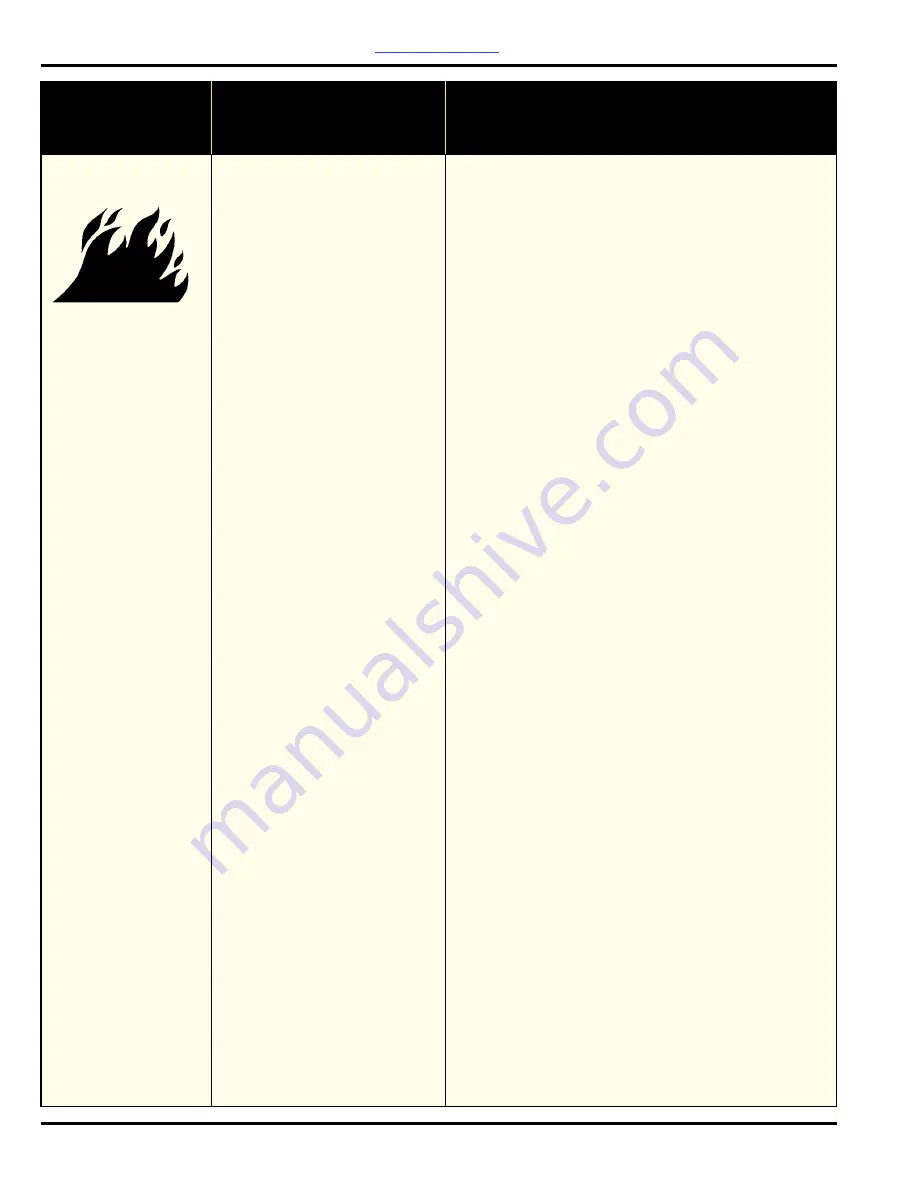
SAFETY
EN
SI-21-06-R1 (11/2021)
4 / 32
www.carlisleft.com
AREA
Tells where hazards
may occur.
HAZARD
Tells what the hazard is.
SAFEGUARDS
Tells how to avoid the hazard.
Spray Area
Fire Hazard
Improper or inadequate
operation and maintenance
procedures will cause a fire
hazard.
Protection against inadvertent
arcing that is capable of
causing fire or explosion is lost
if any safety interlocks are
disabled during operation.
Frequent Power Supply or
Controller shutdown indicates
a problem in the system
requiring correction.
Fire extinguishing equipment must be present in the
spray area and tested periodically.
Spray areas must be kept clean to prevent the
accumulation of combustible residues.
Smoking must never be allowed in the spray area.
The high voltage supplied to the atomizer must be
turned off prior to cleaning, flushing or maintenance.
Spray booth ventilation must be kept at the rates
required by NFPA-33, EN 16985, country, and local
codes. In addition, ventilation must be maintained
during cleaning operations using flammable or
combustible solvents.
Electrostatic arcing must be prevented. Safe
sparking distance must be maintained between the
parts being coated and the applicator. A distance of
1 inch for every 10KV of output voltage is required
at all times.
Test only in areas free of combustible material.
Testing may require high voltage to be on, but only
as instructed.
Non-factory replacement parts or unauthorized
equipment modifications may cause fire or injury.
If used, the key switch bypass is intended for use
only during setup operations. Production should
never be done with safety interlocks disabled.
The paint process and equipment should be set up
and operated in accordance with NFPA-33, NEC,
OSHA, local, country, and European Health and
Safety Norms.