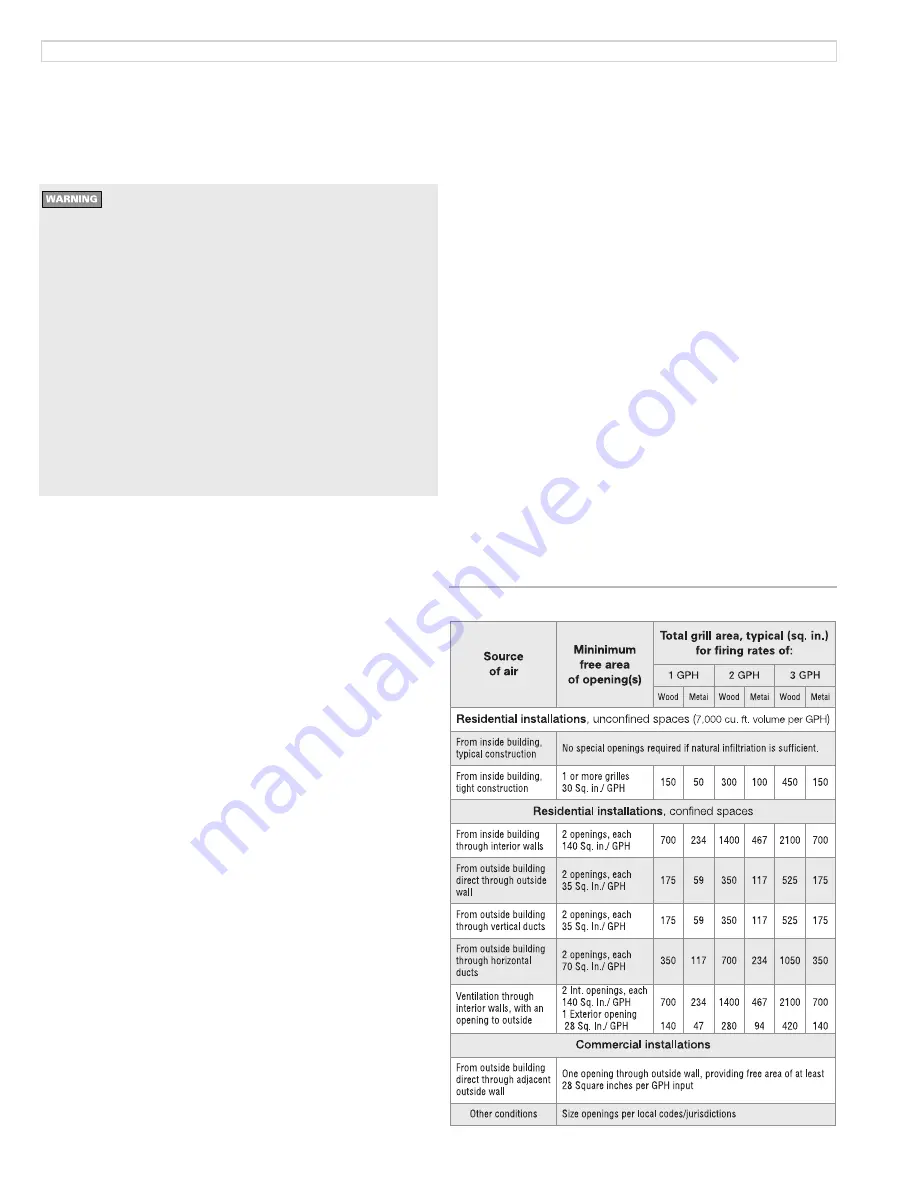
2. Prepare Site • Assemble Burner • Mount Burner
Inspect/repair/replace vent system
Do not install this burner unless you have verified the entire
vent system and the appliance are in good condition and
comply with all applicable codes. And ...
• The vent and chimney must be sized and constructed in
accordance with all applicable codes.
• Do not install or use an existing manual damper in the
breeching (vent connector) or chimney.
• Do not connect the appliance vent connector to a chimney
or vent serving a fireplace, incinerator or solid-fuel-burning
apparatus.
• In a cold climate, do not vent into a masonry chimney that
has one or more sides exposed to the outside. Install a listed
stainless steel liner to vent the flue products.
• A defective vent system could result in severe personal
injury, death or substantial property damage.
Prepare vent/chimney
• Secure all metal vent joints with screws, following the vent manufacturer’s
instructions. Seal all joints in the vent system and chimney. Repair masonry
chimney lining and repair all mortar joints as needed.
• Install a barometric draft regulator in the vent piping if specified in the
appliance manual. (The damper must be located in the same space as the
appliance.)
• Provide support for the vent piping. Do not rest the weight of any of the
vent piping on the appliance flue outlet.
Table 1
Minimum combustion/ventilation air openings
Combustion/ventilation air openings
Check appliance manual and applicable codes for required sizing/design/
placement of combustion/ventilation air openings. You can use the follow-
ing general guidelines, taken from NFPA 31, provided they meet all local
requirements.
Louvers/screens
• Air opening sizes are always given in free area. This means after deduction
for louver obstruction. If you can’t find the louver reduction for the grilles
used, assume free area is 20% of total for wood louvers, or 60% of total
for metal louvers.
• Screens can be no finer than ¼-inch mesh, and must be accessible for
cleaning.
Residential installations
Unconfined spaces (at least 7,000 cubic feet per GPH)
• An unconfined space means a room with at least 7,000 cubic feet volume
for each GPH input (or 50 cubic feet per MBH) of all appliances in the room.
Example: For each 1 GPH oil input, the room must have 7,000 cubic feet
(875 square feet with an 8-foot ceiling height.)
• Open basements and crawl spaces are usually large enough, and will
generally allow enough air infiltration so special provisions will seldom be
required.
• If the building is tightly constructed, you will have to provide outside air
openings into the building. The total free area of the openings must be
at least 1 square inch per 5,000 Btuh (28 square inches per GPH) of all
appliances in the space.
•
See Table 1 for summary
.
Confined spaces (less than 7,000 cubic feet per GPH)
• Air taken from inside building only —
• Provide two openings — one near floor, the other near ceiling. Provide free
area of 140 square inches per GPH input. If building is tightly constructed,
provide air opening(s) into building providing 30 square inches per GPH as
well.
• Air taken from outside —
• Direct through outside wall or vertical ducts: Provide two openings — one
near floor, the other near ceiling. Provide free area of 35 square inches per
GPH input.
• Through horizontal ducts: Provide two openings — one near floor, the other
near ceiling. Provide free area of 70 square inches per GPH input.
• Ventilation air from inside/combustion air from outside
• Size openings to interior to provide 140 square inches free area per GPH
input. Size outside air duct to provide 28 square inches free area per
GPH.
• See Table 1 for summary.
MN66-3P 090721
– 4 –
Carlin Select EZ-66 Oil/Bio Fuel Burner Instruction Manual