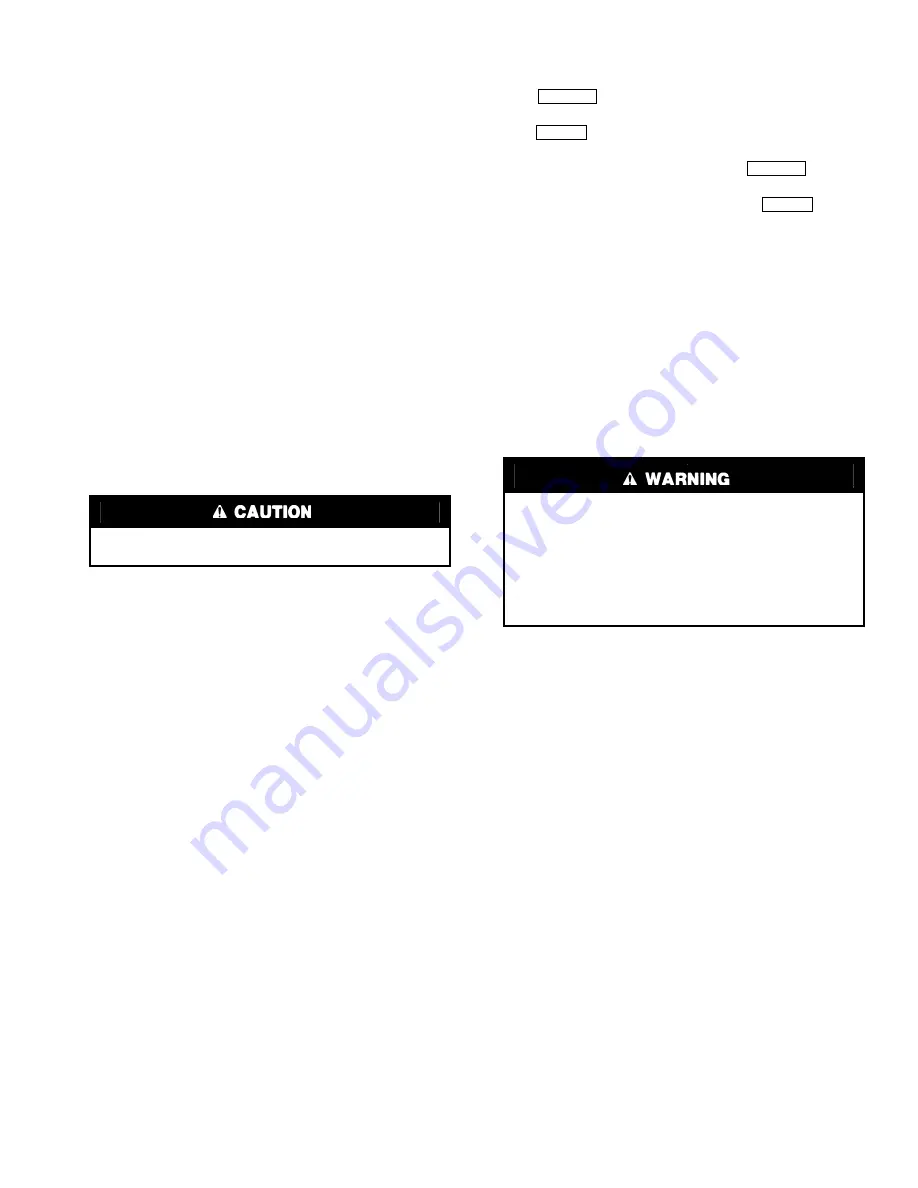
89
Chiller Control Module (CCM) (Fig. 43)
INPUTS — Each input channel has 2 or 3 terminals. Refer to
individual chiller wiring diagrams for the correct terminal
numbers for your application.
OUTPUTS — Output is 24 vac. There are 2 terminals per out-
put. Refer to the chiller wiring diagram for your specific appli-
cation for the correct terminal numbers.
Integrated Starter Module (ISM) (Fig. 44)
INPUTS — Inputs on strips J3-5 and J3 are analog and dis-
crete (on/off) inputs. The specific application of the chiller de-
termines which terminals are used. Refer to the individual
chiller wiring diagram for the correct terminal numbers for
your application.
