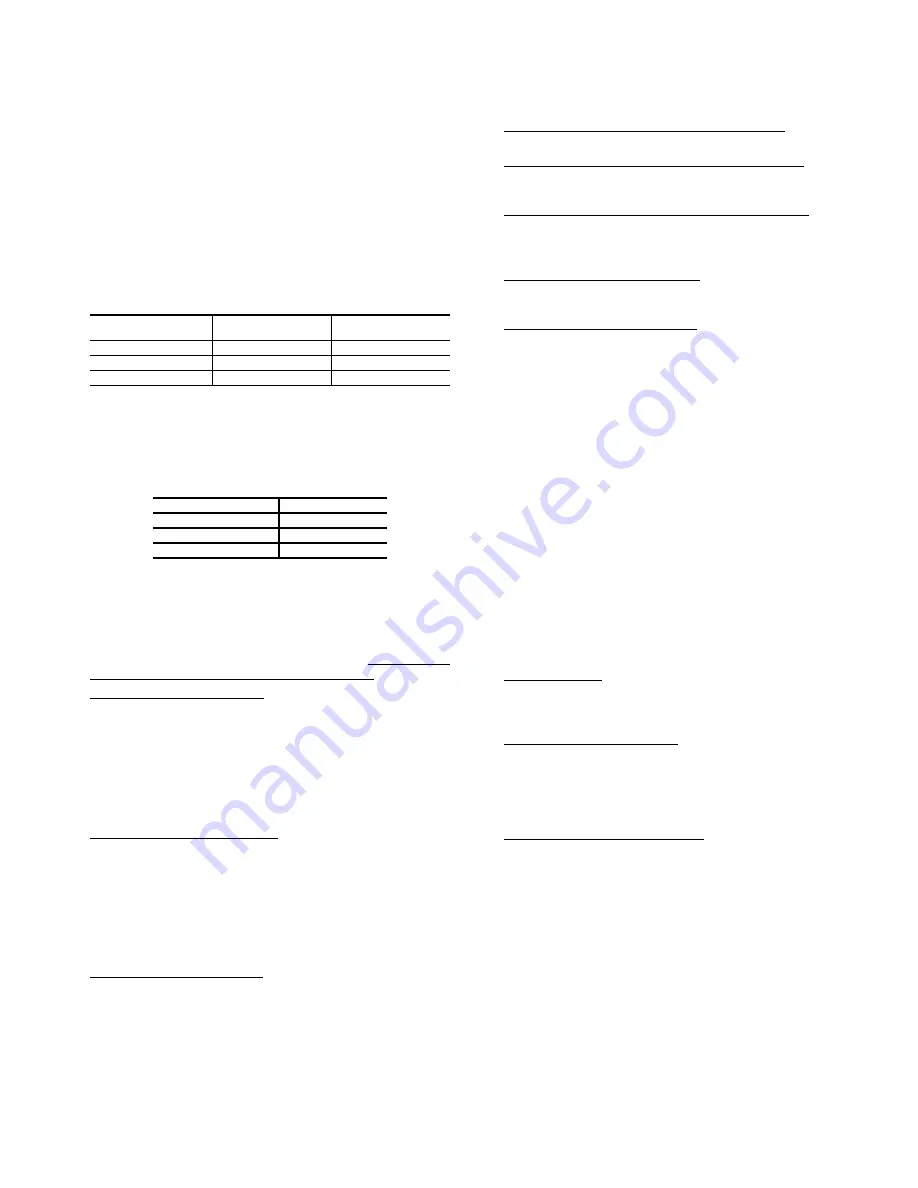
45
SPACE SENSOR CONTROL — If the unit is in cooling,
operating under space temperature control, the economizer is
available for cooling, and no compressors are operating, the
economizer will control the SAT to either
Setpoints
→
LCSP
or
Setpoints
→
HCSP
(see Table 40). If a compressor is ON, the
economizer will try to position itself at the economizer maxi-
mum cooling position (
Configuration
→
ECON
→
EC.MX
).
