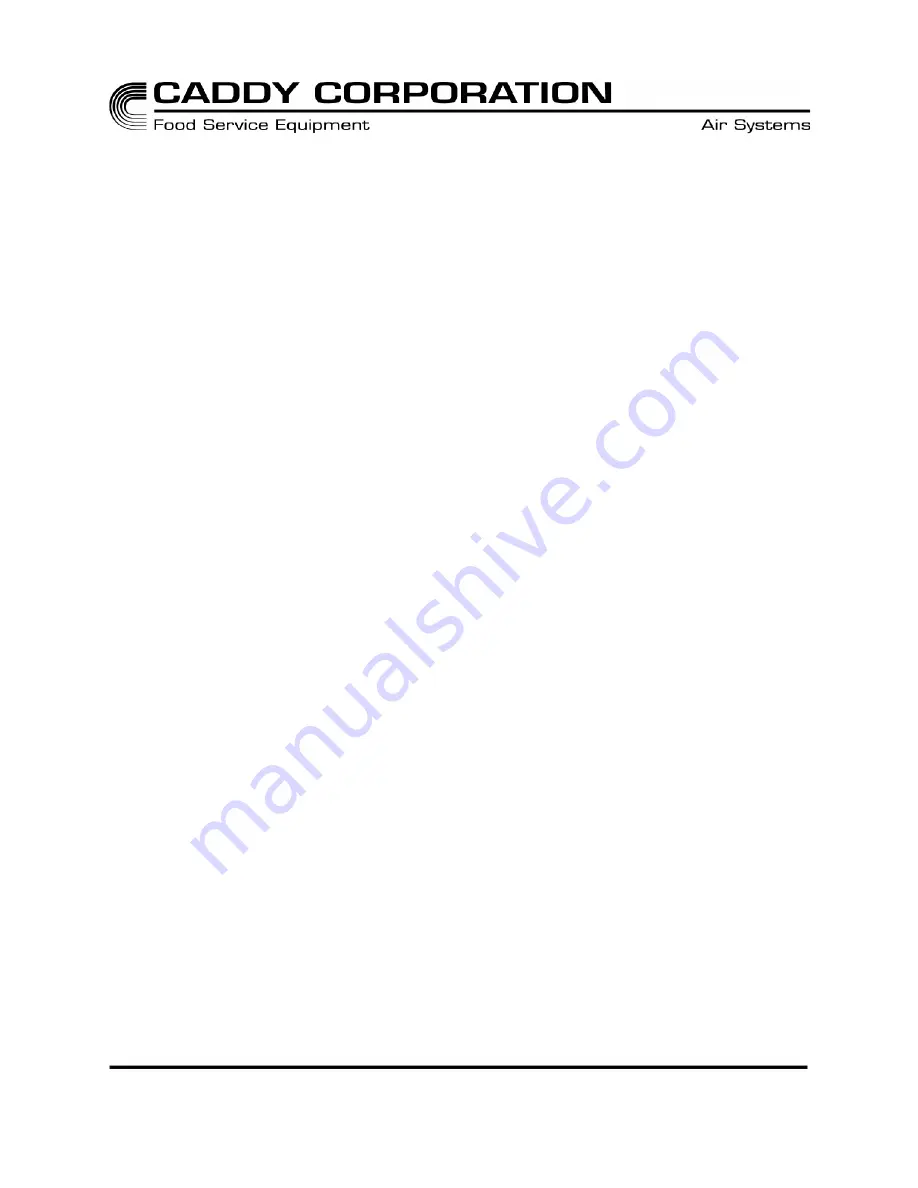
Page 18
509 Sharptown Road P.O. Box 345 Bridgeport, NJ 08014
Email: [email protected] Fax: 856-467-5511
Internet: http://caddycorp.com Phone: 856-467-4222
5.
Keep your food equipment clean.
Use alkaline, alkaline chlorinated or non-chloride cleaners at recommended strength. Clean frequently to
avoid build-up of hard, stubborn stains. If you boil water in stainless steel equipment, remember the single
most likely cause of damage is chlorides in the water. Heating cleaners that contain chlorides have a similar
effect.
6.
Rinse, rinse, rinse.
If chlorinated cleaners are used, rinse and wipe equipment and supplies dry immediately. The sooner
you wipe off standing water, especially when it contains cleaning agents, the better. After wiping
equipment down, allow it to air dry; oxygen helps maintain the stainless steel’s passivity film.
7.
Never use hydrochloric acid (muriatic acid) on stainless steel.
Review
Stainless steels rust when passivity (film-shield) breaks down as a result of scrapes, scratches,
deposits and chlorides.
Stainless steel rust starts with pits and cracks.
Use the proper tools. Do not use steel pads, wire brushes or scrapers to clean stainless steel.
Use non-chlorinated cleaners at recommended concentrations. Use only chloride-free cleaners.
Soften your water. Use filters and softeners whenever possible.
Wipe off cleaning agents and standing water as soon as possible. Prolonged contact eventually causes
problems.