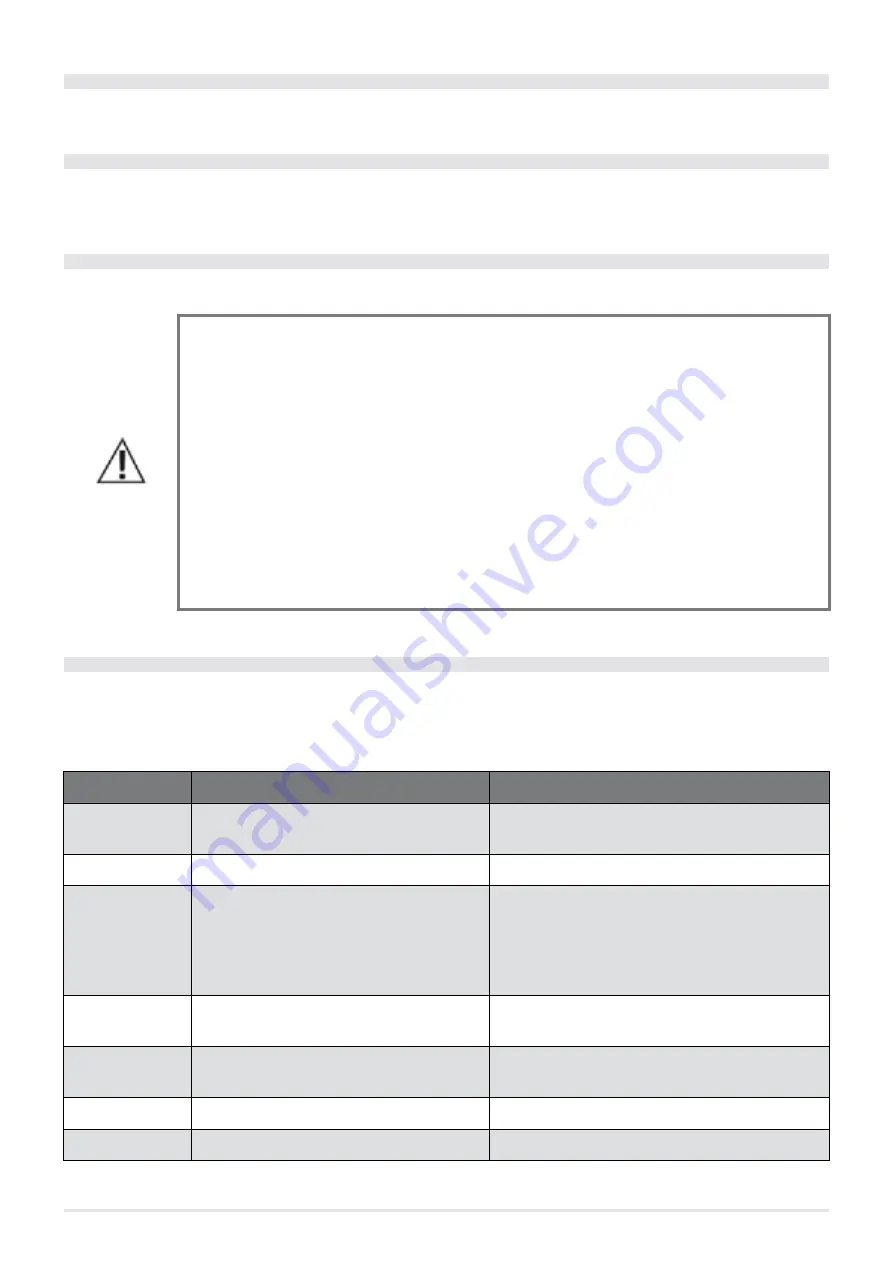
IDRO PRINCE
3
12-16-23-23 H
2
O - IDRO PRINCE 30-30 H
2
O - AQUOS
3
16-23-23 H
2
O - IDRON 16-22 AIRTIGHT - MIRA 16-22 - TESIS 16-23 AIRTIGHT - HIDROFIRE 22.8
57
12.11 FAILED START-UP
If during ignition no flame develops, the boiler will go into alarm condition.
12.12 ANTIFREEZE FUNCTION
If the probe in the boiler detects a water temperature of less than 5°C, the circulation pump is automatically activated to prevent
the system from freezing.
12.13 PUMP ANTI-SEIZURE FUNCTION
If the pump is not used for prolonged periods, it is activated periodically for a few seconds to prevent it from seizing up.
TAMPERING WITH THE SAFETY DEVICES IS PROHIBITED
If the product is NOT used as described in this instruction manual, the manufacturer declines all liability for
any damage caused to persons and property. The manufacturer furthermore refuses to accept responsibility
for damage to persons and property arising from the failure to observe all the rules contained in the manual
and in particular:
• All the necessary measures and/or precautions must be adopted when performing maintenance, cleaning
and repairs.
• Do not tamper with the safety devices.
• Do not remove the safety devices.
• Connect the product to an efficient smoke expulsion system.
• Verify that the room in which the appliance will be installed is adequately ventilated.
The product can be started-up and the automatic function of the probe restored only after having eliminated
the cause that triggered the safety system. This manual will help you understand which anomaly has occur-
red, and explain how to intervene according to the alarm message displayed on the appliance.
12.14 ALARM ALERTS
Whenever an operating condition other than that designed for the regular operation of the boiler occurs, there is an alarm condi-
tion.
The control panel gives information on the reason of the alarm in progress. A sound signal is not envisioned for alarms A01-A02
only so to PANEL ALERTnot disturb the user in the event of pellets running out in the hopper during the night.
PANEL ALERT
TYPE OF PROBLEM
SOLUTION
A01
The fire does not ignite.
Check whether the brazier is clean / level of pellets in
the hopper.
A02
The fire goes off abnormally.
Check the level of pellets in the hopper.
A03 Thermostat
alarms
The temperature of the pellets hopper or the
water temperature exceed the envisioned
safety threshold.
Wait for the cooling stage to end, cancel the alarm and
restart the boiler setting the fuel loading at minimum
(SETTINGS menu - Pellets recipe). If the alarm persists,
contact the service centre. Check if the room fan works
properly (if present).
A04
Smoke overheating.
The set smoke threshold has been exceeded. Reduce
pellets loading (SETTINGS menu - Pellets recipe).
A05 Pressure
switches alarm
Smoke pressure switch intervention or water
pressure insufficient.
Verify chimney obstruction / door opening or hydraulic
system pressure.
A08
Abnormal smoke fan operation.
If the alarm persists, contact the service centre.
A09
Smoke probe faulty.
If the alarm persists, contact the service centre.