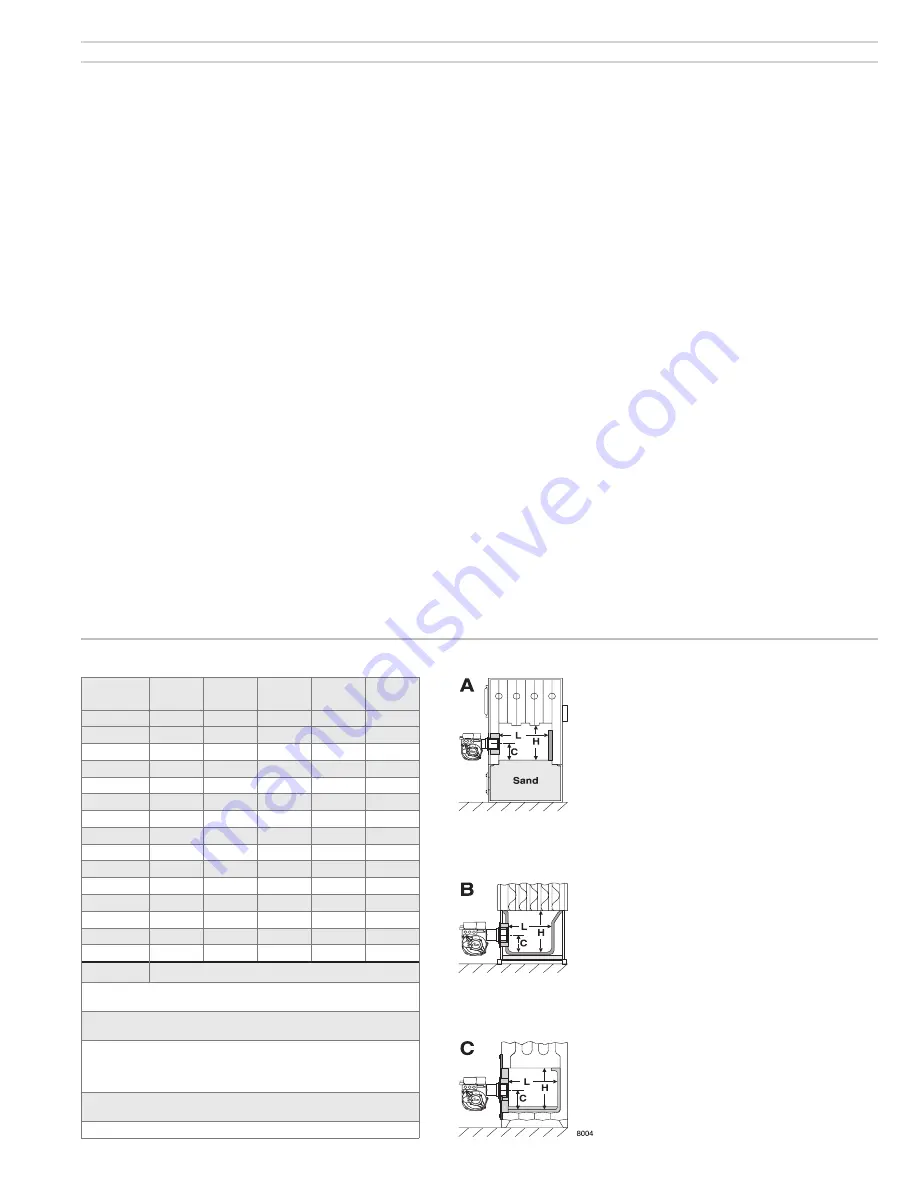
Carlin part number MNEZ123 Rev. 01/12/10
– 7 –
Model EZ-1/2/3 oil burners — Instruction manual
2. Prepare site • assemble burner • mount burner
(continued)
Verify combustion chamber
General guidelines
If retrofitting the burner to an appliance, install the burner in accordance
•
with the appliance instruction manual, when available. If no specific
application data is available from the appliance manufacturer, apply
the guidelines in Table 3 to check whether the burner is likely to work
acceptably in the application.
Clean all appliance flues and heating surfaces thoroughly, removing
•
all soot and scale.
Seal all joints and gaps using furnace cement to prevent excess air infiltration.
Minimum combustion chamber dimensions
Illustrations A to C in Table 3 show different chamber configurations.
•
Burner retrofit applications — guidelines and minimum dimensions for combustion chambers
Table 3
Verify clearances
Verify that the burner/appliance will maintain all clearances from combustible
construction and clearances for service/maintenance as required in the appliance
manual and applicable codes.
