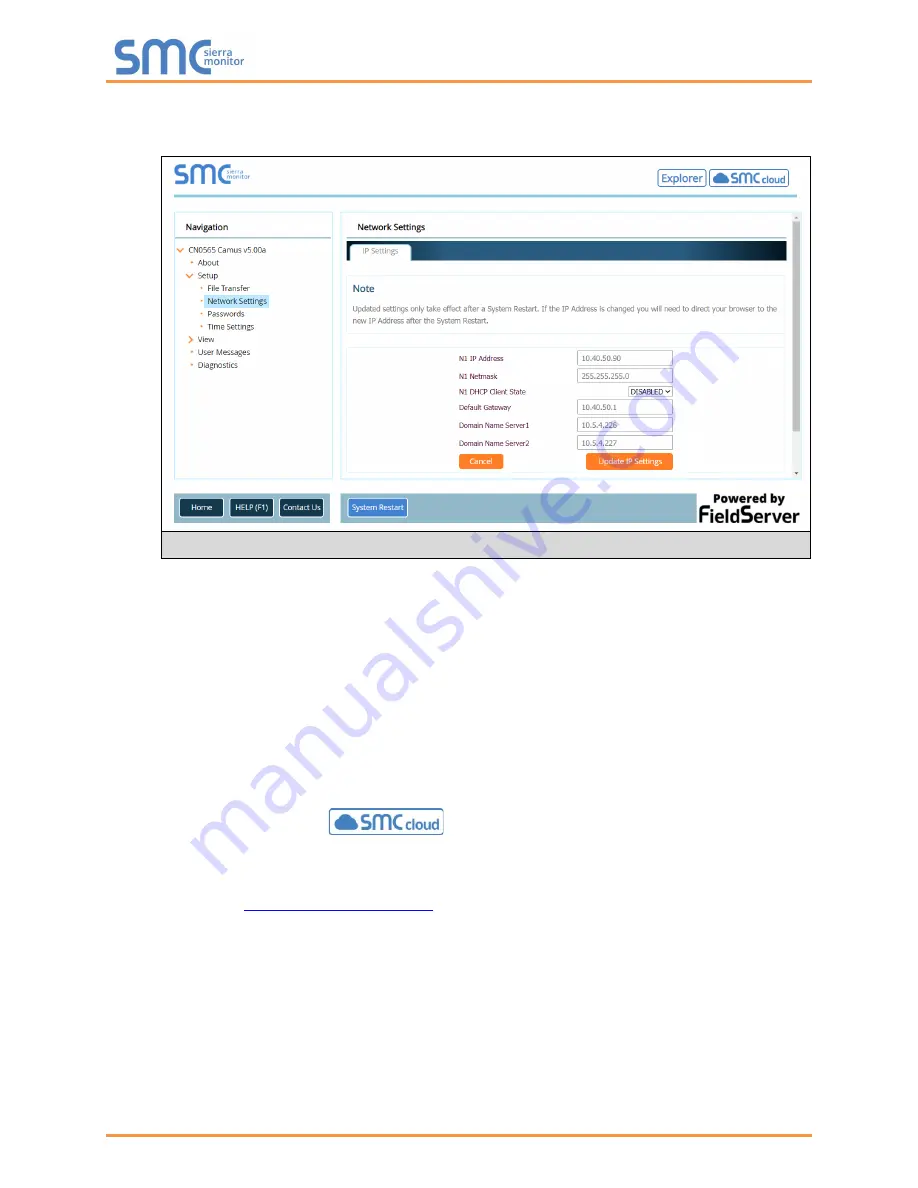
Camus ProtoNode Start-up Guide
Page 35 of 87
•
From the FS-GUI landing page, click on “Setup” to expand the navigation tree and then select
“Network Settings”
to access the IP Settings menu. (
•
Modify the IP Address (N1 IP Address field) of the ProtoNode Ethernet port.
•
If necessary, change the Netmask (N1 Netmask field).
•
If necessary, change the IP Gateway (Default Gateway field).
NOTE: If the ProtoNode is connected to a managed switch/router, the IP Gateway of the
ProtoNode should be set to the IP Address of that managed switch/router.
•
Click the “System Restart” button at the bottom of the page to apply changes and restart the
ProtoNode.
•
Unplug Ethernet cable from PC and connect it to the network switch or router.
•
Record the IP Address assigned to the ProtoNode for future reference.
NOTE: The SMC Cloud button (see
) allows users to connect to the
SMC Cloud, MSA Safety’s device cloud solution for IIoT. The SMC Cloud enables secure
remote connection to field devices through a FieldServer and its local applications for
configuration, management, maintenance. For more information about the SMC Cloud,
Figure 23: Changing IP Address via FS-GUI