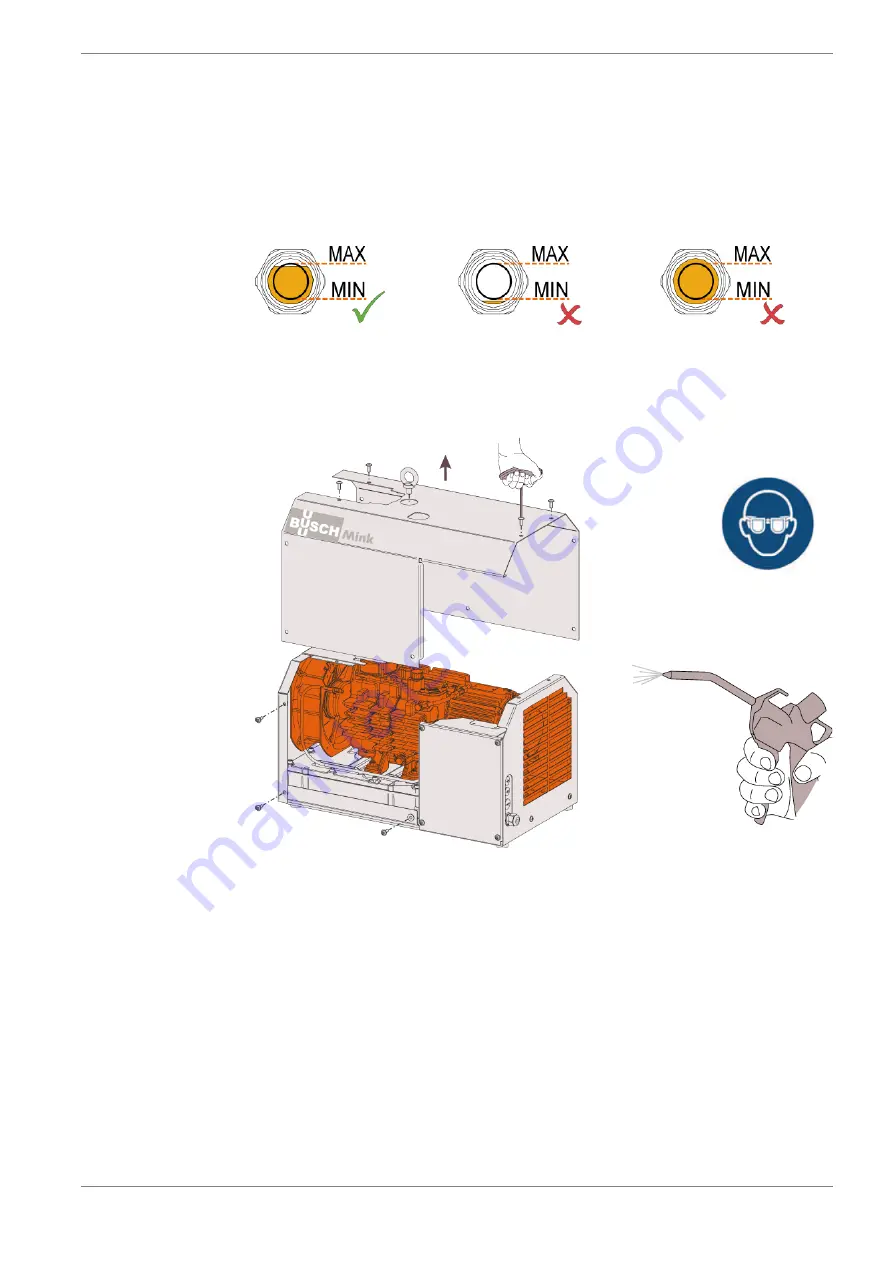
8 | Maintenance
0870S03254
_VO 0040-0080_B_-0000_IM_en
27
/ 52
8.2
34B
Check oil level
Proceed as follows:
•
Switch off the vacuum system.
•
Wait 1 minute after switching off the vacuum pumps, before checking the oil level.
The oil level should be constant over the entire service life. If the oil level drops, the gear box
is leaking and the vacuum pump needs to be repaired.
Top up with oil if necessary (chap. 0).
8.3
35B
Clean vacuum system from dust and dirt
Fig. 15:
Clean vacuum pump
Clean fan grids
and cooling fins
Summary of Contents for SIMPLEX VO 0040 B
Page 2: ...2 52 0870S03254_VO 0040 0080_B_ 0000_IM_en ...
Page 50: ...50 52 0870S03254_VO 0040 0080_B_ 0000_IM_en ...
Page 51: ...Notes ...