Verify that the vent system components maintain all necessary clearances to
combustible construction, including the correct design of thimbles and insulation
where penetrating combustible walls.
Do not attempt to fire the burner in a chamber with dimensions smaller
•
than shown in Table 3 unless the application has been specifically tested
and listed by the appliance manufacturer and/or Carlin.
Please notice the special requirements given in Table 3 notes.
•
Using chamber linings and lightweight chambers
When using refractory liners or lightweight chambers, use insulating-
•
type refractory rated 2300°F minimum.
You must install a target wall liner if flame length is close to the length
•
of the chamber.
Use a floor liner when possible. The floor liner will improve firing in most
•
applications. Extend floor liner 3 to 4 inches up side wall.
Target wall liners — Corbel the top of target wall liners 1½ to 2½ inches
•
deep and extend at least 3 to 4 inches above the center of the flame.
Use pre-formed chamber liners when available.
•
For firing rates below 0.75 GPH, it is best to apply in a refractory-lined
•
or stainless tube (designed for application) chamber. Lining the floor
and target wall of the chamber with lightweight insulating refractory
will accomplish the same.
When conversion firing coal-fired units, install a combustion chamber in
•
the ashpit area, or fill ashpit with sand up to 2 inches above the “mud
ring” of a boiler (firing through the door). Install a lightweight refractory
liner on the target wall as in Table 3, Figure C. Make sure the minimum
dimensions comply with those listed.
A. Conversion firing coal-fired units
Install a combustion chamber in the ashpit area, or fill
1.
ashpit with sand up to 2 inches above the “mud ring”
of a boiler (firing through door).
When firing through door, install a lightweight refractory
2.
“target” on the rear wall, as shown.
B. Conversion firing dry-base units
Applies to brick, refractory, precast and preformed
1.
refractory fiber chambers. Lightweight, insulating-type
materials are preferred because of their quick warm-up.
Use material rated at least 2300°F.
Dimensions in the table can be exceeded without much
2.
effect for dry-base units.
C. Conversion firing wet-based units
Apply recommendations here to prevent flame from im-
1.
pinging on surfaces or being cooled too much by the cool
walls of the heat exchanger. Do not exceed dimensions
of table more than 50% to avoid flame chilling.
Install a ceramic fiber floor liner (extended 3 to 4 inches
2.
up the side walls) and a ceramic fiber rear target the
full width of the back wall as well. Corbel the top of
the target 1½” to 2½” deep and extend at least 3 to 4
inches above the center of the flame. Use preformed
chambers and/or target walls if available.
Set the fuel unit pressure for approximately 150 PSIG
3.
and use a nozzle rated about 20% less than the firing
rate to compensate for the higher pressure. This will
improve atomization, making the flame more intense,
shorter and hotter. Use a head bar matched for the
nozzle size, but set the air band to match the firing
rate.
1
Firing rate
2
L
3
W
4
C
5
H
6
DV
GPH
Inches
Inches (3)
Inches
Inches
Inches (5)
0.50
7
6
3
8
7
0.65
7.5
7
3.5
9
7.5
0.75
8
7
3.5
9
8
0.85
9
7
3.5
9
8.5
1.00
10
8
4
10
9
1.10
11
8
4
10
9.5
1.25
12
8
4
10
10
1.35
13
8
4
10
11
1.50
14
8
4.5
11
12
1.65
15
9
4.5
11
13
1.75
16
9
4.5
11
14
2.00
17
9
4.5
11
15
2.25
18
10
5
12
16
2.50
19
10
5
12
17
Notes
1 Some tested appliances operate well with dimensions other than
above.
2 Generally, the application should be acceptable for dimensions as
large as 50% greater than the above.
3 Horizontal cylinder chambers should have a diameter at least as
large as the dimension in column 3.
Horizontal steel cylinder chambers should have diameters at least
1 to 4 inches larger than the dimension in column 3.
4 Wing walls are not recommended. Corbels can be beneficial to
heat distribution in some appliances.
5
DV
is the minimum diameter for vertical cylinder chambers.
Summary of Contents for EZ-1
Page 16: ...Carlin part number MNEZ123 Rev 01 12 10 15 Model EZ 1 2 3 oil burners Instruction manual...
Page 18: ...Carlin part number MNEZ123 Rev 01 12 10 17 Model EZ 1 2 3 oil burners Instruction manual...
Page 20: ...Carlin part number MNEZ123 Rev 01 12 10 19 Model EZ 1 2 3 oil burners Instruction manual...
Page 22: ...Carlin part number MNEZ123 Rev 01 12 10 21 Model EZ 1 2 3 oil burners Instruction manual...