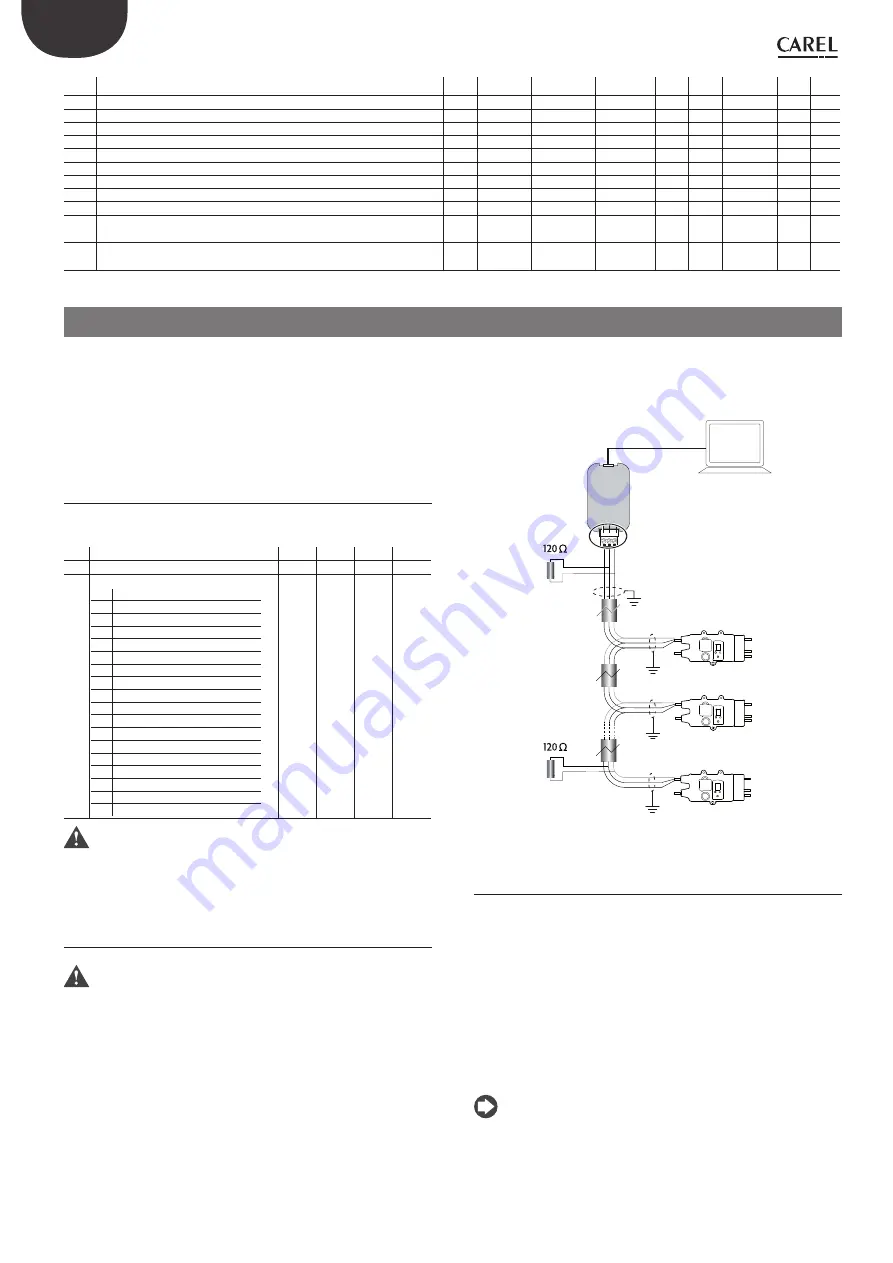
18
ENG
“EVD ice” +0300038EN - rel. 1.1 - 23.04.2018
Par.
Description
Def.
Min.
Max.
