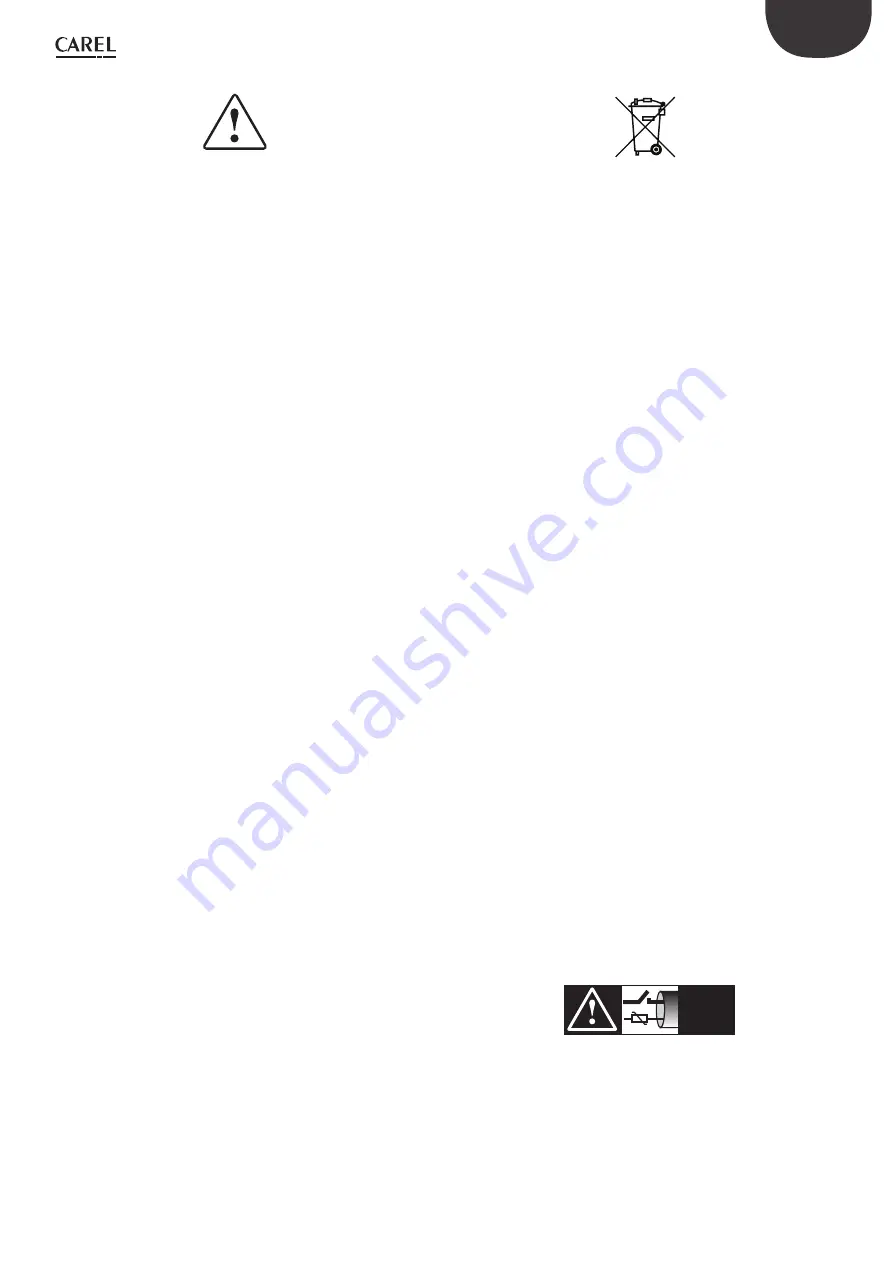
3
ENG
“EVD ice” +0300038EN - rel. 1.1 - 23.04.2018
WARNINGS
CAREL bases the development of its products on decades of experience
in HVAC, on the continuous investments in technological innovations
to products, procedures and strict quality processes with in-circuit and
functional testing on 100% of its products, and on the most innovative
production technology available on the market. CAREL and its subsidiaries
nonetheless cannot guarantee that all the aspects of the product and the
software included with the product respond to the requirements of the final
application, despite the product being developed according to start-of-the-
art techniques. The customer (manufacturer, developer or installer of the final
equipment) accepts all liability and risk relating to the configuration of the
product in order to reach the expected results in relation to the specific final
installation and/or equipment. CAREL may, based on specific agreements, acts
as a consultant for the positive commissioning of the final unit/application,
however in no case does it accept liability for the correct operation of the final
equipment/system.
