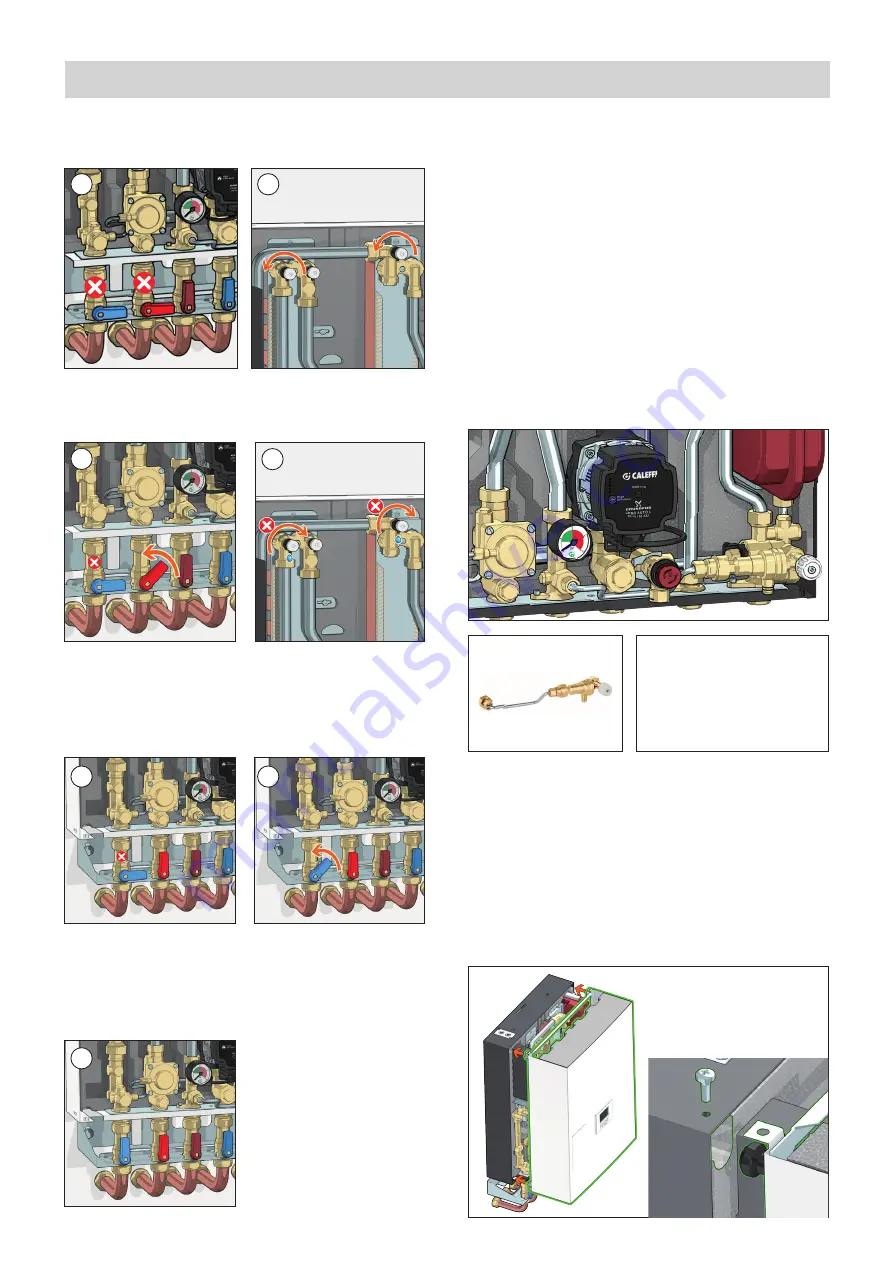
9
A
B
C
N.B.
during the procedures for venting/draining the system use
suitable measures to avoid the risk of any liquid dripping onto the
electronic components.
Vessel pre-charge check
Perform the following steps:
- Use a pressure gauge to check the pre-charge value
- If necessary, restore the pre-charge value shown in the technical
specifications.
Filling the user system
SATK32 series HIU can be fitted with a charging unit equipped with a
backflow preventer (F), check valve (E) and cock (G) (code 572120).
When filling the system for the first time or for subsequent top-up
procedures following a heating circuit pressure switch fault, restore the
system pressure (0,12–0,2 MPa - 1,2–2 bar) by opening cock (G) and
checking the value by means of the pressure gauge (D).
Once the correct pressure has been reached, close the cock (G),
vent the system and re-check the pressure (repeat the filling process
if necessary).
System start-up
Before starting the HIU, visually check the hydraulic connections for
the absence of any leakage and all the electric connections. After
finishing the check, activate the electric supply to the HIU and check
for the presence of any error signal.
If there is any, eliminate the fault indicated (see page 18) and proceed
with setting the set point of the domestic water and heating cycles,
programming the remote user interface according to the desired
temperatures and times, and checking the operating cycles.
Commissioning
Fitting the cover
Fit the cover on the HIU by inserting the pins (A) in the locations
provided (B).
Secure the cover by tightening the 4 screws provided (C).
Filling procedure for SATK32 centralised system
1. Open the air vent cocks upstream of the DHW and HEAT
regulating valves.
2. Slowly open the primary circuit flow shut-off valve at the HIU inlet.
At this stage, shut off the air vent cocks when water begins to
come out (fig. 2b).
3. When filling is complete,
slowly open the primary circuit
shut-off valve at the HIU inlet
until it is fully open.
4. Slowly open the primary
circuit return shut-off valve at
the HIU outlet.
5. When filling is complete,
slowly open the primary
circuit return shut-off valve at
the HIU outlet until it is fully
open.
1a
1b
2a
2b
3
4
5
G
E
F
D
* Filling unit not used in the UK
market. For information on the
user system filling procedure,
please refer to the technical
documentation for the product
ALT-HIUFLP in compliance
with regulation G24 PTII.