up the circulation pump. This operation can be
performed manually from a screen of the “50FC” electronic
control (on a screen of the “Service menu”, password
protected).
- During this stage, check that the air is correctly eliminated.
- Restore the pressure if necessary.
- Stop the pump and start-up again.
- Repeat the last three steps until the pressure is stabilised.
Excessive pressure
fl
uctuations can cause stress and fatigue
to the heat exchanger. Keep the operating pressure constant.
1
IIII
FID
FID
FFFID
FID
FID
FID
FID
FID
FID
5
N
Parameter
Value
Unit
General characteristic
Colourless, without
sediment
PH value
Min. 6,5 ; Max. 8,0
pH
Dissolved oxygen
< 0,05
mg/l
Total iron (Fe)
< 0,3
mg/l
Total copper (Cu)
< 0,1
mg/l
Na2SO3
< 10
mg/l
N2H4
< 3
mg/l
PO4
< 15
mg/l
CaCO3
Min. 50 ; Max. 150
ppm
Trisodium phosphate
None
ppm
Chlorine
< 100
ppm
Electrical conductivity
<200
μ
Siemens/cm
Pressure
Min. 0.6 ; Max. 6
bar
Glycol
Max. 20%
(only propylene glycol)
%
All data in the table refer to water contained in the
system after 8 weeks’ operation.
To prevent the water from freezing, with this option the 50FF/
FC unit always has an anti-freezing thermostat. Add glycol to
the water if necessary (only
propylene glycol
).
Do not use excessively softened water. Excessive water
softening (total hardness < 5° f) results in corrosion due
to contact with metal elements (pipes or thermal module
components).
■
Water quality requirements
It is ABSOLUTELY NECESSARY to treat the water system in
order for the heat generator to work properly and to guarantee
its service life, as well as that of all its components.
The water used for the central heating circuit must conform to
the quality parameters given in the following table:
12 - FACTORY OPTIONS AND ACCESSORIES
Summary of Contents for 50FC 020-099
Page 78: ...78 Notes ...
Page 79: ......