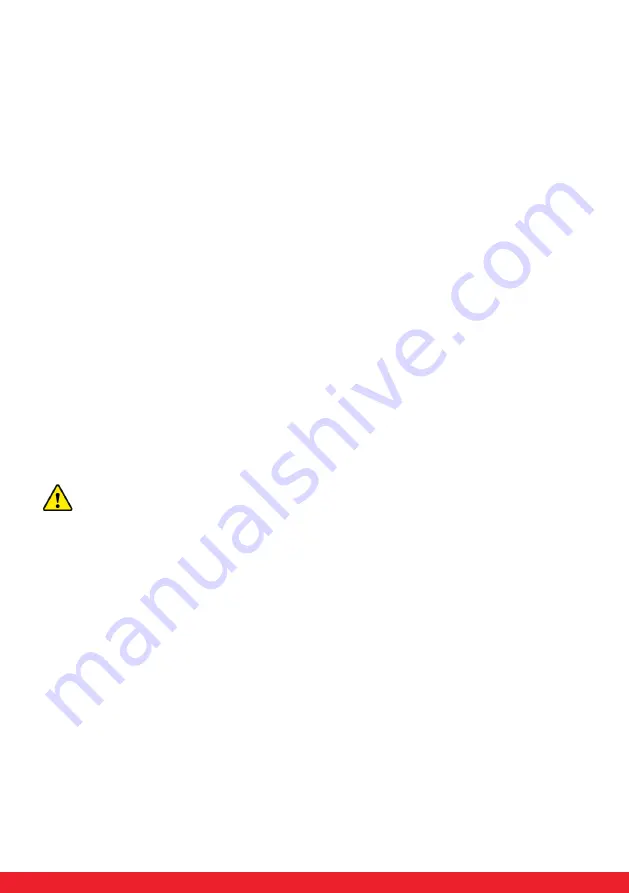
6/36
1. INTRODUCTION
This manual contains all the necessary information on the installation and operation of the PL and PL-T
Fork Positioners.
Some of the maintenance operations should only be carried out by professional technicians. If you
require this information and the maintenance steps, please contact your dealer. Also included in this
manual are a number of safety instructions to create a safe working environment.
With this equipment you can position the forks and sideshift the load (PL-T), resulting in more accurate
handling and placement of the load. This makes it possible to reduce your overall handling time,
reduce damage to pallets and products and increase your manoeuverability, even through tight
corners.
Check your machine manual to make sure you opt for the equipment with the correct load capacity.
Do not use this product for any other purposes.
Please read the manual thoroughly and observe the safety procedures before putting the unit into
operation. The operator and all persons who come into contact with the equipment should read it
carefully and regularly and have access to it at all times.
Keep this manual near the equipment and in a safe place for future reference.
Contact your dealer for any further questions or concerns you may have.
We guarantee a long period of trouble-free operation if the unit is operated and maintained correctly.
We hope you will enjoy working with your attachment.
This equipment may be unsafe if adequate maintenance is neglected. Therefore,
adequate maintenance facilities, trained personnel and procedures should be provided.
Maintenance and inspection shall be performed in conformity to the following practices:
1. A scheduled planned maintenance, lubrication and inspection system should be followed
(see maintenance instructions chapter 7).
2. Only qualified and authorised personnel shall be permitted to maintain, repair, adjust,
and inspect the equipment.
3. Modifications and additions which affect capacity and safe operation shall not be
performed by the customer or user without the manufacturer’s prior written approval.
Capacity, operation and maintenance plates or decals shall be changed accordingly.
4. If modifications are made without the written approval of the manufacturer, the warranty
will no longer apply.
Any person in charge of putting the machine into operation, the operation itself or the
maintenance of the machine is urged to carefully read and observe the following instructions.
Make sure that the operators of this product are qualified and authorised to do so and are
familiar with the safety instructions, making sure to follow all the procedures. Neglecting these
instructions can cause injury or death.