The CAREL product is a state-of-the-art product, whose operation is specified
in the technical documentation supplied with the product or can be
downloaded, even prior to purchase, from the website www.carel.com.
Each CAREL product, in relation to its advanced level of technology, requires
setup/configuration/programming/commissioning to be able to operate in
the best possible way for the specific application. The failure to complete such
operations, which are required/indicated in the user manual, may cause the
final product to malfunction; CAREL accepts no liability in such cases.
Only qualified personnel may install or carry out technical service on the
product.
The customer must only use the product in the manner described in the
documentation relating to the product.
In addition to observing any further warnings described in this manual, the
following warnings must be heeded for all CAREL products:
•
prevent the electronic circuits from getting wet. Rain, humidity and all
types of liquids or condensate contain corrosive minerals that may damage
the electronic circuits. In any case, the product should be used or stored
in environments that comply with the temperature and humidity limits
specified in the manual;
•
do not install the device in particularly hot environments. Too high
temperatures may reduce the life of electronic devices, damage them and
deform or melt the plastic parts. In any case, the product should be used
or stored in environments that comply with the temperature and humidity
limits specified in the manual;
•
do not attempt to open the device in any way other than described in the
manual;
•
do not drop, hit or shake the device, as the internal circuits and mechanisms
may be irreparably damaged;
•
do not use corrosive chemicals, solvents or aggressive detergents to clean
the device;
•
do not use the product for applications other than those specified in the
technical manual.
All of the above suggestions likewise apply to the controllers, serial boards,
programming keys or any other accessory in the CAREL product portfolio.
CAREL adopts a policy of continual development. Consequently, CAREL
reserves the right to make changes and improvements to any product
described in this document without prior warning.
The technical specifications shown in the manual may be changed without
prior warning.
The liability of CAREL in relation to its products is specified in the CAREL general
contract conditions, available on the website www.carel.com and/or by
specific agreements with customers; specifically, to the extent where allowed
by applicable legislation, in no case will CAREL, its employees or subsidiaries
be liable for any lost earnings or sales, losses of data and information, costs of
replacement goods or services, damage to things or people, downtime or any
direct, indirect, incidental, actual, punitive, exemplary, special or consequential
damage of any kind whatsoever, whether contractual, extra-contractual or
due to negligence, or any other liabilities deriving from the installation, use or
impossibility to use the product, even if CAREL or its subsidiaries are warned
of the possibility of such damage.
DISPOSAL
INFORMATION FOR USERS ON THE CORRECT
HANDLING OF WASTE ELECTRICAL AND ELEC-
TRONIC EQUIPMENT (WEEE)
In reference to European Union directive 2002/96/EC issued on 27 January
2003 and the related national legislation, please note that:
1. WEEE cannot be disposed of as municipal waste and such waste must be
collected and disposed of separately;
2. the public or private waste collection systems defined by local legislation must
be used. In addition, the equipment can be returned to the distributor at
the end of its working life when buying new equipment;
3. the equipment may contain hazardous substances: the improper use or
incorrect disposal of such may have negative effects on human health
and on the environment;
4. the symbol (crossed-out wheeled bin) shown on the product or on the
packaging and on the instruction sheet indicates that the equipment has
been introduced onto the market after 13 August 2005 and that it must
be disposed of separately;
5. in the event of illegal disposal of electrical and electronic waste, the penalties
are specified by local waste disposal legislation.
Warranty on the materials:
2 years (from the date of production, excluding
consumables).
Approval:
the quality and safety of CAREL INDUSTRIES products are
guaranteed by the ISO 9001 certified design and production system, as well
as by the marks (*).
CAUTION: separate as much as possible the probe and digital input signal
cables from the cables carrying inductive loads and power cables to avoid
possible electromagnetic disturbance.
Never run power cables (including the electrical panel wiring) and signal
cables in the same conduits.
NO POWER
& SIGNAL
CABLES
TOGETHER
READ CAREFULLY IN THE TEXT!