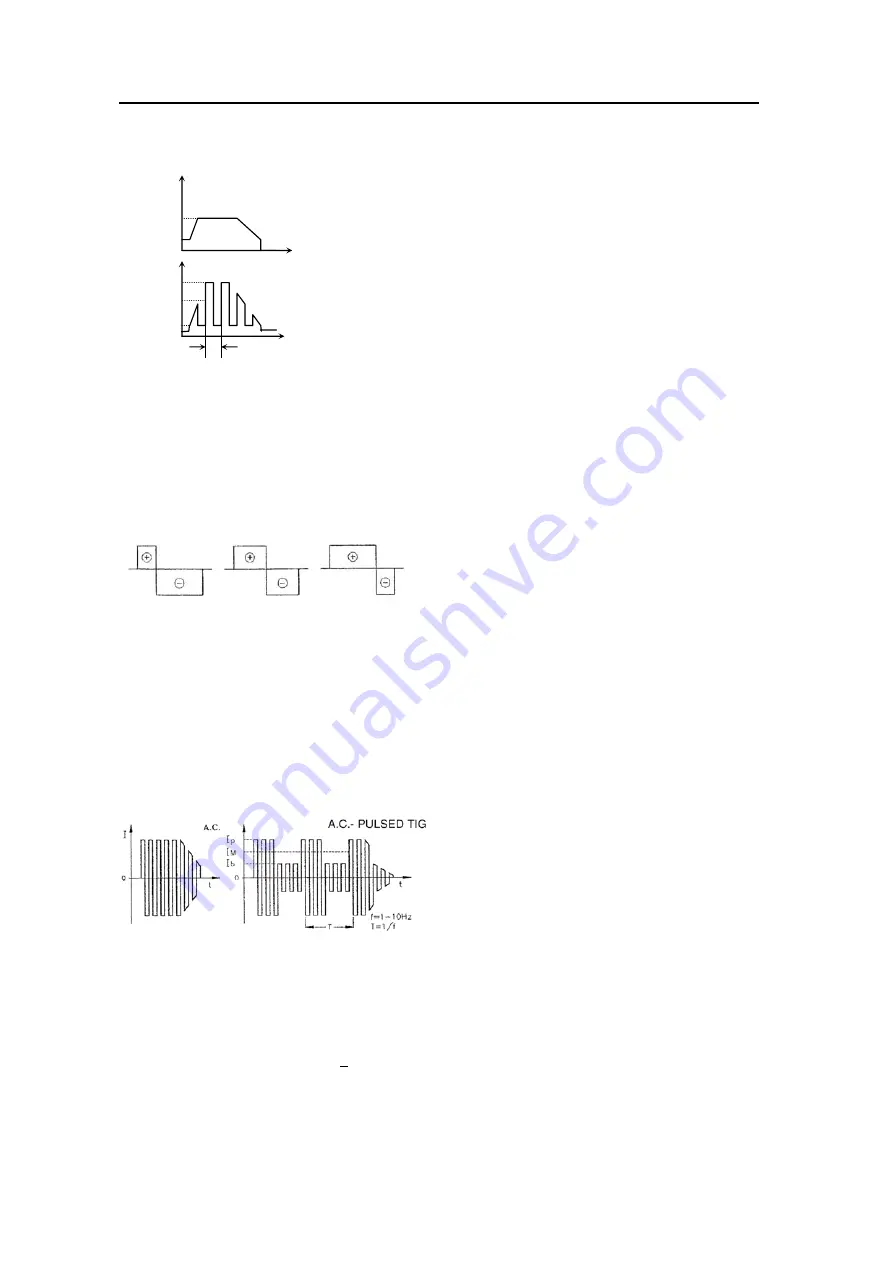
B-8 OPERATION B-8
Increasing the frequency constricts the arc,
increases stability and improves weld quality.
FIGURE B.6
A.C. (Alternating Current)
(see Figure B.7)
Alternating Current welding is typically used for Tig
welding aluminum (and its alloys) or magnesium.
The polarity alternates between Electrode Positive
and Electrode Negative (EN). During the positive
halfwave the oxide is broken. During the negative
halfwave, the electrode cools, the workpiece melts
and penetration occurs.
FIGURE B.7
Greater % EN = MORE PENETRATION 50% (EN) Lesser %
EN = more CLEANING
Changing the wave balance alters the ratio between
the cleaning and the penetrating current.
A.C.-Pulsed TIG
When AC welding, a pulsed current can be used,
with similar effects to those described in pulsed
direct current welding.
FIGURE B.8
STEEL TIG WELDING
The TIG process is very effective for welding both
carbon steel and alloy steel, especially in
applications requiring precision results. DC
Electrode Negative Polarity is required. Since this
process does not include the removal of impurities,
proper cleaning and preparation of the edges is
required.
FILLER MATERIAL:
The filler rods must deposit welds with mechanical
characteristics appropriate for the application.
COPPER TIG WELDING
Since the TIG welding is a process characterized by
high heat concentration, it is particularly suitable for
welding materials with high thermal conductivity,
like copper. As with steel, the DC Electrode
Negative
Polarity is employed, with argon as protective gas.
Considering the fluidity of molten copper, the use of
backup support may prove useful.
FILLER MATERIAL:
In order to avoid the oxidation of the molten material,
filler materials containing phosphorus, silicon or
other deoxidating materials are typically used. The
mechanical properties can also be improved
through the use of silver.
TIPS FOR AC TIG WELDING
AC Inverter TIG power sources offer two significant
advantages over conventional Silicon Controlled
Rectifier (SCR) / transformer power sources:
1. The AC wave balance(SP%) can be set to a
higher percentage electrode negative which
minimizes tungsten heating and erosion.
2. The AC frequency can be varied to "focus" the
arc. Increasing the AC frequency above 60Hz will
narrow the cone shape arc from the tungsten’s tip.
Decreasing the AC frequency below 60Hz will
broaden the cone shape arc from the tungsten’s tip.
The two above benefits can be used to maintain a
tight focus of the arc for precise heat control and
tight joint access. Because of the AC inverters
abilities in these areas the following
recommendations are made as a starting point:
●
A 2% Thoriated tungsten is recommended instead
of the Pure tungsten that is normally recommended
for AC welding. Thoriated tungstens emit electrons
easier and therefore will improve starting.
●
. Sharpen the tungsten to a point. Normally it is
recommended to preball a pure tungsten when AC
welding with a conventional power source.
However, the AC inverter with it
’
s extended AC
balance control minimized tungsten heating thus
allowing for a pointed tungsten to be used.
Greater % EN=more penetration
Lesser % EN=more CLEANING
50 % (EN)
DC TIG-NOT PULSED
DC PULSED TIG
I(A)
Ip
I(A)
Ip
Im
Ia
t
t
T
f = 0.5 ~ 25Hz
T =1/f
Summary of Contents for Digi-Tig320ACDC
Page 27: ...B 13 OPERATION B 13...
Page 28: ...B 14 OPERATION B 14...
Page 29: ...B 15 OPERATION B 15...