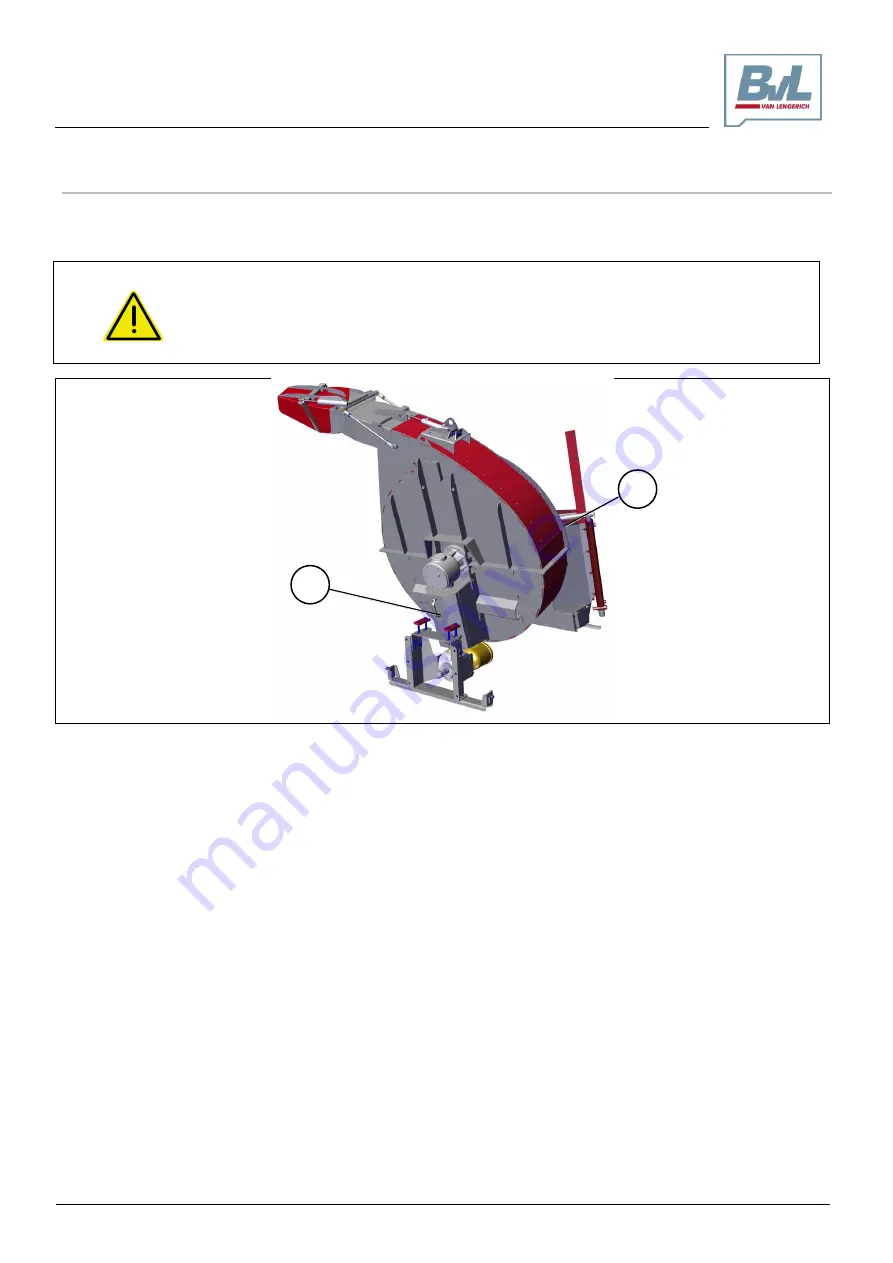
Design and function
Translation of the Original Operating Manual
27
4.2
Safety devices and guards
This chapter provides an overview of the safety devices and guards and the arrangement of the correctly
installed guards in the safety position.
WARNING
Risks of personal injury from crushing, entanglement and catching may arise when
moving parts of the machine are unprotected during operation!
Do not put the machine into operation unless the guards are installed completely.
Replace defective guards immediately with new ones.
Fig. 4-8 V-Comfort Turbo Plus
(1)
Protective hood
(2)
Rubber guard
1
2