If the control senses low suction pressure for any active re-
frigerant circuit when the economizer is also providing cooling,
the maximum allowable economizer position will be reduced.
Factory default configurations have been qualified over a large
range of conditions and should only be changed with care. For
unit troubleshooting, factory default maximum economizer
limits for this condition are provided in Table 41.
Table 40 — LCSP and HCSP Transitions for
Space Temperature Mode
LEGEND
Table 41 — Maximum Economizer Limits During
Low Suction Pressure
ECONOMIZER ACTUATOR COMMUNICATIONS — The
configuration Economizer Control Type determines the
communication method, either digital or analog, used to
communicate between the ECB and the economizer actuator.
Economizer Control Type is accessible via the Scrolling
Marquee at
Configurations
→
ECON
→
E.CTL
. The power to
the unit must be cycled after
E.CTL
is changed.
E.CTL =
1
(Digital/Position) — When
E.CTL
is set to 1, the
ECB will communicate with the economizer actuator using the
digital protocol. The ECB 4 to 20 mA output will represent the
actuator’s actual position. Because the wiring has a built-in
500-ohm resistor, the 4 to 20 mA signal is converted to a 2 to
10-v signal that is accessible via field connection terminal board
TB2-8 and TB2-9. However, before this signal can be read, the
violet wire that connects the actuator to field connection termi-
nal board TB2-J10-8 must be removed or cut.
E.CTL =
2
(Digital/Command) — When
E.CTL
is set to 2,
the ECB will communicate with the economizer actuator using
the digital protocol. The ECB 4 to 20 mA output will represent
the actuator’s commanded position. Because the wiring has a
built-in 500-ohm resistor, the 4 to 20 mA signal is converted to
a 2 to 10-v signal that is accessible via field connection termi-
nal board TB2-8 and TB2-9. However, before this signal can
be read, the violet wire that connects the actuator to field con-
nection terminal board TB2-J10-8 must be removed or cut.
E.CTL =
3
(Analog Control) — When
E.CTL
is set to 3, the
ECB will communicate with the economizer actuator using the
4 to 20 mA analog signal wired to TB2-8 and TB2-9 along
with the 500-ohm resistor producing a 2 to 10-v signal for the
actuator. While in this mode, the actuator’s built-in 2 to 10-v
feedback signal is accessible via TB2-9 and TB2-10.
UNOCCUPIED FREE COOLING — The unoccupied free
cooling algorithm attempts to maintain the building space at
the occupied cooling set point during unoccupied periods if the
conditions in the building and the outdoors are suitable. Three
different configurations define this algorithm: Unoccupied
Free Cooling (
Configuration
→
ECON
→
UEFC
), Free Cool-
ing Preoccupancy Time (
Configuration
→
ECON
→
FC.TM
)
and Free Cool Low Temp Limit (
Configuration
→
ECON
→
FC.LO
).
Configuration
→
ECON
→
UEFC
= 0
(Disabled) — When
UEFC
= 0
, unoccupied free cooling is disabled.
Configuration
→
ECON
→
UEFC
= 1
(Unoccupied) — When
UEFC
= 1
, unoccupied free cooling can occur whenever the
building is unoccupied.
Configuration
→
ECON
→
UEFC
= 2
(Preoccupancy) — When
UEFC
= 2
, unoccupied free cooling can only occur when the
time to the next occupied period is less than
Configuration
→
ECON
→
FC.TM
minutes.
Configuration
→
ECON
→
FC.TM
—
FC.TM
is the configura-
tion that determines how many minutes before occupancy that
free cooling can occur.
Configuration
→
ECON
→
FC.LO
— Unoccupied free cooling
cannot occur if the Outdoor Air Temperature (
Tempera-
ture
→
AIR.T
→
OAT
) is less than
FC.LO
.
