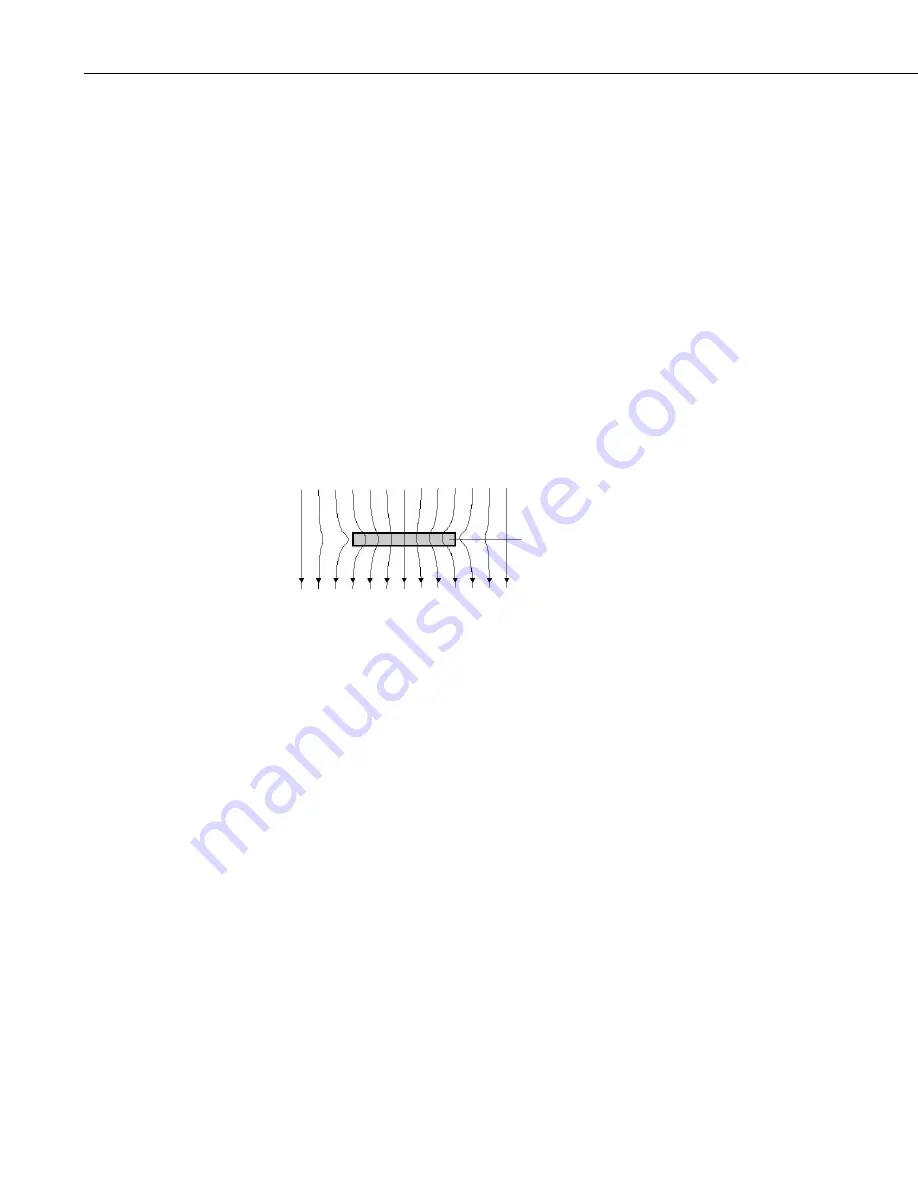
Appendix A. General Theory of Heat Flux Sensors
better if the soil conditions are closer to the reference conditions (see
the sensor specifications) and, in an actual experiment, the expected
error range will probably be
±
10%.
The reference conditions for the calibration are a thermal conductivity
of 0.8 W/mK and a nominal temperature of 20°C.
A.2 Extended Theory
It is obvious that there is the possibility that the sensor itself can
significantly disturb the phenomenon that it is supposed to measure.
By adding a sensor to the material under observation, you can add
additional, and sometimes differing, thermal resistances.
The deflection error, as shown in Figure A-2, represents the effect
that, as a result of differing resistances, the flow pattern will change,
especially at the edges of the heat flux sensor. The order of
magnitude of this error for strongly different thermal conductivity
values between the sensor and its environment (for example 0.6 for a
typical sensor and 0.03 for an insulating wall) is about 40%.
FIGURE A-2. Deflection error
The heat flux is deflected at the edges of the sensor. As a result, the
heat flow at the edges is not representative.
Apart from the sensor thermal resistance, the contact resistance
between the sensor and surrounding material require special attention.
The conductivity of air is approximately 0.02W/mK which is ten
times smaller than that of the heat flux sensor. It follows, therefore,
that air gaps can form major contact resistances. In all cases the
contact between sensor and surrounding material should be as close
and as stable as possible, so that it will not influence the
measurements.
The aspects of differing thermal properties between sensor and its
environment can also be dealt with during the measurement using a
higher accuracy self-calibrating type of heat flux sensor.
A-2