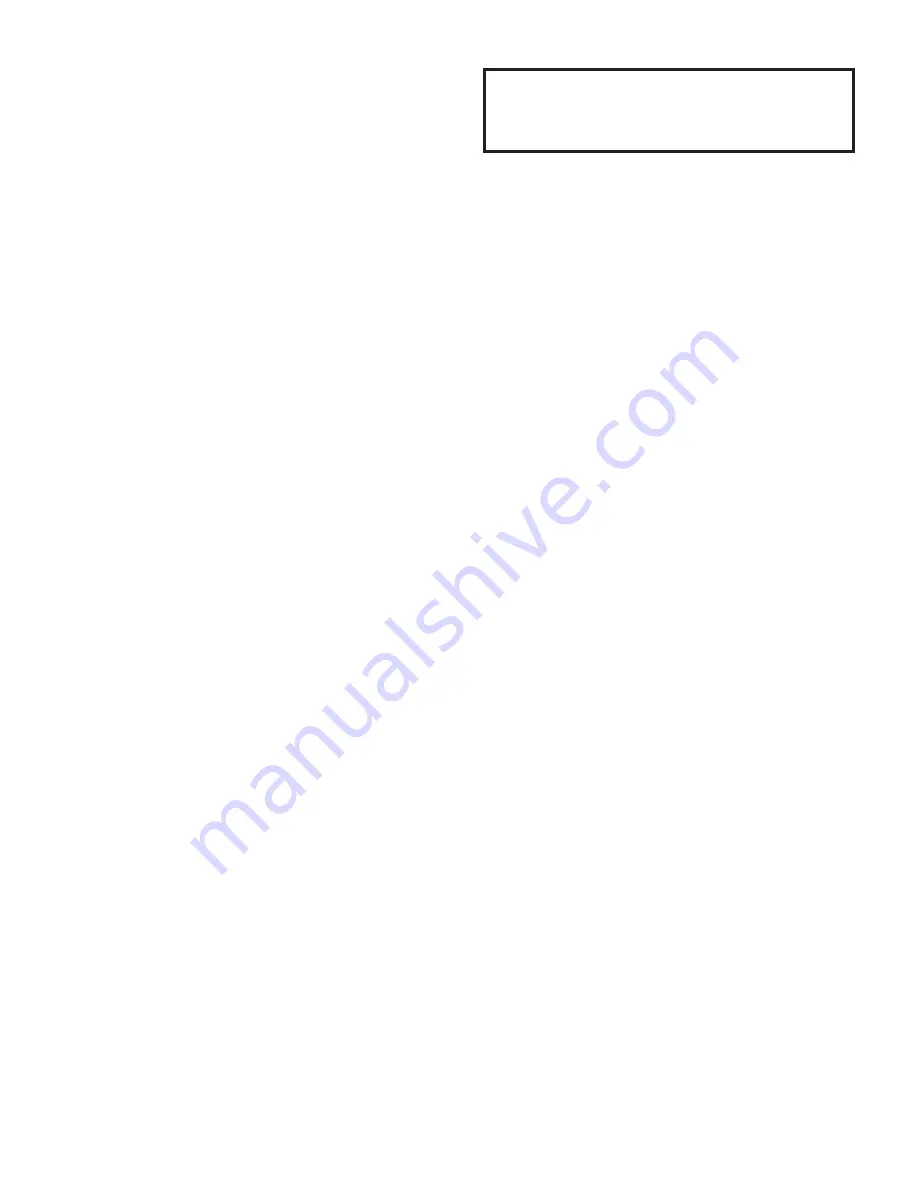
E-Series Technical Manual
11
Cambridge Air Solutions
START-UP CHECKLIST
Once the air handler has been assembled, installed,
and piped, attention must be directed to individual
components for proper operation. Before operating the
unit, complete the Pre Start-up checklist. Sign and send
copy to Cambridge.
NOTE: Follow all Manufacturers’ Guides for Pre Start-
Up. The following is a guide only.
1. Remove any debris from the unit interior.
a. Remove all foreign material from the drain pan
and check drain pan opening and condensate line
for obstructions.
b. Ensure the unit has been installed level.
c. Ensure the damper operator motors and
connecting linkage has been installed.
d. Verify the damper operation and linkage
alignment.
e. Check that the air filters are in place and
positioned properly.
f. Close and secure all unit access doors
2. If differential pressure switch is provided on filter
rack, adjust per system requirements.
3. Inspect electrical connections to the unit and unit
controllers.
a. Connections should be clean and secure.
b. Compare the actual wiring with the unit
diagrams.
c. eference the appropriate controller manual for
more details about starting units with factory
mounted controls.
4. Ensure all piping, connections, vents and drains have
been connected properly
5. Ensure supply and return air ducts have been
connected properly.
6. Check piping and valves for leaks.
7. Fill sump tank with water and adjust float to ½”
below overflow drain.
8. Check that the fill and drain valve are installed and
wired to the 24-hour timer and freeze stat. Set the
24-hour fill and drain timer to local time. The drain
and refill feature is factory set to turn off the sump
for 1 hour between 4 am to 5 a.m., and is manually
adjustable to User’s requirements.
WARNING:
Whenever power is interrupted, the 24-hour clock
must be reset to local time.
9. Turn power to unit on and check for any electrical
shorts.
a. Measure and record the motor voltage and
amperage on all phases to ensure proper
operation. The readings should fall within the
range given on the motor nameplate.
b. Check fan rotation and correct if necessary.
c. Check all interlocks to be sure that connected
components work per plans and specifications.
10. Check that line and sump pump voltages and
amperages as per the nameplate.
11. Confirm the time delay has been set to 1 minute on
the sump pump(s).
12. Verify the low water level float switch located in
sump is working properly and will turn the pump(s)
on.
13. Start-up the fan per manufacturer's instructions. After
both the fan and sump are running and operating
properly, check that water is not being carried over
into the airstream from the media pads or sump.
14. Cycle damper actuators to ensure they open and close
freely.
If there is water carryover from the media pads
perform the following procedure:
15. Check for proper positioning of media pads on the
sides of the pads are arrows marking the direction of
air flow. If media pads are correctly positioned then
check for air bypassing between the media pads and
their frames. If air is bypassing, then place a strip
of foam gasketing between the media pads and side
channel to compress the media pads and fill the gap.
16. After twenty (20) minutes observe media for
complete wetting and check that there are no dry
streaks. Open balancing valve to increase water flow
and close valve as necessary to reduce water flow to
media pads. (Initial factory-set position of valve is ½
open).