OUTPUTS — Outputs are 24 vac and wired to strip J9. There
are 2 terminals per output.
Replacing Defective Processor Modules —
The module replacement part number is printed on a small
label on the rear of the CVC module. The chiller model and
serial numbers are printed on the chiller nameplate located on
an exterior corner post. The proper software is factory-installed
by Carrier in the replacement module. When ordering a
replacement chiller visual controller (CVC) module, specify
the complete replacement part number, full chiller model num-
ber, and chiller serial number. The installer must configure the
new module to the original chiller data. Follow the procedures
described in the Software Configuration section on page 60.
INSTALLATION
1. Verify the existing CVC module is defective by using
the procedure described in the Troubleshooting Guide
section, page 76, and the Control Modules section,
page 88. Do not select the ATTACH TO NETWORK
DEVICE table if the CVC indicates a communication
failure.
2. Data regarding the CVC configuration should have
been recorded and saved. This data must be reconfig-
ured into the new CVC. If this data is not available,
follow the procedures described in the Software Con-
figuration section.
If a CCN Building Supervisor or Service Tool is avail-
able, the module configuration should have already
been uploaded into memory. When the new module is
installed, the configuration can be downloaded from
the computer.
Any communication wires from other chillers or CCN
modules should be disconnected to prevent the new
CVC module from uploading incorrect run hours into
memory.
3. To install this module, record values for the TOTAL
COMPRESSOR STARTS and the COMPRESSOR
ONTIME from the MAINSTAT screen on the CVC.
4. Power off the controls.
5. Remove the old CVC.
6. Install the new CVC module. Turn the control power
back on.
7. The CVC now automatically attaches to the local net-
work device.
8. Access the MAINSTAT table and highlight the TOTAL
COMPRESSOR STARTS parameter. Press the
softkey. Increase or decrease the value to
match the starts value recorded in Step 3. Press the
softkey when you reach the correct value.
Now, move the highlight bar to the COMPRESSOR
ONTIME parameter. Press the
softkey.
Increase or decrease the run hours value to match the
value recorded in Step 2. Press the
softkey
when the correct value is reached.
9. Complete the CVC installation. Following the instruc-
tions in the Input Service Configurations section,
page 60, input all the proper configurations such as the
time, date, etc. Check the pressure transducer calibra-
tions. PSIO installation is now complete.
Solid-State Starters —
Troubleshooting information
pertaining to the Benshaw, Inc., solid-state starter may be
found in the following paragraphs and in the Carrier
REDISTART MICRO Instruction Manual supplied by the
starter vendor.
Attempt to solve the problem by using the following prelim-
inary checks before consulting the troubleshooting tables found
in the Benshaw manual.
With power off:
•
Inspect for physical damage and signs of arcing, over-
heating, etc.
•
Verify the wiring to the starter is correct.
•
Verify all connections in the starter are tight.
•
Check the control transformer fuses.
TESTING SILICON CONTROL RECTIFIERS IN THE-
BENSHAW, INC., SOLID-STATE STARTERS — If an
SCR is suspected of being defective, use the following proce-
dure as part of a general troubleshooting guide.
1. Verify power is applied.
2. Verify the state of each SCR light-emitting diode
(LED) on the micropower card.
NOTE: All LEDs should be lit. If any red or green side
of these LEDs is not lit, the line voltage is not present
or one or more SCRs has failed.
3. Check incoming power. If voltage is not present check
the incoming line. If voltage is present, proceed to
Steps 4 through 11.
NOTE: If after completing Steps 4 - 11 all measure-
ments are within specified limits, the SCRs are func-
tioning normally. If after completing Steps 4 - 11
resistance measurements are outside the specified
limits, the motor leads on the starter power lugs T1
through T6 should be removed and the steps repeated.
This will identify if abnormal resistance measurements
are being influenced by the motor windings.
4. Remove power from the starter unit.
Electrical shock can cause personal injury. Disconnect all
electrical power before servicing.
1. Motor terminals or starter output lugs or wire should not
be touched without disconnecting the incoming power
supply. The silicon control rectifiers (SCRs) although
technically turned off still have AC mains potential on
the output of the starter.
2. Power is present on all yellow wiring throughout the
system even though the main circuit breaker in the unit
is off.
SELECT
ENTER
SELECT
ENTER