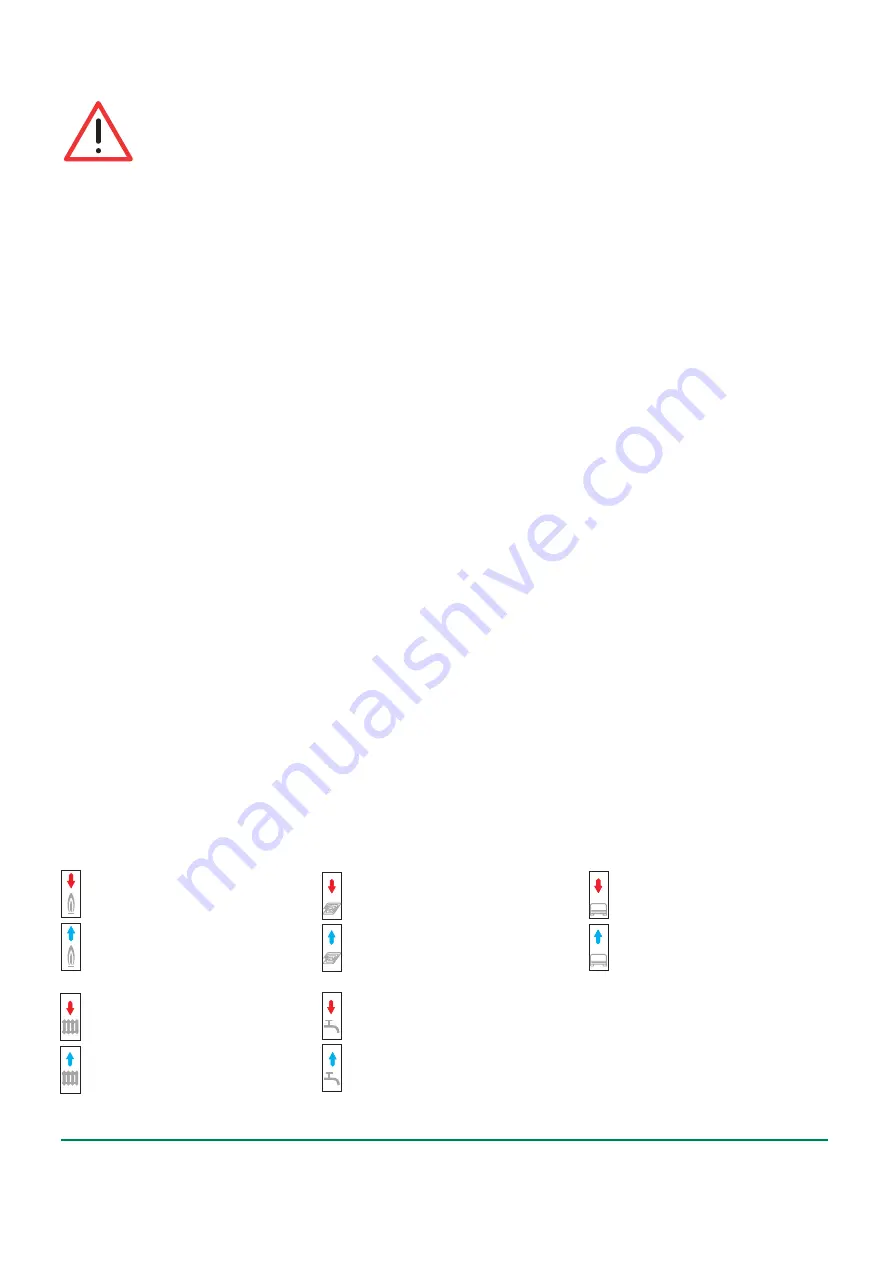
WARNINGS
These instructions must be read and understood before installing and servicing the device.
IMPORTANT! FAILURE TO FOLLOW THESE INSTRUCTIONS COULD RESULT IN A SAFETY HAZARD!
1 The device must be installed, commissioned and serviced by qualified technical personnel in accordance with national regulations and/or relevant local requirements.
2 If the device is not installed, commissioned and serviced correctly in accordance with the instructions provided in this manual, it may not work properly and may
endanger the user.
3 Clean the pipes of any particles, rust, incrustations, limescale, welding slag and any other contaminants. The hydraulic circuit must be clean.
4 Make sure that all connection fittings are watertight.
5
When connecting water pipes, take care not to subject the threads to excessive mechanical stress. Over time this could result in breakage, with water leaks causing
damage and/or injury.
