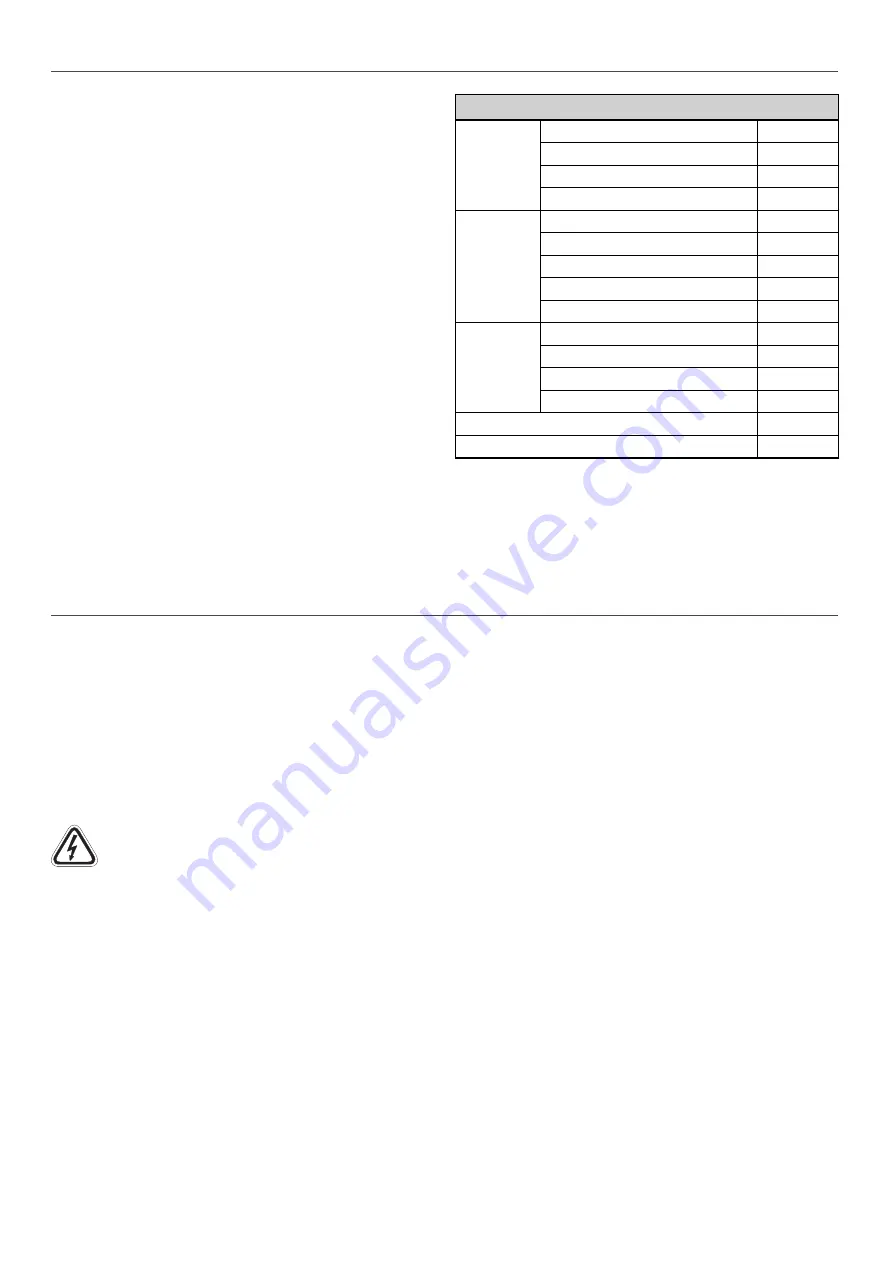
20
Operational checks
Cooling MODE
Compressor
Suction pressure
bar
Suction temperature (1)
ºC
Condensation pressure
bar
Condensation temperature (2)
ºC
Air condenser
Gas inlet temperature
ºC
Liquid outlet temperature (3)
ºC
Air inlet temperature
ºC
Outdoor temperature
ºC
Air outlet temperature
ºC
Water
evaporator
Water inlet temperature
ºC
Water outlet temperature
ºC
Liquid inlet temperature
ºC
Evaporator outlet temperature (4)
ºC
Subcooling (2) - (3)
ºC
Overheating (4) - (1)
ºC
The recording of these parameters whilst the unit is running allows
controlling the installation performance and it is the best possible
way to avoid breakdowns since the analysis of these data makes
early detection of anomalies possible or the provision of the
necessary means available to ensure that they do not take place.
Check the unit operation by verifying the electronic control and
the safety devices.
It is also recommendable to create a report, taking note of the
date, which includes the following information:
■
the nominal voltage,
■
current absorbed by the compressors, fans and other electrical
components.
■
signi
fi
cant temperatures in the cooling circuit (see attached
table),
■
other aspects considered interesting such as alarms detected
by the electronic control of the unit.
11 - COMMISSIONING
Recommendations
■
Do not lean on the unit. A platform must be used to work on
a level.
■
Do not lean on the copper refrigerant tubes.
■
Keep the unit clean.
■
Keep the space surrounding the unit clean and cleared in order
to avoid accidents and ensure the proper ventilation of the coil.
■
Perform a visual (remains of water or oil below or around the
unit) and auditory inspection of the entire installation.
■
In general, a corrosion control must be performed on the
metallic parts of the unit (frame, bodywork, exchangers, electric
panel, etc.).
■
Check that the insulation foam is not unstuck or torn.
12 - MAINTENANCE
The minimal maintenance operations and their periodicity will be
made according to the national regulations.
Any intervention on the electric cooling components must be made
by a quali
fi
ed and authorized technician.
Technicians who intervene with the unit must use the necessary
safety equipment (gloves, goggles, insulating clothing, safety
shoes, etc.).
Furthermore, if working around sources of signi
fi
cant noise, we
recommend the use of noise-dampening headgear.
Caution: Before intervening in the unit, cut o
ff
main
power.
Plate exchanger
■
The exchangers are
fi
tted with thermal insulation. Check that
the foam is not unstuck or broken.
■
The water quality and the pressure drop must be veri
fi
ed at
the exchanger level. After verifying the mesh
fi
lter condition,
if necessary, the exchanger must be cleaned. To this end, a
weak solution of phosphoric acid 5% must be circulated using
the high pressure pump. During optimum cleaning, the cleaning
solution
fl
ow must, as a minimum, be 1,5 times the working
fl
ow, preferably in the inverse circulation mode. This must be
followed by thorough rinsing with water to remove any acidic
residues. It is advisable to circulate a solution 1%-2% of sodium
hydroxide prior to the last rinsing in order to ensure that the acid
has been neutralised.
■
Any repair or modi
fi
cation to the plate exchanger is prohibited.
It can only be replaced by an original part.
Air coil
■
Check that the coil is free from dust and grease.
■
Cleaning the accumulated dust on the coil can be performed
with a vacuum cleaner perpendicular to the
fi
ns or with a low-
pressure water cleaner. Grease can be removed with water with
degreaser. Do not put stress on the
fi
ns as they could deform.
■
All the electric connection states must be checked as well, as
well as the air tightness of the di
ff
erent circuits.
Next, some recommendations are stated for performing the
maintenance and cleaning of the unit’s components.
Summary of Contents for 30PA 180
Page 27: ......