POWER EXHAUST — To enable power exhaust,
Configu-
ration
→
ECON
→
PE.EN
must be set to
ENBL
. If power ex-
haust is enabled, Power Exhaust 1 will turn on when the econo-
mizer position is greater than the value of
Configuration
→
ECON
→
PE.1
. If power exhaust is enabled, Power Exhaust 2
will turn on when the economizer position is greater than the
value of
Configuration
→
ECON
→
PE.2
. There are small time
delays to ensure that rapid cycling does not occur.
Optional Humidi-MiZer™ Dehumidification Sys-
tem —
Units with the factory-equipped Humidi-MiZer
option are capable of providing multiple modes of improved
dehumidification as a variation of the normal cooling cycle.
The Humidi-MiZer option includes additional valves in the
liquid line and discharge line of each refrigerant circuit, a small
reheat condenser coil downstream of the evaporator, and
Motormaster® variable-speed control of some or all outdoor
fans. Operation of the revised refrigerant circuit for each mode
is described below.
NOTE: x = refrigerant circuit A or B.
Normal Cooling — Refrigerant flows from the outdoor
condenser through the de-energized 3-way valve (RH1.x) to
the expansion device. Reheat2 Valve (RH2.x) is closed. See
Fig. 6.
Reheat 1 (Subcooling Mode) — This mode increases latent
cooling and decreases sensible cooling compared to normal
cooling. Refrigerant flows from the outdoor condenser,
through the energized 3-way Valve (RH1.x), and through the
reheat condenser coil to the expansion device. Reheat2 Valve
(RH2.x) is closed. See Fig. 7.
Reheat 2 (Hot Gas Reheat Mode) — This mode provides
maximum latent cooling with little to no sensible capacity.
This mode can operate to provide dehumidification when there
is no cooling demand. Like Reheat 1 mode, refrigerant flows
from the outdoor condenser, through the energized 3-way valve
(RH1.x), and through the reheat condenser coil to the expan-
sion device. Reheat2 Valve (RH2.x) is open which provides
some compressor discharge gas to the reheat condenser to fur-
ther increase the reheat of the evaporator air stream. See Fig. 8.
Units with multiple circuits can operate with additional
staging of the cooling and dehumidification capacity. When
there is only cooling demand, based on a space temperature
sensor or thermostat, one or more circuits will operate in
normal cooling mode. When there is only dehumidification
demand, based on a space humidity sensor or switch, all
circuits will operate in reheat2 mode. When there is both
cooling demand and dehumidification demand, all circuits will
operate in either reheat1 or reheat2 mode, with the portion of
reheat1 circuits determined from the cooling demand.
CURRENT SAT
SET POINT
COOL DEMAND
(
∆
F)
NEXT SAT
SET POINT
LCSP
>0.5
HCSP
HCSP
<0
LCSP
LCSP
<–0.5
Exit Cooling
HCSP
—
High Cool Set Point
LCSP
—
Low Cool Set Point
SAT
—
Supply-Air Temperature
COOLING STAGE
LIMIT (%)
Bottom
50
Middle
50
Top
0
Summary of Contents for 48PG24
Page 68: ...68 Fig 14 Low Voltage Control Schematic 48PG20 28 Units without Humidi MiZer System a48 7627...
Page 69: ...69 Fig 15 Low Voltage Control Schematic 48PG20 28 Units with Humidi MiZer System a48 8227...
Page 70: ...70 Fig 16 Low Voltage Control Schematic 50PG20 28 Units without Humidi MiZer System a48 7778...
Page 71: ...71 Fig 17 Low Voltage Control Schematic 50PG20 28 Units with Humidi MiZer System a50 8101...
Page 72: ...72 Fig 18 Power Schematic Units without Humidi MiZer System a48 7628...
Page 73: ...73 Fig 19 Power Schematic Units with Humidi MiZer System a48 8228...
Page 74: ...74 Fig 20 Component Arrangement Units without Humidi MiZer System a48 8229...
Page 75: ...75 Fig 21 Component Arrangement Units with Humidi MiZer System a48 8230...
Page 105: ......