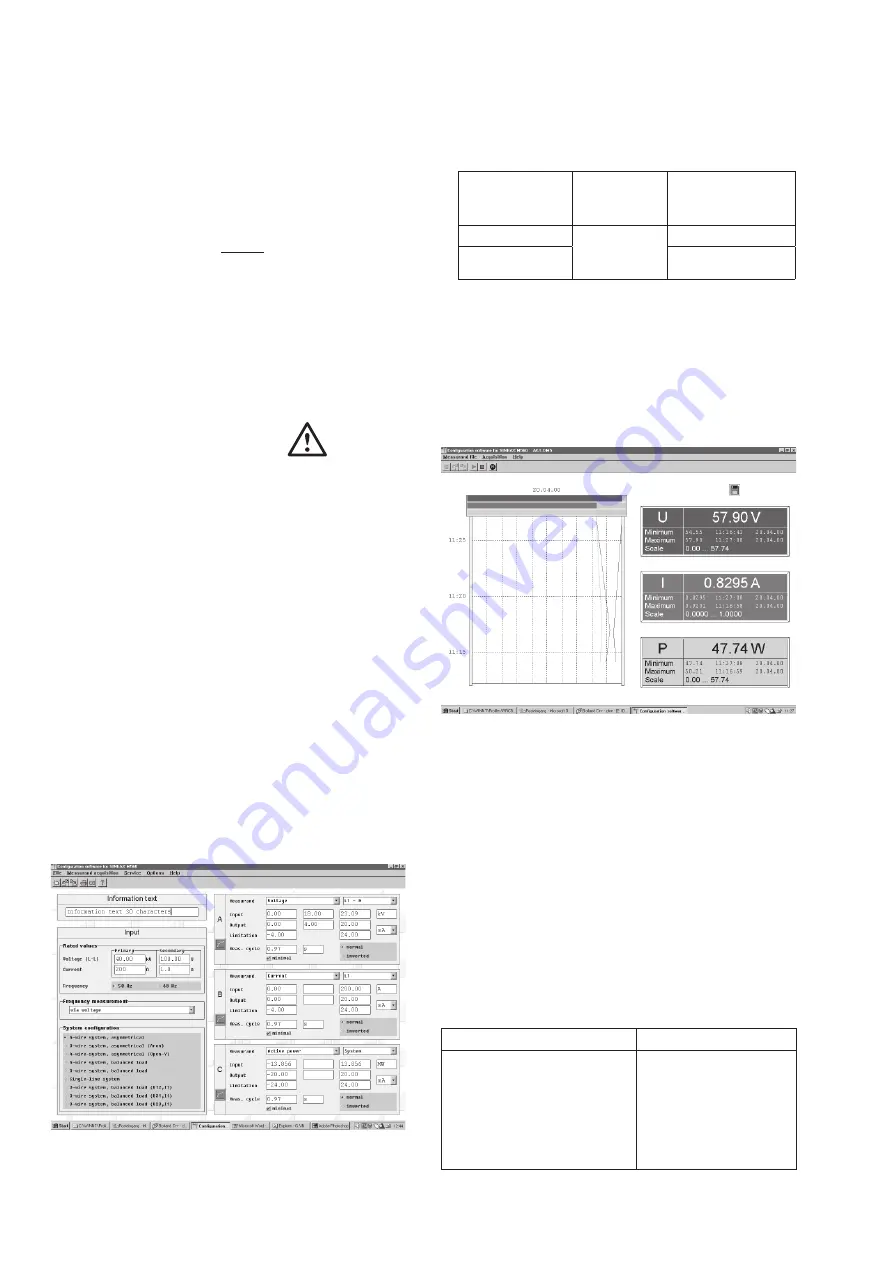
30
Programming connector on transducer
The programming connector on the transducer is connected
by the programming cable PRKAB 560 to the RS-232 inter-
face on the PC. The electrical insulation between the two is
provided by the programming cable.
Ambient conditions
Nominal range of use
for temperature:
0…15…30…45 °C
(usage group II)
Operating temperature: – 10 to + 55 °C
Storage temperature:
–40 to + 85 °C
Annual mean
relative humidity:
≤ 75%
Altitude:
2000 m max.
Indoor use statement
5.2 Programming the transducer
The transducers SINEAX M561 / M562 / M563 have an
integrated RS 232 C interface (SCI).
The existing programmation can be matched conveniently
to a changed situation and stored via the “Confi guration
software for M 560” (Order number 146 557).
For this purpose, the RS 232 output of the transducer must
be connected to a PC via the RS 232 C (SCI) programming
cable (Order number 147 779 and 143 587) and the trans-
ducer must be supplied with power supply.
The confi guration software has an easy-to-operate, clear
menu structure which allows for the following functions to
be performed:
• Reading and displaying the programmed confi guration of
the transducer
• Clear presentation of the input and output parameters
• Transmission of changed programmation data to the
transducer and for archiving of a fi le
• Protection against unauthorized change of the program-
mation by entry of a password
• Confi guration of all the usual methods of connection
(types of power system)
Fig. 5. Presentation of all programmation parameters in the main
menu.
• Easy change of input and output parameters
WARNING: Watch for maximum input voltage on trans-
ducers with internal power supply connection from mea-
suring input:
Power supply
Power supply
connection
Maximum input
voltage across the
power supply
24 - 60 V AC
Internal from
measuring
input
69 V AC
85 - 230 V AC
264 V AC
• Selection possible for frequency measurement via vol-
tage or current
• Possibility to reset the slave pointer of the output quantity
involved
• Parameter setting of outputs A to C (input of measured
quantity, upper limits, limitation of upper limits and re-
sponse time per output, possible up to max. 30 s)
• Graphics display of the set system behaviour of each
output
Fig. 6. Displaying, recording and evaluation of measurements.
Provision is also made for the following ancillary functions:
• Displaying, recording and evaluation of measurements on
a PC
• The simulation of the outputs for test purposes
• Printing of nameplates
6. Reconfi guring the analogue outputs
The alternative confi gurations for the analog outputs can be
seen from Table 1.
Table 1:
Action
Procedure
Change the current full-
scale value from, for example,
20 mA to 10 mA
(a hardware setting always
thas to be made when
changing from a lower to
a higher value)
Reconfi gure the
software,
but do not change the
hardware setting.
Accuracy is reduced.