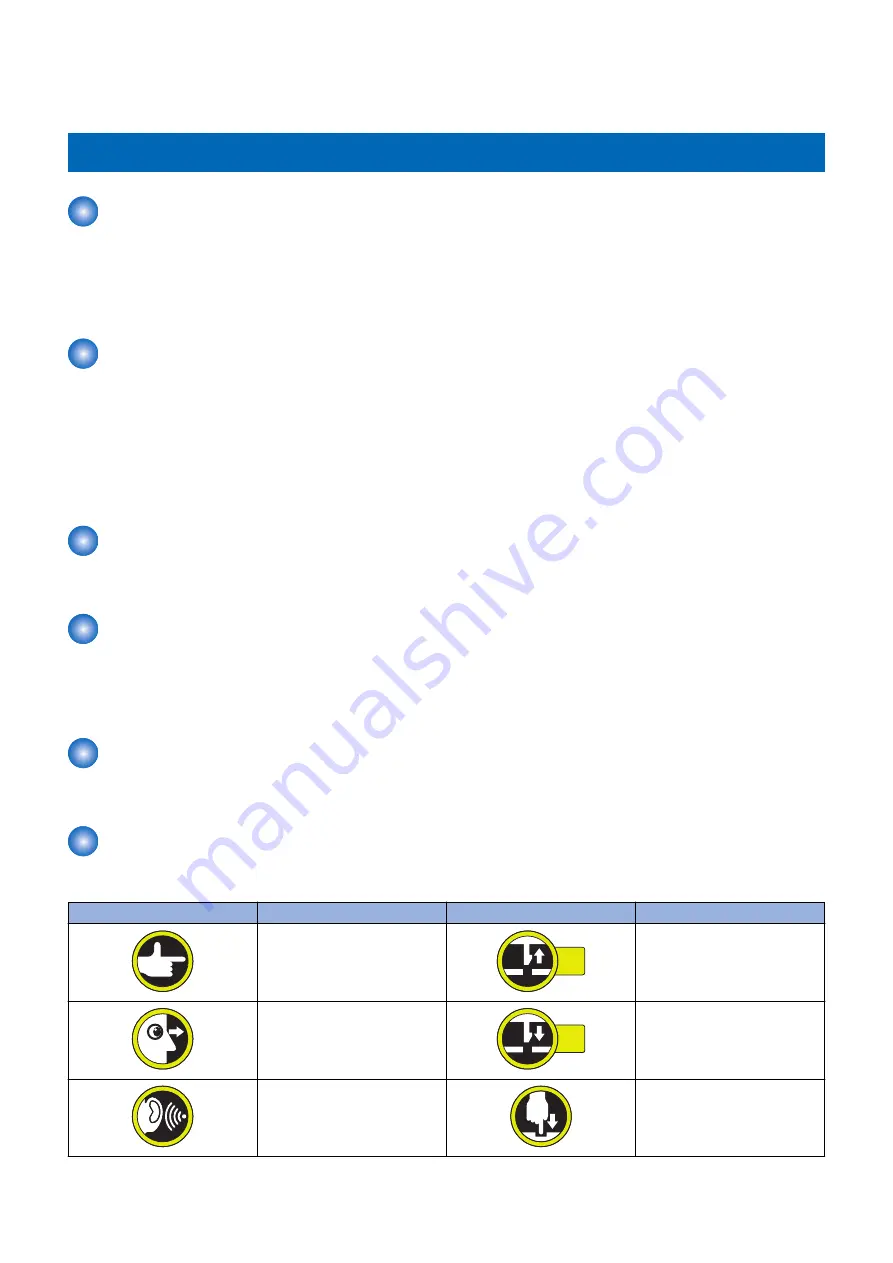
Introduction
Important Notices
Application
This manual has been issued by Canon Inc. for qualified persons to learn technical theory, installation, maintenance, and repair
of products.
This manual covers all localities where the products are sold. For this reason, there may be information in this manual that does
not apply to your locality.
Corrections
This manual may contain technical inaccuracies or typographical errors due to improvements or changes in products.
When changes occur in applicable products or in the contents of this manual, Canon will release technical information as the
need arises. In the event of major changes in the contents of this manual over a long or short period, Canon will issue a new
edition of this manual.
The following paragraph does not apply to any countries where such provisions are inconsistent with local law.
Trademarks
The product names and company names used in this manual are the registered trademarks of the individual companies.
Copyright
This manual is copyrighted with all rights reserved. Under the copyright laws, this manual may not be copied, reproduced or
translated into another language, in whole or in part, without the consent of Canon Inc.
Copyright CANON INC. 2015
Caution
Use of this manual should be strictly supervised to avoid disclosure of confidential information.
Explanation of Symbols
The following symbols are used throughout this Service Manual.
Symbols
Explanation
Symbols
Explanation
Check.
1x
Remove the claw.
Check visually.
1x
Insert the claw.
Check a sound.
Push the part.
Introduction
Summary of Contents for Paper Folding Unit-J1
Page 1: ...Revision 3 0 Paper Folding Unit J1 Service Manual ...
Page 9: ...Product Overview 1 Outline 4 Specifications 5 Names of Parts 9 ...
Page 18: ...Technical Explanation 2 Basic Configuration 13 Controls 25 Upgrading 55 ...
Page 62: ...Periodical Service 3 List of Work for Scheduled Servicing 57 ...
Page 73: ... Procedure 1 Remove the screws 2 Screws 2x 4 Disassembly Assembly 67 ...
Page 95: ...Adjustment 5 Overview 90 Major Adjustment 93 Action on parts replacement 105 ...
Page 155: ...13 Return the jam recovery map and close the front upper cover 6 Installation 149 ...
Page 158: ...APPENDICES Service Tools 153 General Circuit Diagram 154 ...