UoM
Type Carel Modbus® R/W Note
Si
Unit of measure 1=°C/K/barg ¦ 2=°F/psig
1
1
2
-
I
16
143
R/W
IA
Enable operating mode modification 0/1 = yes/ no
0
0
1
-
I
15
142
R/W
U1
Enable manual valve positioning 0/1 = no/ yes
0
0
1
-
D
11
10
R/W
U2
Manual valve position
0
0
999
step
I
7
134
R/W
U3
Valve control steps: 1/2 = 480/960 steps
1
1
2
-
I
11
138
R/W
U4
Valve opening at start-up (evaporator/valve capacity ratio)
50
0
100
%
I
19
146
R/W
Fr
Firmware release
-
-
-
-
A
9
8
R
di
DI configuration: 1=start/stop regulation; 2=backup regulation
1
1
2
-
I
18
145
R/W
rt
Reserved
1
1
1
-
L1
S1 alarm: Minimum pressure
-1
-85(-121)
S1 alarm:
Max pressure
barg (psig)
A
20
19
R/W
H1
S1 alarm: Maximum pressure
-
S1 alarm:
Min press.
200 (392) barg (psig)
A
21
20
R/W
Tab. 7.a
8. NETWORK CONNECTION
The driver can be connected via a network connection to:
1.
a computer running the VPM software, for setting the parameters
before commissioning;
2.
a pCO controller, loaded with the application program;
3.
a PlantVisor/PlantVisorPRO supervisor, for remote monitoring and
alarm detection.
8.1 RS485 serial configuration
n1 assigns to the controller an address for serial connection to a
supervisory and/or telemaintenance system.
Par. Description
Def.
Min.
Max. UoM
n1 Network address
1
1
99
-
n2 Baud rate (bit/s)
0 4800, 2 stop bit, parity none
1
9600, 2 stop bit, parity none
2
19200, 2 stop bit, parity none
3
4800, 1 stop bit, parity none
4
9600, 1 stop bit, parity none
5
19200, 1 stop bit, parity none
6
4800, 2 stop bit, parity even
7
9600, 2 stop bit, parity even
8
19200, 2 stop bit, parity even
9
4800, 1 stop bit, parity even
10 9600, 1 stop bit, parity even
11 19200, 1 stop bit, parity even
12 4800, 2 stop bit, parity odd
13 9600, 2 stop bit, parity odd
14 19200, 2 stop bit, parity odd
15 4800, 1 stop bit, parity odd
16 9600, 1 stop bit, parity odd
17 19200, 1 stop bit, parity odd
2
0
17
-
Important:
all controllers connected in a serial network need to be
set with the same communication parameters.
8.2 Network connection for commissioning
via PC
Warnings:
•
fasten the converter properly so as to prevent disconnection;
•
complete the wiring without power connected;
•
keep the CVSTDUMOR0 interface cables separate from the power
cables (power supply);
•
in compliance with standards on electromagnetic compatibility, a
shielded cable suitable for RS485 data transmission is used.
The RS485 converter is used to connect a computer running the VPM
software to the EVD ice driver via a serial network, for commissioning the
controllers. The system allows a maximum of 99 units, with a maximum
network length of 500 m. Connection requires the standard accessories
(RS485-USB converter, CAREL P/N CVSTDUMOR0) and a 120 Ω terminating
resistor to be installed on the terminals of the last connected controller.
Connect the RS485 converter to controllers and make the connections
as shown in the figure. To assign the serial address, see parameter n1. See
the converter technical leaflets for further information.
GND
USB-485
Converter
CVSTDUMOR0
USB
T+ T -
shield
shield
shield
shield
*
*
EVD ice 1
EVD ice 2
EVD ice ...n
VPM
Fig. 8.a
8.3 Visual parameter manager
Go to http://ksa.carel.com and follow the instructions below. Select in
sequence:
1.
“Software & Support”
2.
“Configuration & Updating Softwares”
3.
“Parametric Controller Software”
4.
“Visual Parametric Manager”
A window will open with the possibility to download two files:
1.
VPM_setup_X.Y.Z.W_full.zip: complete program;
2.
X.Y.Z.W_VPM_Devices_Upgrade.zip: upgrade for supported devices;
If this is the first installation, select Setup full, otherwise Upgrade. The
program installs automatically by running setup.exe.
Note:
if choosing complete installation (Setup full), uninstall any
previous versions of VPM.