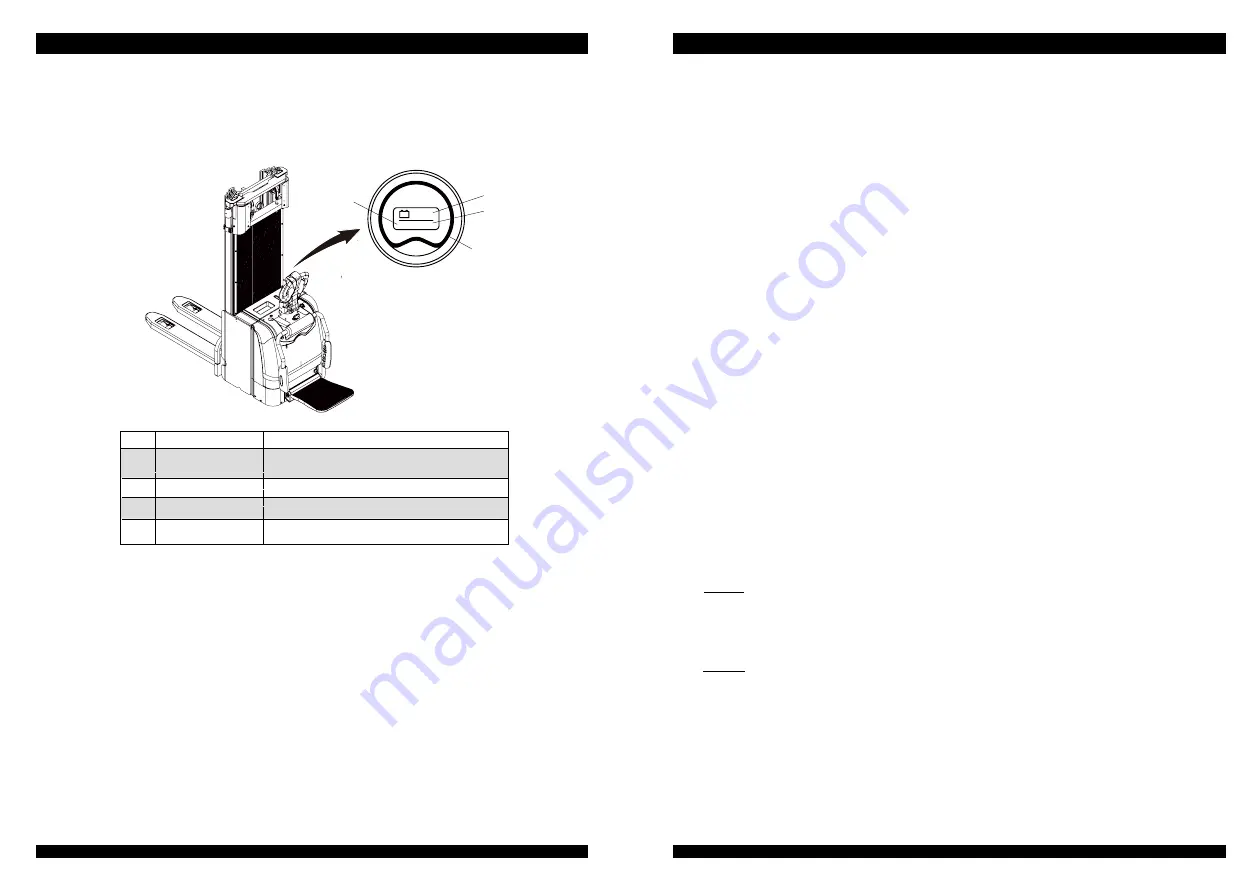
USER MANUAL
30
31
INSTRUMENT
(
TYPE B
)
There are a display screen and an instrument aperture on the instrument (Type B). The display
screen shows information such as power, service time and fault code.
When a controller is faulty,
the instrument aperture will be shown as red, and the interface displays the current fault code.
1
ALARM INDICATOR
WHEN THE BATTERY POWER IS LOW OR THE FORKLIFT IS
FAULTY,THE INSTRUMENT APERTURE WILL BE SHOWN AS RED,
AND THE INTERFACE DISPLAYS THE CURRENT FAULT CODE.
2
SPEED INDICATOR
IT WILL DISPLAY CURRENT RUNNING SPEED WHEN THE
FORKLIFT STARTS NORMALLY.
3
WORKING TIME INDICATOR
IT WILL DISPLAY TIME WORKED WHEN THE FORKLIFT STARTS
NORMALLY.
4
BATTERY STATE
THE BATTERY POWER IS SHOWN AS PERCENTAGE.
Υ
Τ
α
NPK K
OPERATION
EPS14Pi
NO.
NAME
DESCRIPTION
TRANSPORTING GOODS
LOADING
1. GOODS ON THE GROUND
(1)
Drive the car carefully towards the position where goods are placed, and start the
brake.
(2)
Put the fork on the ground.
(3)
Insert the fork exactly into the bottom of the goods.
(4)
Lift the fork.
(5)
Pay attention to the road condition and pedestrians when driving and keep an ap-
propriate forklift speed. Send goods to an assigned place.
2. ELEVATED GOOD
(1)
Move the forklift towards the goods-storing position carefully and start braking.
(2)
Keep mast vertical and lift the fork to the bottom of goods.
(3)
Insert the fork into the bottom of goods perfectly.
(4)
Continue to lift the fork and take out goods completely.
(5)
Drive backwards carefully and slowly and takes goods completely out of the stacking
area.
(6)
Lower the fork to a certain height.
(7)
Pay attention to the road conditions and pedestrians in the process of transportation,
and maintain an appropriate speed. Then send goods to a assigned place.
(1)
K
eep an appropriate speed when approaching to goods in order to avoid collision.
(2)
Do not stay below the lifting goods.
When loading goods, the shipper s72hall be responsible for fastening goods safely,
ensuring that goods are compact, the center of gravity is in the center of goods.
Danger
Caution
OM-
EPS14Pi
2019001-EN