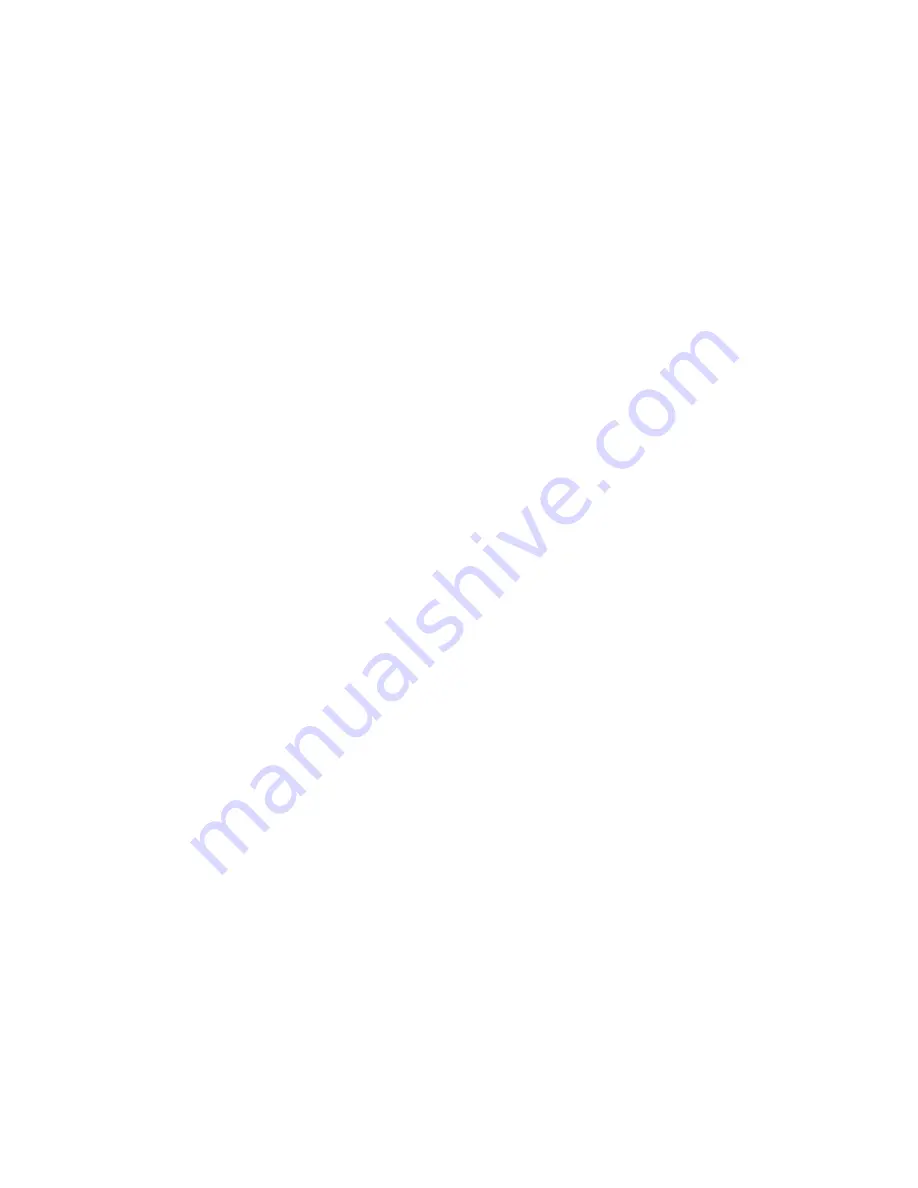
LEFM 3xxCi User Manual
IB1406 Rev 12
Section 1
Page 7
August 2017
Model Number
Meter Body Model Numbers
The model number defines construction and features. From the model number, a user can identify and
verify the component type, meter size, piping thickness, construction material, ANSI rating, and enclosure
type.
MODEL NUMBER CODE: LEFM 3BC-D-E-F-G-H-J-K-L-M-N-P-Q-R
B = 80 FOR 8 PATH METERS
B = 40 FOR 4 PATH METERS
C = Ci-G3 FOR INTEGRAL ELECTRONICS
C = Ci-R-G3 FOR REMOTE ELECTRONICS AND 1 J-BOX PER MANIFOLD
C = Ci-RB-G3 FOR REMOTE ELECTRONICS AND 1 J-BOX FOR WHOLE METER
D = NOMINAL PIPE SIZE (e.g., 04 = 4 INCH, 16 = 16 INCH ....)
E = PIPE SCHEDULE (SCHEDULE 5 THRU 160 AND XXS)
F = CF FOR FORGED CARBON STEEL
F = CC FOR CAST CARBON STEEL
F = SF FOR FORGED STAINLESS STEEL
F = SC FOR CAST STAINLESS STEEL
F = DF FOR FORGED DUPLEX STEEL
F = DC FOR CAST DUPLEX STEEL
F = LF FOR FORGED LOW TEMPERATURE CARBON STEEL
F = LC FOR CAST LOW TEMPERATURE CARBON STEEL
F = HF FOR HASTELLOY
F = IF FOR INCONEL FORGED
G = ASME FLANGE RATING (CLASS 150, 300, 600, 900, 1500, 2500)
H = B FOR MANIFOLDS INTEGRAL WITH METER BODY
H = D FOR SPLIT MANIFOLDS INTEGRAL WITH METER BODY
H = E FOR SINGLE TRANSDUCER ENCLOSURES INTEGRAL WITH METER BODY
J = W FOR WELD NECK RAISED FACE FLANGES
J = R FOR WELD NECK RTJ FACE FLANGES
J = O FOR OTHER FLANGE VARIETY
J = S FOR SLIP-ON FLANGES
K = L FOR LOCTITE E40 EXP POTTING MATERIAL
L = B FOR SECONDARY SEAL DESIGN TRANSDUCER HOUSING IN ACCORDANCE WITH ISA 12.27.01 (DUAL SEAL)
L = C FOR DOUBLE O-RINGS
M = N FOR NO PRESSURE PORT OPTION
M = P FOR PRESSURE PORT OPTION
N = A FOR ALUMINUM MANIFOLDS COVERS
N = S FOR STAINLESS STEEL MANIFOLDS COVERS
P = 1 FOR ONE TRANSMITTER
P = 2 FOR TWO TRANSMITTERS
Q = G FOR GAS TRANSDUCER HOUSINGS
R = "BLANK" FOR NO CUSTOM OPTION
R = C FOR CUSTOM OPTION
Example: For a forged carbon steel 380Ci meter that has a head mounted electronics, 6 inch NPS,
Schedule 40, 150# weld neck flanges with raised faces, no pressure port, aluminum manifold covers,
having the secondary seal design and having no other custom features – the model code would be:
LEFM380Ci-G3-06-40-CF-150-B-W-L-B-N-A-1-G