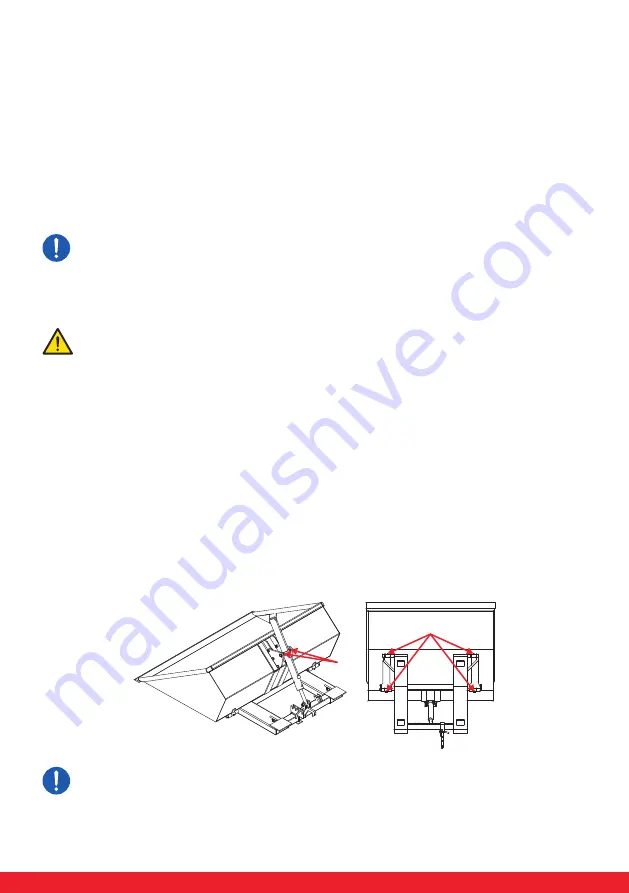
17/28
2. Cleaning
Only clean the equipment with a cloth dampened in a soap solution (REF 131TA5500)* or TotalSource
wipes (REF 147TA3378). Do not use solvents, petrol, strong detergents etc.
If the equipment is heavily soiled, the use of a pressure cleaner is only permitted providing that it is set
to a maximum of 200 bar.
When you use a high-pressure cleaner, do not direct the jet onto the bearings and seals, otherwise the
grease will be washed out and the lifespan of the machine will be shortened.
Never use sandpaper or abrasive material on the hydraulic scoop.
Can be done by the user.
* Soap solution must be diluted 5 to 10%. Use the soap solution to wash off the dirt and wipe
off the soap residue with a cloth dipped in clean water.
3. Check the connections of the hydraulic system
Make sure that the hydraulic system is connected with the correct hydraulic hoses (See chapter 5).
Never try and search for leaks or plug a leak by hand. Liquids under high pressure can easily
penetrate skin and clothing, and may cause serious injuries.
Replace damaged hydraulic hoses to prevent them from breaking and causing accidents.
May only be done by a qualified service technician and according to the manufacturer’s instructions.
4. Lubrication
After every 10 hours, lubricate the hinges of the device.
A periodic coating of lubricating oil at pivot points and the hydraulic cylinder will help to prevent rust
and assure that the pump assemblies move freely.
Recommended lubricants include ‘Multipurpose Lithium EP2 grease’ (REF 165TA3769).
Can be done by the user.
Where to lubricate?
Please see picture below for the pivot points (A) that need a periodic coating of lubricant.
Use a non-abrasive grease to lubricate the hydraulic parts.
A
A
Summary of Contents for BH24466
Page 21: ...21 28 10 ANNEXES 10 1 CE certificate...
Page 22: ...22 28...
Page 26: ...26 28 NOTES...
Page 27: ...27 28 NOTES...