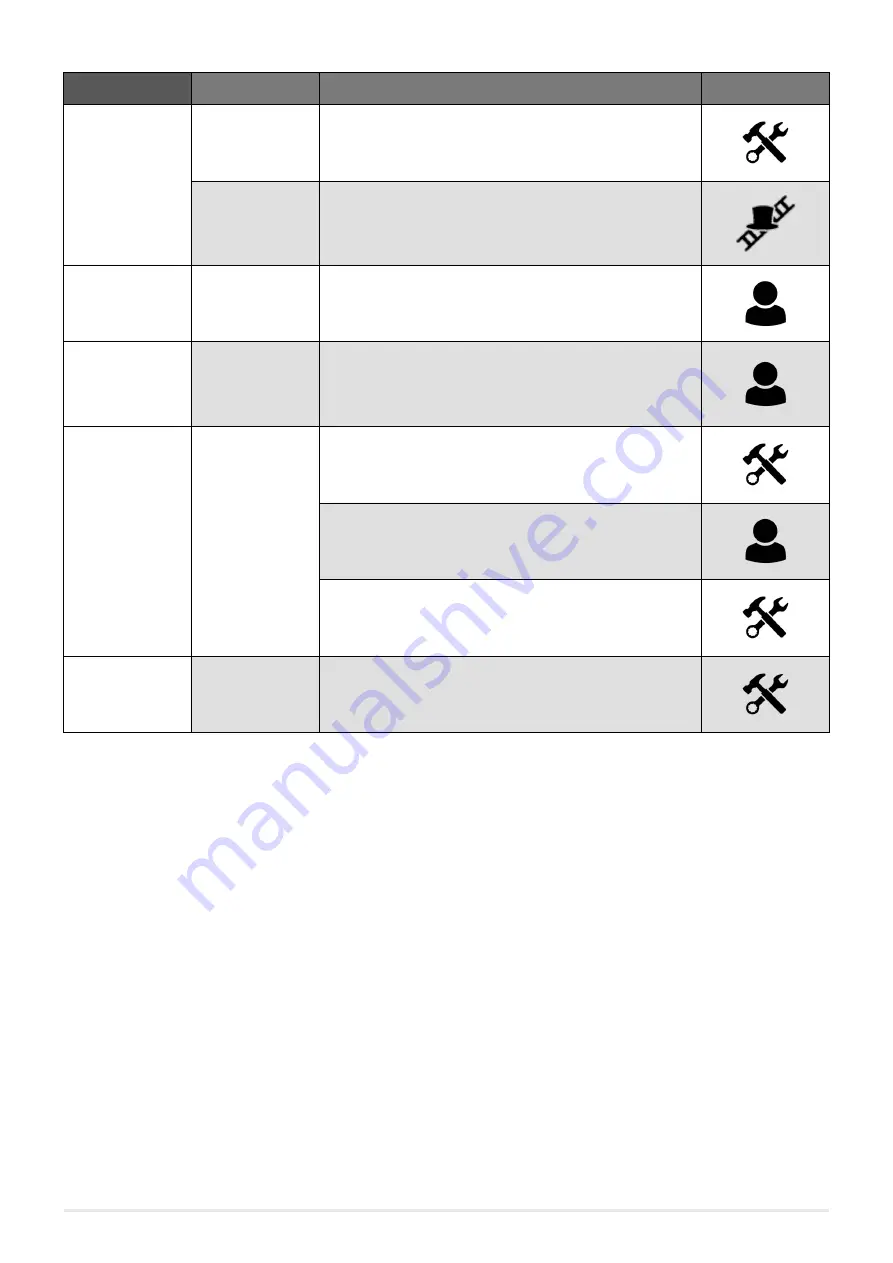
RIVER IDROTECH 18 - 24 - 24H2O
38
PROBLEM
CAUSE
SOLUTION
INTERVENTION
Ash remains along
the stove
Faulty or out of order
door gaskets
Replace the gaskets.
Not sealed fume
pipes
Contact an expert stove-repairer who will immediately provide for
sealing the junctions with high-temperature silicone and/or for
replacing pipes with those in compliance to current regulations. A
not sealed fume channelisation can be noxious to health.
The stove is at its
highest power but
does not heat up.
Ambient temperatu-
re reached.
The stove is at its minimum value. Increase the desired ambient
temperature.
Stove running and
display showing
"Smoke Overtepe-
rature"
Reached fume outlet
limit temperature
The stove runs at minimum. NO PROBLEM!
The stove's smoke
duct produces
condensation
Low smoke tempe-
rature
Check that the flue is not clogged.
Increase stove power to minimum (pellet drop and fan revs).
Install condensation collection cup.
Stove running and
display showing
"SERVICE"
Routine maintenan-
ce alert (it does not
block the system)
When this flashing message appears upon start-up, it means that
the preset operating hours have elapsed before maintenance.
Contact the service centre.