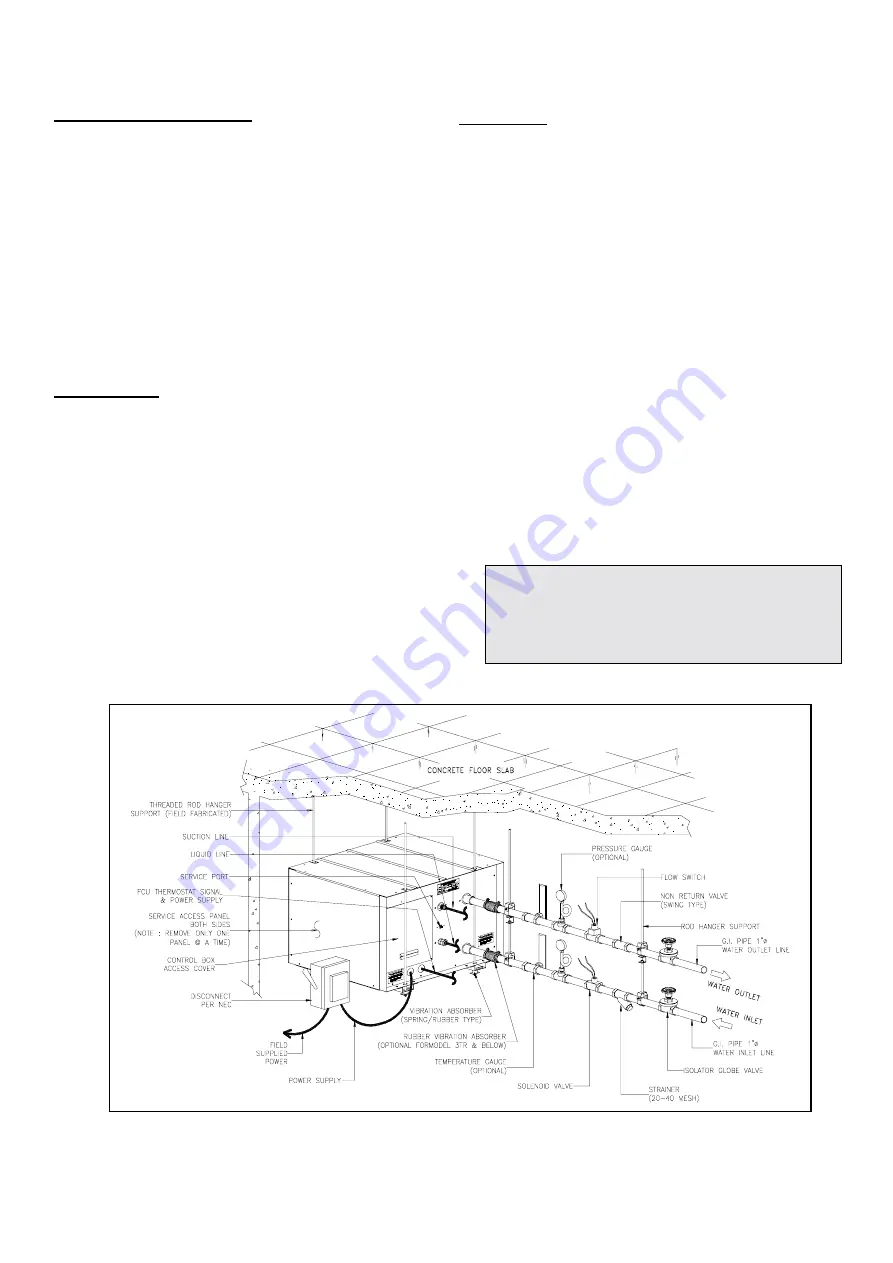
4
EVACUATION AND DEHYDRATION
Evacuation is the most important part of the entire service procedure.
The life and efficiency of the equipment is dependent upon the
evacuation and dehydration thoroughness exercised by the
serviceman.
Air in the system causes high condensing temperature and pressure,
resulting in increased power consumption and at the same time it
reduces system efficiency. Moisture chemically reacts with the
refrigerant and oil thus forming corrosive acids which attacks motor
windings and metal parts, causing early breakdown.
After the system has been leak checked and proven leak free, connect
the vacuum pump and evacuate system to 29” Hg vacuum. It is
advisable to connect both vacuum pump hose to the high-side and low-
side of the system to have a better and faster evacuation.
FINAL LEAK TEST
After the unit has been properly evacuated and charged, use a halogen
leak detector to check system for leaks. In the absence of this device
water-soap solution is acceptable. All piping within the condensing unit,
evaporator, and interconnecting tubing should be checked for leaks. If a
leak is detected, the refrigerant should be recovered before repairing the
leak. This is in compliance with the Clean Air Act.
WATER PIPING
•
Water inlet and outlet are equipped with 25.4mm or 1 “ (FPT)
female pipe thread.
•
Make sure that internal water piping is clean.
•
Use correct size wrenches and proper sealing for water inlet
and outlet connections.
•
Do not over tighten the connections.
•
Suspend or use vibration isolators on water pipes, for pipes
not to transmit vibration.
•
Field install air bleed valve and dirt leg pipes (for backwashing
purposes) in water piping system.
•
Field install water supply and return line connection and check
for water pressure drop and flow rates.
•
Water piping accessories, water strainer (screen assemblies
of 20 to 40 mesh) and water flow switch to be field supplied
and installed.
•
Water system needs to be chemically treated in order to
maintain water cleanliness and minimize scale build-up.
•
After all the water piping is completed, be sure to flush all pipe
work prior to start-up.
Condenser water inlet need to be controlled at 29.5
°C
(85
°F
)
.
It is advisable to always maintain the water inlet temperature in
this region. This can be accomplished by using a thermostat to
control the cooling tower fan and water temperature in the
basin of the tower.
FIG. 5 TYPICAL PIPING & WIRING WORKS
Summary of Contents for 07KHP
Page 5: ...5 FIG 6 CEILING MOUNTED INSTALLATION FIG 7 FLOOR MOUNTED INSTALLATION ...
Page 8: ......
Page 10: ...10 FIG 8 WIRING DIAGRAM 07KHP012 FIG 9 WIRING DIAGRAM 07KHP018 024 ...
Page 11: ...11 FIG 10 WIRING DIAGRAM 07KHP040 050 FIG 11 WIRING DIAGRAM 07KHP060 ...
Page 12: ...12 FIG 12 WIRING DIAGRAM 07KHP090 FIG 13 RECOMMENDED SERVICE CLEARANCES ...