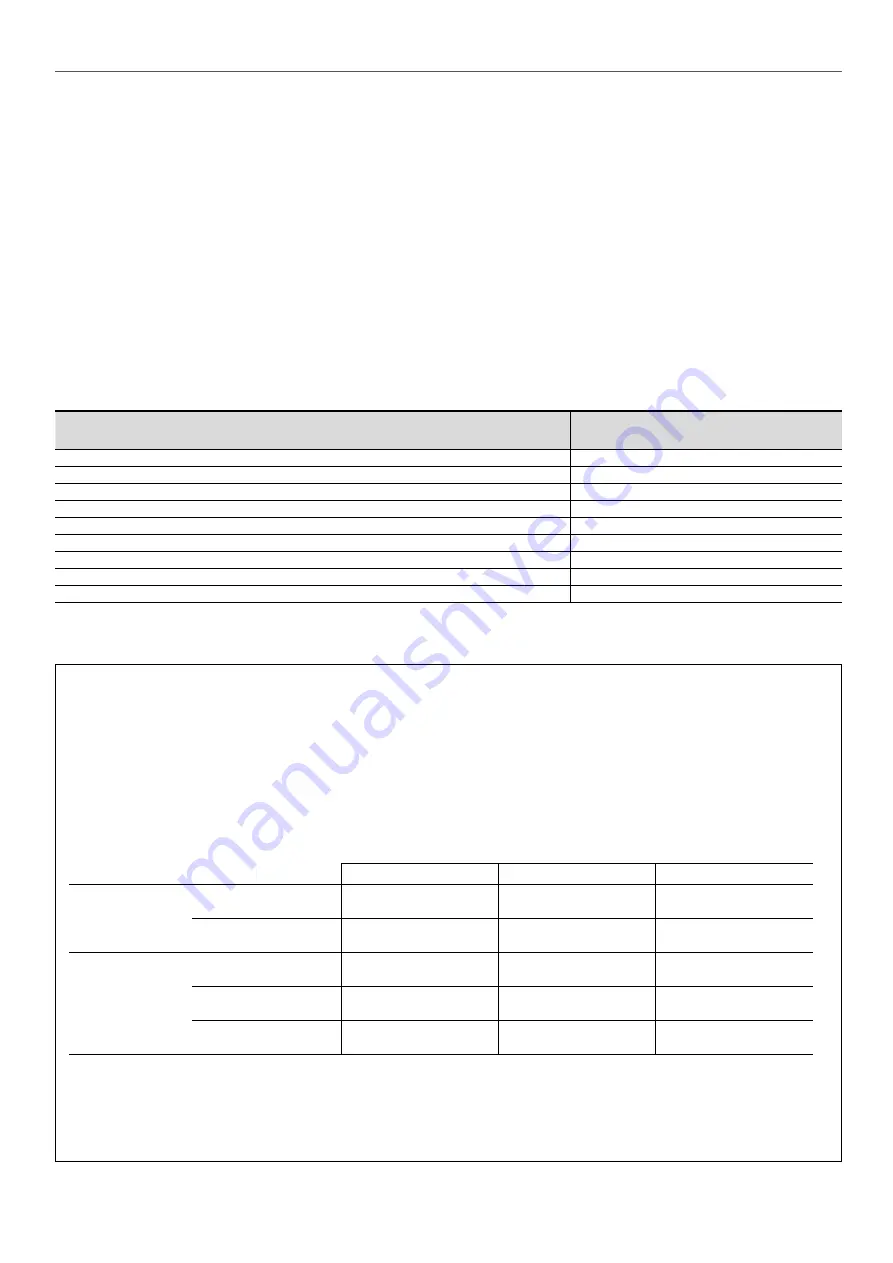
14 - MAINTENANCE
14.1 - Recommendations for maintenance
■
Make sure power to the unit has been disconnected before servicing.
■
Reduce the temperature and pressure before carrying out any work on the bundle.
■ For drycoolers with an expansion vessel, lower the temperature before opening the filler cap (valve cap).
■ Do not make any modifications without our agreement.
■
Do not walk directly on the unit.
■ Depending on the type of fluid (e.g. water without anti-freeze), take precautions to prevent the risk of freezing, which would destroy
the coil. As standard units cannot be completely drained by gravity, protect from freezing as follows:
1. Drain the circuit using the bleed nozzles and the vent located on the manifolds or pipes.
2. Circulate compressed air through the circuit until all water has been removed.
3. Fill the circuit with anti-freeze and close the circuit.
■
For regulated units, do not forget the mandatory inspections.
■
In winter, do not allow snow to accumulate around and on top of the unit.
■
Periodically check the condition of the coatings and apply touch-ups as needed.
14.2 - Maintenance frequency
ACTION
FREQUENCY
Retighten nuts and bolts on fan motor assemblies (grille, motor).
6 months
Check and retighten the packing boxes and mounting bolts on the terminal boxes, if necessary.
6 months
Clean the coil.
1 year (1)
Retighten the electrical connections.
1 month after system start-up then 1 year
Retighten all visible nuts and bolts.
1 year
Check for corrosion to the panelling and that the safety labels and name plate label are present.
1 year (1)
Clean the louvres on the electrical cabinet (optional)
1 year
Expansion vessel (optional): check that all devices work correctly and check the sealing of all couplings.
1 year
Check the electrical cables.
5 years
(1) Frequency to be adapted to the environmental conditions.
14.3 - Information relating to condensers
The sealing test must be carried out in compliance with EC regulation no. 517/2014 relating to certain greenhouse gases.
R410A, R134a and R407C are refrigerant gases with the following environmental impact:
1/ No impact on the ozone layer.
They have an ODP (Ozone Depletion Potential) index of 0
2/ Impact on the greenhouse effect: Global Warming Potential (GWP) of each gas.
- R410A -------- GWP = 2088
- R407C -------- GWP = 1800
- R134a --------
GWP = 1430
-
Users must ensure that periodic leak testing is carried out by qualified personnel based on the number of tonnes of CO
2
equivalent:
≥ 5 tCO2eq
≥ 50 tCO2eq
≥ 500 tCO2eq
Frequency of check
Without leak detection system
Every 12 months
Every 6 months
Every 3 months
With leak detection system
Every 24 months
Every 12 months
Every 6 months
Refrigerant
charge*
R410A (GWP = 2088)
≥ 2.39 kg
≥ 23.9 kg
≥ 239 kg
R407C (GWP = 1800)
≥ 2.77 kg
≥ 27.7 kg
≥ 277 kg
R134a (GWP = 1430)
≥ 3.49 kg
≥ 34.9 kg
≥ 349 kg
* The refrigerant charge and the number of tonnes of CO
2
equivalent will be given by the installer.
-
Users of any system subject to leak testing are required to keep a log of the quantities and types of fluids used, (added or
recovered), and to include the dates and results of leak tests, as well as the name of the technician and the technician's company.
-
A leak test must be carried out one month after any leak repairs.
-
System users are responsible for collecting used refrigerant and having it recycled, regenerated or destroyed.
13
Summary of Contents for 09PE
Page 27: ......