6 Water temperatures higher than 50 °C may cause severe burns. When installing, commissioning and servicing the device, take the necessary precautions so that
these temperatures will not be hazardous for people.
7 In the case of particularly hard or impure water, the device must be fitted for filtering and treating the water before it enters the device, in accordance with current
legislation. Otherwise the device may be damaged and will not work properly.
Important note: system washing must take place in accordance with current local regulations. In any case, we recommend the use of specific
by-passes for the first washing cycles, in order to avoid water containing impurities from flowing into the device. At the end of the procedure, make
sure all the system and device filters are clean.
8 Any use of the device other than its intended use is prohibited.
9 Any combination of the device with other system components must be made while taking the operational characteristics of both units into consideration.
10 An combination coupling could compromise the operation of the device and/or system.
IMPORTANT
: Risk of electric shock. Live parts. Shut off the electric supply before opening the device enclosure.
1 During installation and maintenance operations, always avoid direct contact with live or potentially hazardous parts.
2 The device must not be exposed to dripping water or humidity, direct sunlight, the weather, heat sources or high intensity electromagnetic fields. This device cannot
be used in areas at risk of explosion or fire.
3 The device must be connected to an independent two-pole switch. If work must be carried out on the device, cut off the electric supply first. Do not use devices
with automatic or time reset, or which may be reset accidentally.
4 Use suitable automatic protection devices in accordance with the electrical characteristics of the region in which the device is installed and in compliance with
current legislation.
5 The device must always be earthed before it is connected to the electric supply. If the device must be removed, always disconnect the earth connection after
disconnecting the electric supply conductors. Check that the earth connection has been made to the highest of standards under applicable legislation.
6 Electrical installation must only be carried out by a qualified technician, in accordance with legal requirements.
7 The appliance does not contain asbestos or mercury.
8 The device is not designed for use by persons of reduced mental, physical or sensory capacity (including children) or persons lacking experience, unless they are
supervised or instructed in use of the device by a person responsible for their personal safety.
LEAVE THIS MANUAL AS A REFERENCE GUIDE FOR THE USER. DISPOSE OF THE PRODUCT IN COMPLIANCE WITH CURRENT LEGISLATION
THE MANUFACTURER RESERVES THE RIGHT TO CEASE PRODUCTION AT ANY TIME AND TO MAKE ANY CHANGES DEEMED USEFUL OR NECESSARY
WITHOUT THE OBLIGATION OF PRIOR NOTICE.
SAFETY INSTRUCTIONS
NOTES
:
1 Install water hammer arresters to compensate for any overpressure in the domestic water circuit;
2 In the presence of hot water recirculation or if a check valve is fitted into the domestic cold water inlet, suitable devices must be used to accommodate the
expansion of the medium contained within the system and the heat interface unit;
3 All hydraulic connections must be visually checked while pressurising the system. Vibration during transport may cause the connections to become loose. If a fitting
needs to be tightened apply a proper tightening torque, otherwise the components may be damaged by overtightening.
For the updated version of the technical documentation refer to www.caleffi.it.
Key to symbols
2
Primary circuit flow
Primary circuit return
Domestic hot water outlet
Domestic cold water inlet
High temperature circuit flow
High temperature circuit return
Medium temperature circuit flow
Medium temperature circuit return
Low temperature circuit flow
Low temperature circuit return
Primary circuit flow
Primary circuit return
Domestic hot water outlet
Domestic cold water inlet
High temperature circuit flow
High temperature circuit return
Medium temperature circuit flow
Medium temperature circuit return
Low temperature circuit flow
Low temperature circuit return
Primary circuit flow
Primary circuit return
Domestic hot water outlet
Domestic cold water inlet
High temperature circuit flow
High temperature circuit return
Medium temperature circuit flow
Medium temperature circuit return
Low temperature circuit flow
Low temperature circuit return
Primary circuit flow
Primary circuit return
Domestic hot water outlet
Domestic cold water inlet
High temperature circuit flow
High temperature circuit return
Medium temperature circuit flow
Medium temperature circuit return
Low temperature circuit flow
Low temperature circuit return
Primary circuit flow
Primary circuit return
Domestic hot water outlet
Domestic cold water inlet
High temperature circuit flow
High temperature circuit return
Medium temperature circuit flow
Medium temperature circuit return
Low temperature circuit flow
Low temperature circuit return