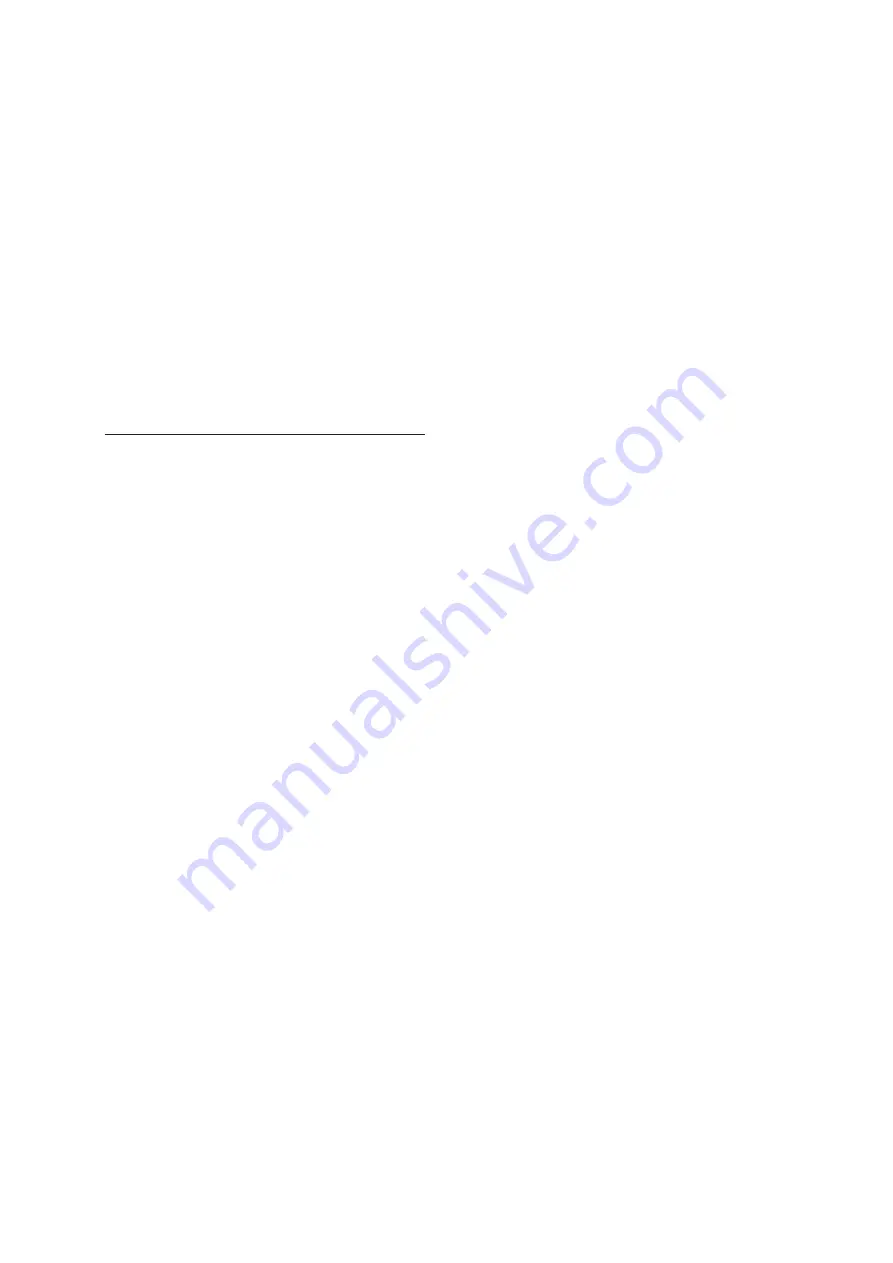
10
Power supply
The power supply must conform to the specification on the
chiller nameplate. The supply voltage must be within the range
specified in the electrical data table.
ATTENTION: Units 30GH/GZ 040-160 have only one power
connection point.
Units 30GH/GZ 170-245 have two power connection points.
For connections refer to the wiring diagrams.
WARNING: Operation of the chiller with an improper supply
voltage or with excessive phase imbalance constitutes abuse
which will invalidate the Carrier warranty. If the phase
imbalance exceeds 2% for voltage, contact your local
electricity supply company at once and ensure that the chiller
is not switched on until corrective measures have been taken.
Voltage phase imbalance (%) :
= 100 x max.deviation from average voltage deviation
Average voltage
Electrical checks
WARNING: Never switch off the power supply to the crankcase
heaters unless the chiller is out of service for a seasonal
shutdown or lengthy repair. The heaters must be re-energised
for at least 24 hours before the chiller is restarted.
a.
Switch the unit off.
b.
Open the control circuit disconnect switch.
c.
Check the transformer connections.
d.
Ensure that the control circuit corresponds to the wiring
diagram for the unit.
e.
Check that all electrical connections are secure at the
terminals, contactors, bus bars and compressor terminal
blocks.
Start-up
Preliminary checks
Never be tempted to start the chiller without reading fully, and
understanding, the operating instructions and without having
carried out the following pre-start checks:
Confirm that all crankcase heaters are firmly in place, and
check the secure positioning of all control sensors.
Confirm that all crankcase heaters are working by feeling all
compressor crankcases. Every compressor has a 180 W
cartridge heater (see the wiring diagram). The heater remains
energised even when the chiller is shut down to stop the
lubricating oil from absorbing refrigerant.
Check the operation of all accessories - chilled water
circulating pumps, air handlers and other equipment connected
to the evaporator. Follow the individual manufacturer's
instructions for this equipment.
It is recommended to connect the auxiliary contact of the water
pump contactor to ensure maximum unit safety (see wiring
diagram delivered with the unit).
Fill the chilled water circuit with clean water, and an inhibitor
formulated specifically for this purpose, or fill it with another
non-corrosive fluid to be chilled.
Purge air at all high points in the system. If water temperatures
below 5°C for R-407C and 4°C for R-22 are likely, add the
appropriate volume of ethylene glycol to prevent freezing.
Confirm that the suction and discharge line stop valves are
fully opened.
Open the refrigerant line valves. Check again that the water
circuit valves are open.
Check that oil is visible in each compressor sight glass to
between 1/8 and 3/8 of the total glass depth (check for all
compressors).
Confirm that there are no refrigerant leaks.
Confirm that discharge muffler securing bands and discharge
line connections are tight.
Check that all electrical connections are secure.
Actual start-up
IMPORTANT:
•
Commissioning and start-up of the chiller must be
supervised by a qualified refrigeration engineer.
•
Start-up and operating tests must be carried out with a
thermal load applied and water circulating in the
evaporator.
•
All set point adjustments and control tests must be carried
out before the unit is started up.
•
Please refer to the controls manual for the unit.
1.
Ensure that the crankcase heaters have been energized for
24 hours before starting up the unit for the first time.
2.
Start up the unit.
3.
Check that all safety devices are satisfied, paticularly the
high pressure switches.
For this purpose:
-
Stop the condenser fans.
-
Operate the machine until the high pressure switch
trips and verify that the pressure does not exceed the
cut-out value of 2900 kPa.
-
Using the control point as a reference, verify the
correct operation of the unit.