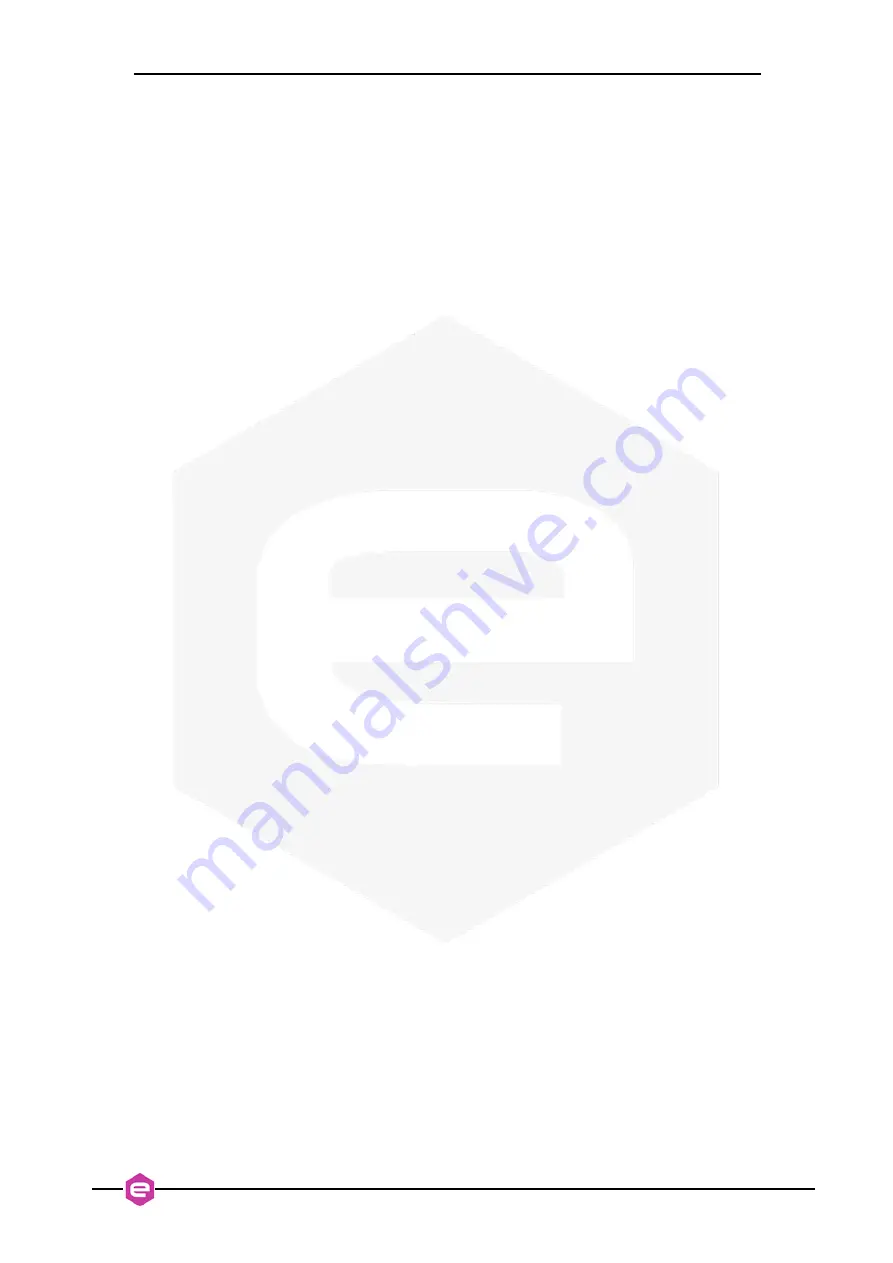
Introduction
BEST
User’s Manual
10
The current from the phBPM are acquired by the
TetrAMM
and sent to the
BEST
Central Unit using a very low latency SFP connection.
The
BEST
Central Unit takes care of all the calculations to obtain the beam position
and intensity information. The
BEST
Central Unit calculates the correction
necessary to stabilize the intensity and position of the beam at the desired setpoint,
using a fast PID algorithm. The correction setpoints are then sent to the actuator block
using a low-latency SFP interface. The critical tasks are performed in hardware using
a FPGA device in order to have a deterministic computing time, maximum calculation
speed and high reliability. The X-ray beam intensity is constantly monitored and can
be used to automatically enable or disable the PID controller, by determining if the
beam is ON (intensity higher than a specific threshold) or if the beam is OFF
(intensity lower than a specific threshold). The control and interface unit offers a local
graphical interface (Local GUI), which allows to fully monitor, manage and control
the beam position and intensity. A standard 10/100/1000 TCP-IP Ethernet link allows
remote control and configuration of this system, hence it is possible to connect the
control unit directly to the beamline control system.
The actuator device, called
PreDAC
, receives the correction/compensation data
calculated by the
BEST
Central Unit and drives the beamline optics, using its
internal high precision digital-to-analog converters to generate an output voltage
signal capable of driving piezoelectric actuators acting on the optical elements. In this
way it is possible to close the control loop and to stabilize the X-ray beam.
The FPGA-based hardware architecture allows performing the control algorithms at a
maximized speed and with very low latency in order to guarantee full effectiveness of
the
BEST
correction performance over a frequency spectrum up to several kHz. The
slower and non-critical tasks (i.e. configuration commands) are separately performed
on an embedded industrial PC running a Linux OS with dedicated software.
The distributed architecture was selected in order to maximize the performance, both
in terms of speed as well as of sensitivity and accuracy, of the whole system. The
TetrAMM
readout system should be placed as close as possible to the phBPM and
the
PreDAC
system as close as possible to the actuator driving the beamline optics
in order to reduce the noise pickup on the analog part of the feedback system. The
internal
BEST
computation and communication between the three system blocks
are all performed in a fully digital way, therefore excluding all additional noise
sources that can strongly affect the controller and stabilization loop performances at
high speed. All three building blocks are interconnected via low-delay fast
communication SFP links running a proprietary protocol. The SFP links on the back
of the
BEST
Central Unit are directly interfaced to a powerful FPGA board that
performs the position and control algorithms and sends correction values to the DACs
embedded in the
PreDAC
device.
The
BEST
system was designed with one of its main focuses on configurability
expandability and flexibility, being able to control and monitor up to two readouts -
TetrAMM
devices (i.e. up to 8 picoammeter channels) and one multichannel
actuator -
PreDAC
device (i.e. up to 4 DAC channels) from one single
BEST
central unit.