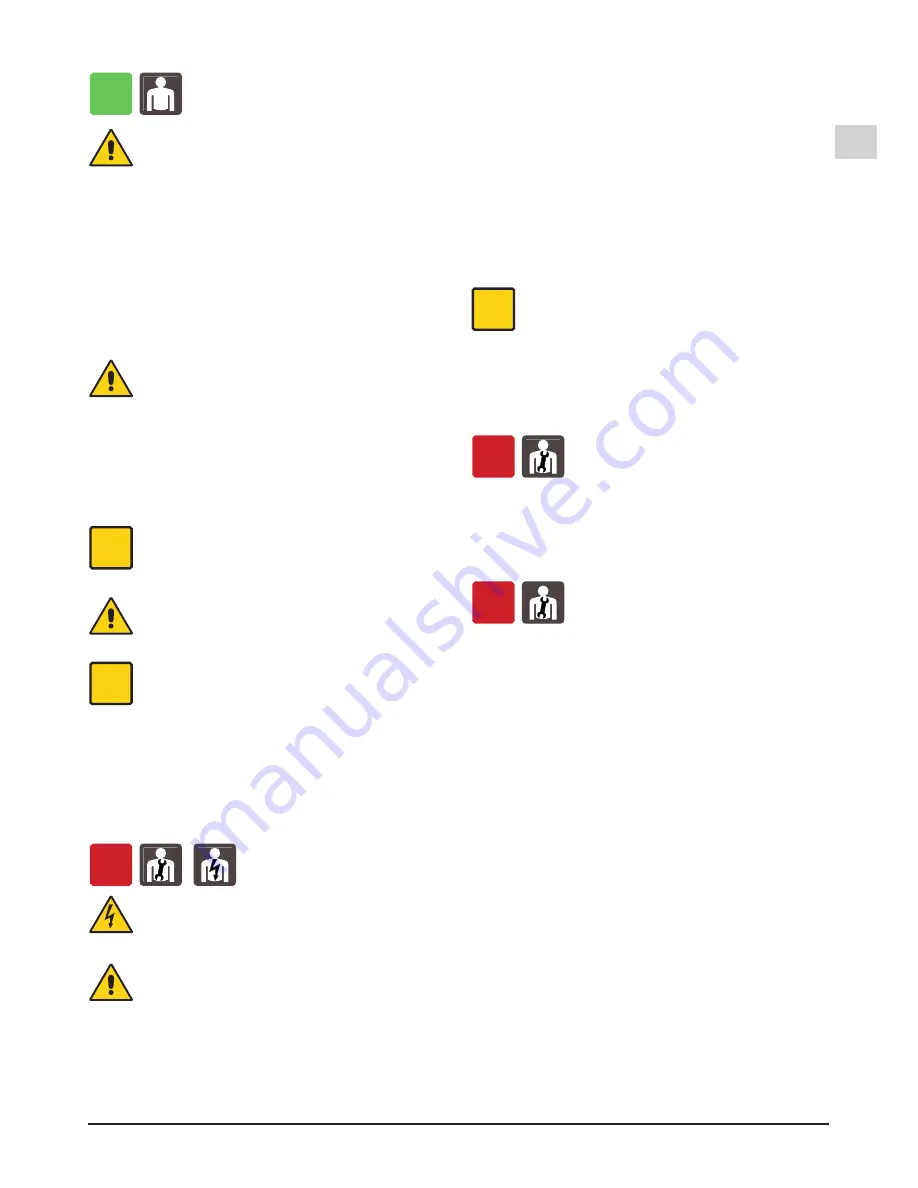
GB
BS...IMAT Rev2 - Operating Instructions
Page 7 / 12
7.6. Switch off of the pump
ON
The appliance must be switch off every time
there are faults.
The product is designed for a continuous duty, the
switch off is performed by disconnecting the power
supply by means the expected disconnecting
devices (see paragraph “6.5 Electrical connection”).
8. MAINTENANCE
Before any operations it's necessary to disconnect
the power supply.
If required ask to an electrician or to an expert
technician.
Every maintenance operations, cleaning
or reparation executed with the electrical
system under voltage, it could cause serious
injuries to people.
In case of extraordinary maintenance, or
maintenance operations that require part-removing,
the operator must be a qualified technician able to
read schemes and drawings.
It is suggest to register all maintenance operation
executed.
i
During maintenance keep particular
attention in order to avoid the introduction of
small external parts, that could compromise
the device safety.
It is forbidden to execute any operations with
the direct use of hands. Use water-resistant,
anti-cut gloves to disassemble and clean the
booster set.
i
During maintenance operations external
personnel is not allowed.
Maintenance operations that are not described
in this manual must be made only by special
personnel authorized by Calpeda.
For further technical information regarding the use
or the maintenance of the device, contact Calpeda.
8.1. Routine maintenance and inspection
OFF
Before every maintenance operations
disconnect the power supply and make
sure that the device could not accidentally
operate.
Close the suction and delivery gate valves
and before attempting any maintenance
activity.
It is suggested to make an inspections at least
every 6 months. The inspection must include:
1. Check that there are no leaks especially around
the area of the pump seals.
2. Check for any corrosion or signs of wear.
3. Check that the pump rotate freely.
4. Check that there is no sign of water at the vessel
air valve by quickly depressing the air valve
needle.
5. Check that the pump/s are operating correctly
and quietly without excessive vibration.
6. Check that the system operates smoothly and
comes to rest when there is no demand and the
set pressure has been reached.
7. Check all electrical cables and fittings for signs of
damage or wear.
8. Check the vessel pre-charge.
9. Check the operation of any float switches or
safety or protection devices.
i
We advise that for a reliable and constant
supply of water that you take out a
maintenance contract. These are especially
devised for the set you have and the work is
carried out by fully qualified and experienced
staff.
8.2. Dismantling the system
OFF
Close the suction and delivery gate valves and
drain
the booster set before dismantling.
9. DISPOSAL
OFF
The final disposal of the device must be done by
specialized company.
Make sure the specialized company follows the
classification of the material parts for the separation.
Observe the local regulations and dispose the
device accordingly with the international rules for
environment protection.
Changes reserved.