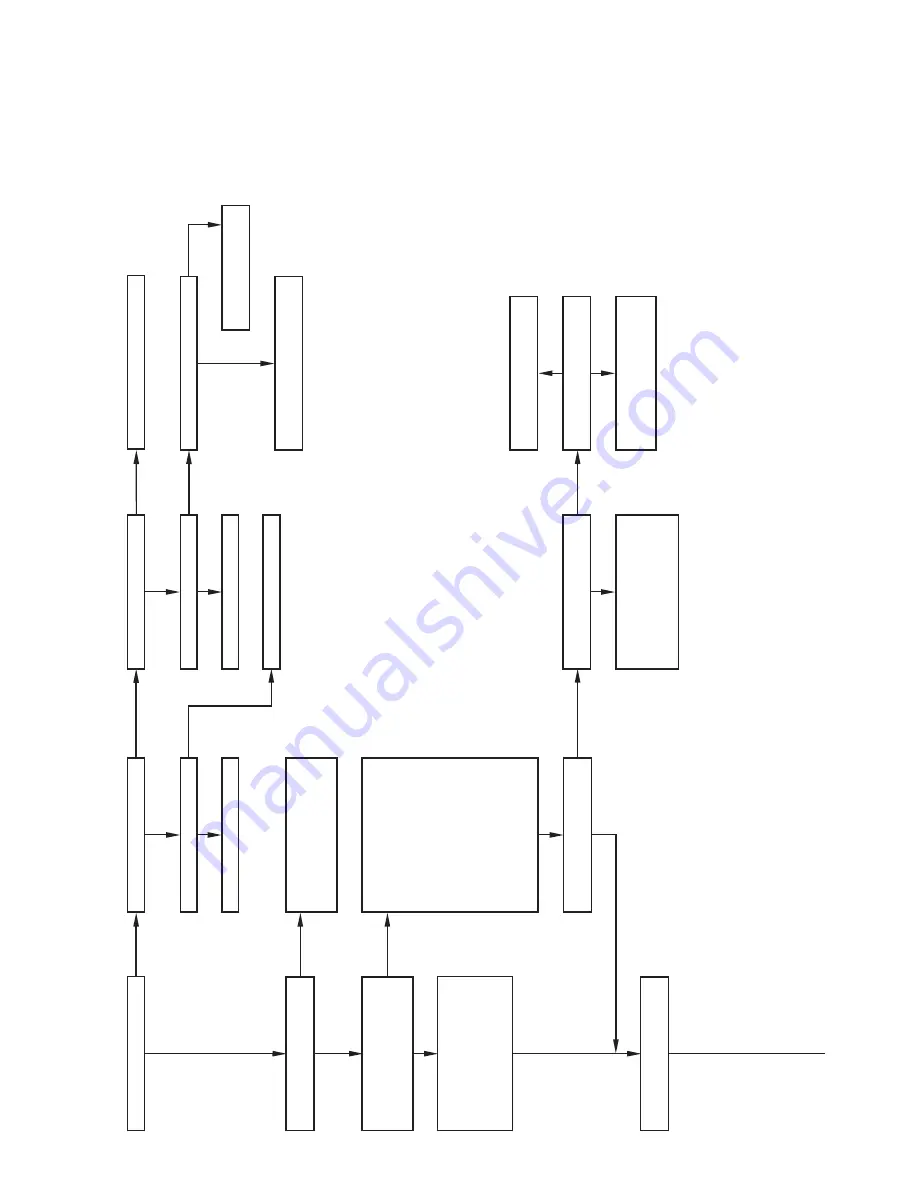
Is circuit breaker closed?
Close door switch and go to start.
Is red LED status light on?
Is door switch closed?
Is red LED status light blinking
rapidly without a pause?
Is there 1
15v going to switch?
Replace door switch.
Replace control center
.
Replace transformer
.
Is red LED status light blinking
ON/OFF slowly with a
combination of short and long
flashes?
Check for correct line voltage
polarity
. If units are twinned,
check for proper low-voltage
(24v) transformer phasing.
Check for previous fault by
momentarily shorting the
TEST
terminal and the C terminal until
the LED goes out. LED will flash
the status code of any previous
fault or the code No. 1
1
(1 short
and 1 long flash) if no previous
fault.
After the control repeats the
code 3 times, the control will go
through a brief component test
sequence.
The inducer will start
and run for the entire component
test.
The HSI, blower motor heat
speed, and blower motor cool
speed will run for 10-15 sec each.
Determine status code.
The
status code is a 2 digit number
with the first digit determined by
the number of short flashes and
the second digit by the number of
long flashes.
W
as there a previous fault code
other than No. 1
1
?
Does control respond to W
,
Y
,
or G 24-vac thermostat signals?
Run system through a heating or
cooling cycle to check operation.
Status codes are erased after 48
hrs or whenever power (1
15v
or 24v) is interrupted.
Go to section with status code
determined.
Is there 1
15v at L1 and L2?
Close circuit breaker and
go back to start.
Check for continuity in wire from circuit
breaker to furnace.
NO
NO
NO
NO
NO
NO
YES
YES
YES
YES
YES
YES
YES
NO
NO
YES
YES
YES
ST
AR
T
Is there 24v at SEC-1 and SEC-2?
NO
Is 24 vac present at W
,
Y
, or G
terminals on the control?
Replace control if it does not
respond to 24-vac signal at W
,
Y
,
or G screw terminals.
Check room thermostat or
interconnecting cable.
YES
NO
NO
12