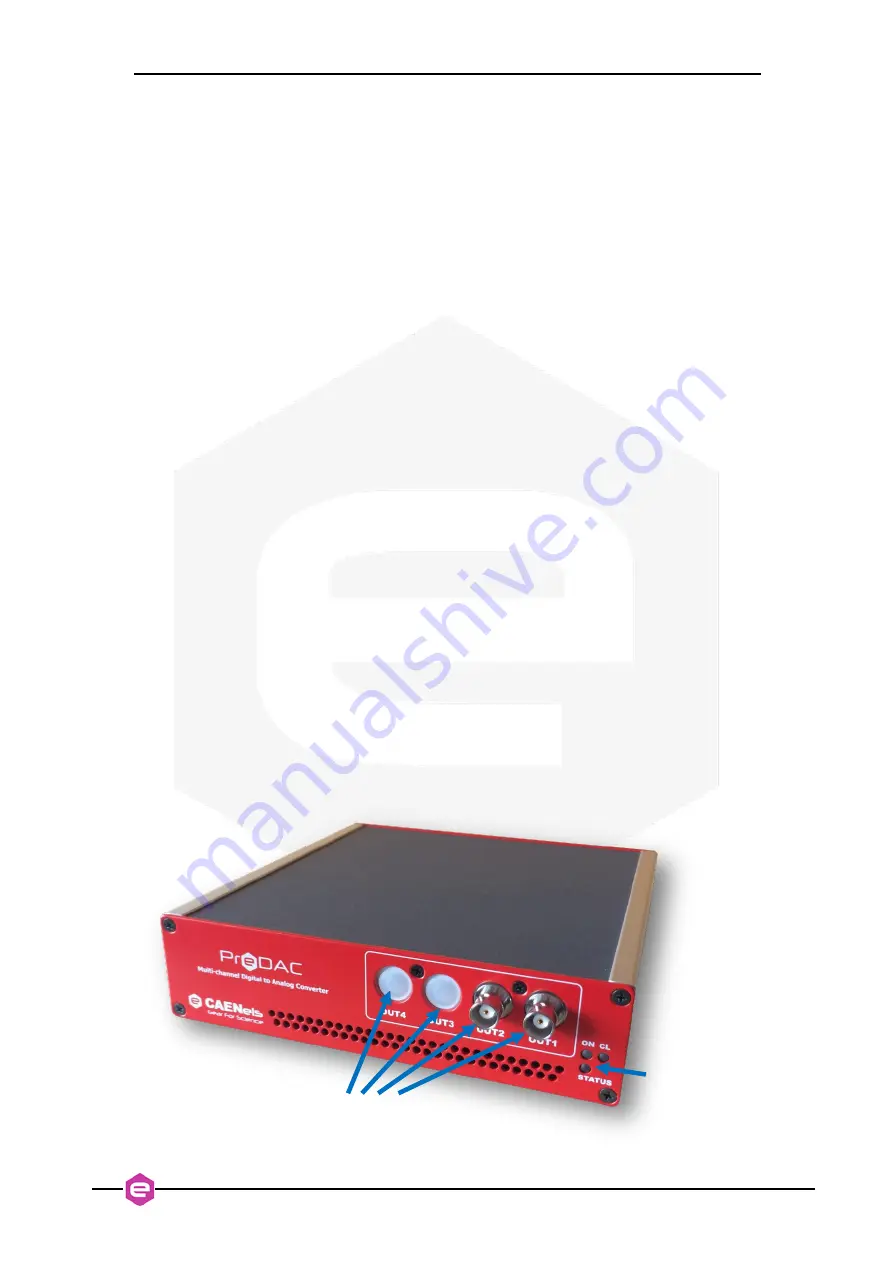
Introduction
BEST
User’s Manual
14
1.3
PreDAC
Overview
The
PreDAC
is a (up to) 4-channel, 21-bit resolution, wide-bandwidth Digital to
Analog Converter (DAC) which is especially designed for seamless operation within
the
BEST
system. At the core of the
PreDAC
system there is a high-speed 16-bit
digital to analog converter that uses dithering technique and active low-pass filtering
to obtain a stable high accuracy (21-bit) output signal.
This device is capable of outputing up to ±12 V bipolar voltage with an ultimate
resolution of 12
V – i.e. 21 bits on the bipolar full output range. Output voltage noise
is suppressed using a 4
th
order active low-pass filter with cut-off frequency (-3 dB) of
10 kHz. Its minimized temperature-induced drifts, good linearity and very low noise
levels enable users to perform high-precision voltage signal generation.
The standard
PreDAC
has two voltage output channels but can be optionally
upgraded to have three or even four output channels on a single unit. It is housed in a
light, robust and extremely compact metallic box that can be placed as close as
possible to the actuator power driver/amplifier in order to reduce cable lengths and
consequently minimize possible noise pick-up on the analog signal path. It is specially
suited for applications where multi-channel simultaneous actuations are required, a
typical application being control of position (X, Y) and intensity (I
0
) of the photon
beam in synchrotron radiation or XFEL X-ray beamlines.
The
PreDAC
communication to a host PC when used as a standalone unit is
guaranteed by a standard 10/100/1000 Mbps Ethernet TCP/IP protocol while its
integration in the
BEST
(Beamline Enhanced Stabilization Technology) system is
performed via the SFP link available on the rear panel.
The
PreDAC
unit and its I/O connections can be easily seen in
Figure 6
(front)
and in
Figure 7
(rear).
Output Channels
ON, CL and
STATUS LEDs