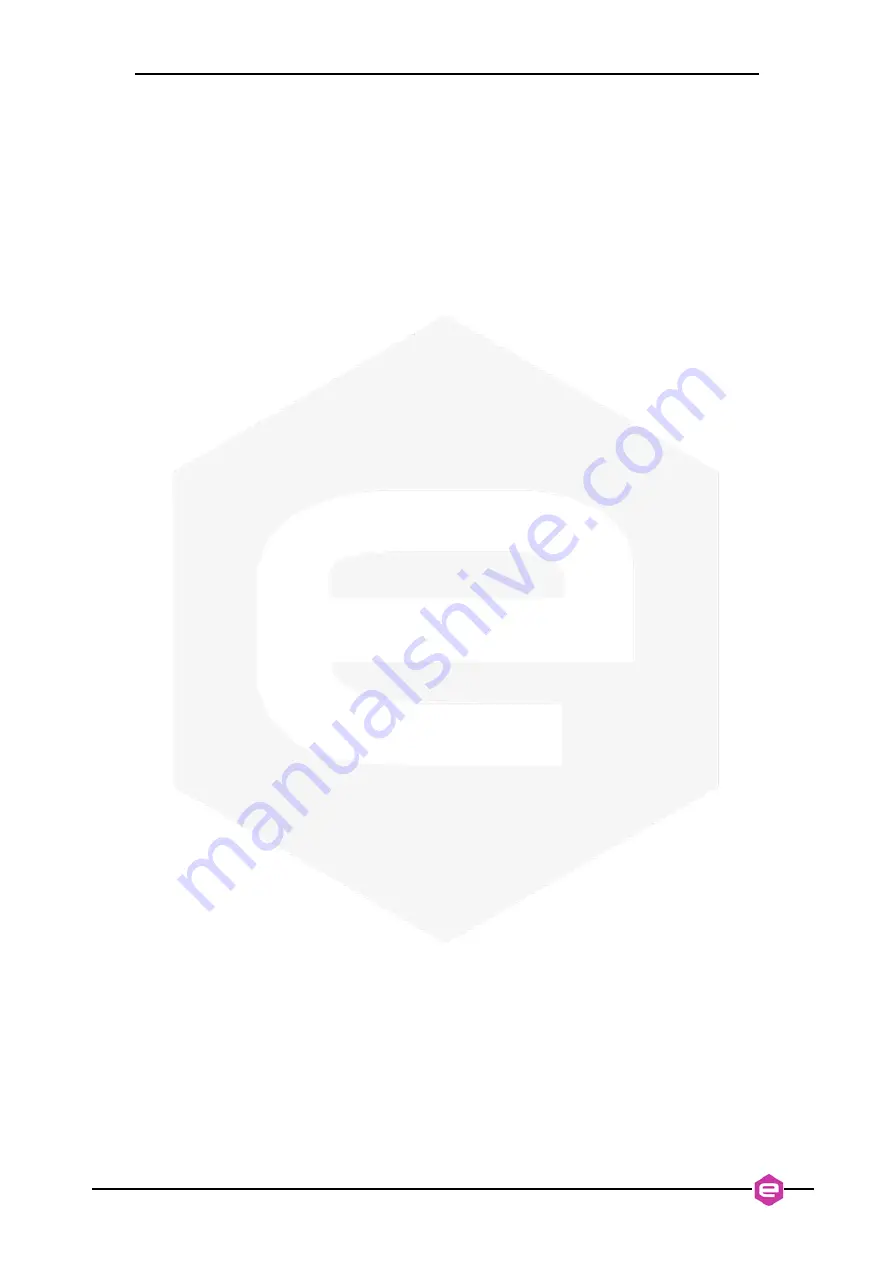
BEST
User’s Manual
BEST Local GUI
29
Regulate
– select which PID to enable,
Source
– select which BPM to use as source for the PID (“BPM Selector”
block in
Figure 15
),
DAC output
– assign the PID output to the desired
PreDAC
output
(“Output Selector” block in
Figure 15
).
The feedback configuration options come into force after pressing the “Update
Config” button.
Lastly, the beam position setpoint can be changed manually by specifying the beam
position (“Position X” and Position Y”) in µm. New values come into effect after
pressing the “Update Setpoint” button.
4.1.3
PID Configuration Panel
The PID parameters of the four independent PID loops available in the
BEST
hardware are all accessible from the GUI main window. To modify a parameter
simply change its value and click the “Update” button to make the changes effective.
The PID parameters (
Figure 22
) are used in the FPGA logic for the
BEST
fast
feedback computation algorithms. The
BEST
system can control and stabilize up to
three variables:
1.
X
: horizontal position;
2.
Y
: vertical position;
3.
I
0
: intensity.
A digital filter (simple average) is applied to the input data received from the
TetrAMMs
before entering the PID (see “AVG” block in
Figure 15
). This
filtering is performed to maximize the signal-to-noise ratio and to reduce the feedback
actuation frequency that can be set using the field “Freq” in the PID Configuration
menu. This parameter is of paramount importance and is correlated to the dynamical
performances of the positioning mechanics driven by the PID. Certain positioners are
stiff, lightweight and fully backlash-free, therefore they can be actuated to track the
setpoints generated by the PID at relatively high frequencies of 100 Hz and above.
Other positioners may be intrinsically slower, therefore they can be actuated at
frequencies of only a very few tens of Hz. Slow thermal drifts are easily compensated
by running the PID at just around 1 Hz.