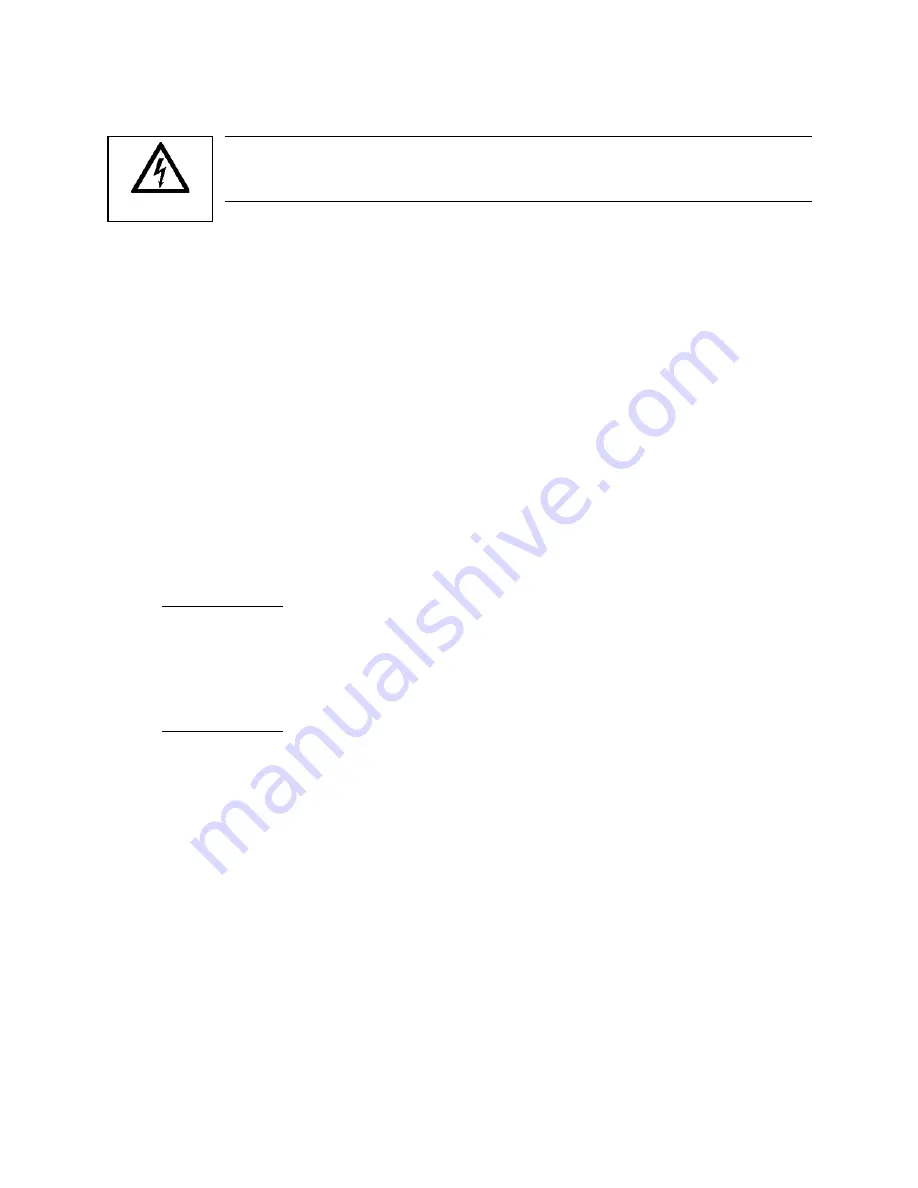
LEFM 3xxCi User Manual
IB1406 Rev 12
Section 2
Page 15
August 2017
To avoid damaging the swivel hoist rings, never use cables, hooks, or chains to lift the meter body.
Lift the meter gradually. Exposing the swivel hoist rings to shock loads can result in damage to the
hoist ring. DO NOT USE any swivel hoist ring exposed to shock loads.
5.
After lifting, remove the swivel hoist rings and store away from exposure to
moisture, extreme temperatures, and other adverse conditions.
6.
Reinsert the plug bolts into the tapped holes to protect them from debris and corrosion.
Meter Installation
Install the flowmeter so that:
•
The acoustic paths are horizontal (with the transmitter and nameplate on top) to decrease the
likelihood of debris accumulating in the sensor wells.
•
The flow arrow indicates the flow direction for positive flow.
•
All wiring to the transmitter is routed in shielded conduit / armored cable that meets site
environment specifications.
•
All power connections on site shall go through an equipment switch or circuit breaker employed as
a disconnecting device. This switch shall be easily accessed and be marked as the disconnecting
switch for the transmitter. This switch shall meet the requirements of IEC 60947-1 and IEC 60947-
3 and site electrical codes.
•
If using DC power, power cable must be installed in separate conduit from all other cabling. This is
to meet requirements of IEC 61000-4-4 (2004-07).
•
380Ci Installations: Upstream of the meter there should be at least 5 diameters of straight pipe of
the same nominal diameter as the meter. If a straightening/conditioning element is used, 10
diameters of straight pipe between the conditioner and flowmeter are recommended with an
additional 5 diameters upstream of the flow conditioner. Downstream of the meter, there should be
at least 3 diameters of straight pipe of the same nominal diameter as the meter. Refer to Figure 2.
for details.
•
340Ci Installations: Upstream of the meter there should be at least 10 diameters of straight pipe of
the same nominal diameter as the meter. If a straightening/conditioning element is used, 10
diameters of straight pipe between the conditioner and flowmeter are recommended with an
additional 5 diameters upstream of the flow conditioner. Downstream of the meter, there should be
at least 3 diameters of straight pipe of the same nominal diameter as the meter.
•
Process temperature and pressure should be measured within 2 to5 diameters downstream of the
meter. The pressure measurement may be made at the downstream spool ahead of the
temperature measurement or optionally at the meter body itself.
CAUTION