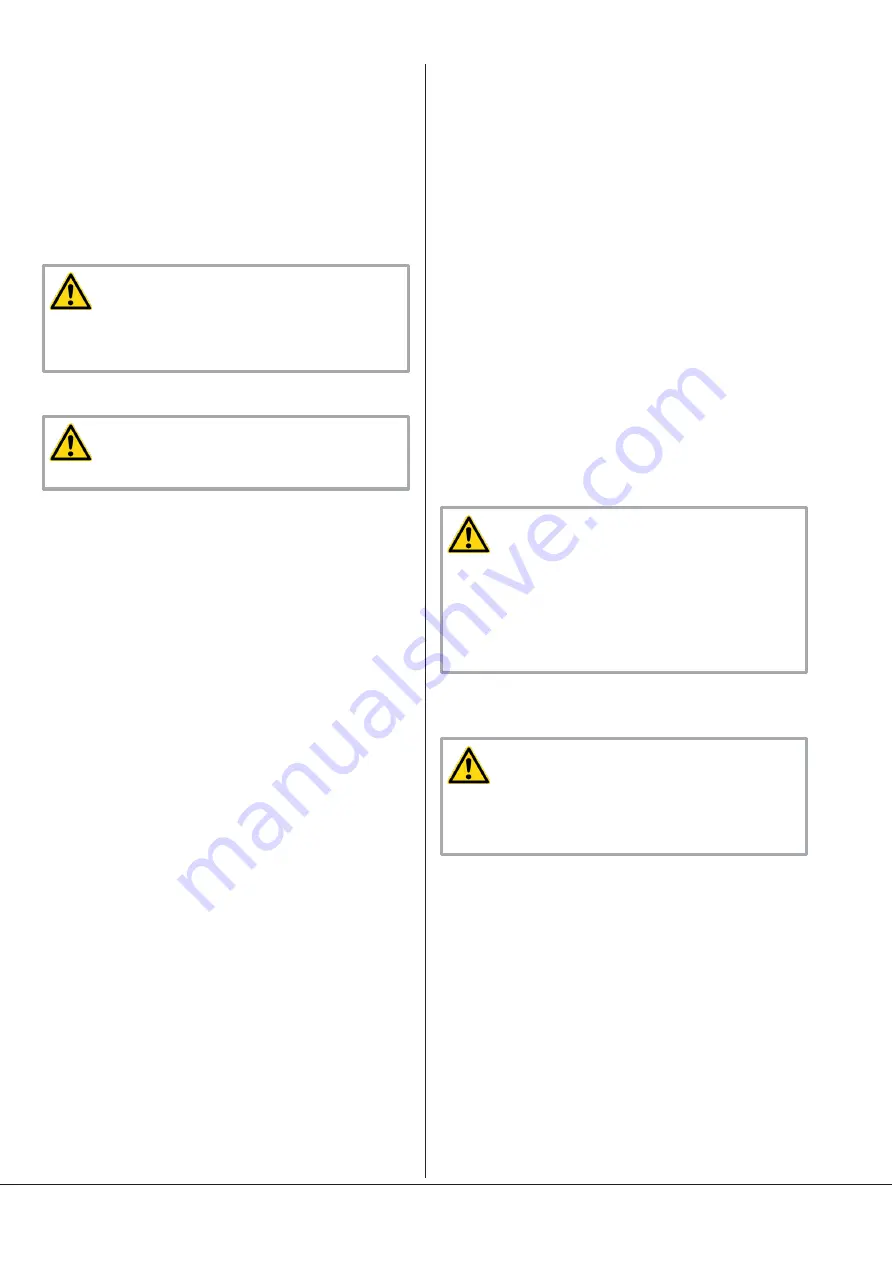
WY (MB) rotary lobes vacuum pump
Make sure that the oil level still lies in the target circle of the oil
sight glasses
If the oil level is below the target circle :
Fill in more oil into the two vacuum pumps If
the intake line is equipped with a shut-off device:
Open the shut-off device
If the intake line is not equipped with a shut-off device:
Remove the rubber plate from the intake flange and connect
the intake line to the intake flange
CAUTION
In the case of a vacuum pump filled with oil, you ensure that the
angle of inclination of the vacuum pump at the time of rise does not
exceed 5° compared to the horizontal. In the event of too important
slope (> 5°), risk of oil leakage in the workspace.
Before each transport requiring a means of adapted lifting, control
the slope of the vacuum pump (< 5°).
CAUTION
The vacuum pump must remain in a horizontal position when it has
been filled with oil.
Filling in cooling liquid
The COBRA DS vacuum pumps are generally dispatched with cooling
liquid already in the vacuum pump. Before vacuum pump first startup,
control the cooling liquid level. In the event of absence of this lubri-
cant, please carry out the filling (see the chapter “Cooling liquid types
” for information on the recommended cooling liquids).
Prepare the quantity of cooling liquid specified in the table
“Cooling liquid quantity”
NOTE
: The quantity of cooling liquid specified in the installation hand-
book is of informative nature only. Respect the procedure of filling the
cooling liquid.
Unscrew filler cap (CLF) of cooling liquid on cylinder upper plate
Open purge cap (CLV) on cylinder upper plate and purge cap
(CLV) on cylinder endplate B-side
Fill in by filler hole until cooling liquid flows by purge cap on
cylinder endplate B-side
Stop filling in cooling liquid
Close the purge cap on cylinder endplate B-side
Fill in again by filler hole until cooling liquid flows by purge cap of
cylinder upper plate
Close the purge cap of cylinder upper plate
Screw on the filler cap for the cooling liquid again
If liquid has run on to the outside surfaces of the vacuum pump,
wipe it off
Start the vacuum pump
If the intake line is equipped with a shut-off device:
Close the shut-off device
If the intake line is not equipped with a shut-off device:
Place a rubber plate on the intake flange
Let the vacuum pump run for a few minutes
Stop the vacuum pump and wait a few minutes
Unscrew purge cap on cylinder upper plate
Control that cooling liquid level is just under cylinder upper plate
In case cooling liquid level is below required level:
Fill in more cooling liquid
If the intake line is equipped with a shut-off device:
Open the shut-off device
If the intake line is not equipped with a shut-off device:
Remove the rubber plate from the intake flange and connect the
intake line to the intake flange
Checking the direct cooling
The flow of the cooling water is checked by the flow switch FS 2. The
flowmeter must be connected in such a way that switching-on leads to
an alarm and stopping of the vacuum pump when the flow drops be-
low 9 l/min.
Checking the nitrogen supply
The flow of the nitrogen is checked by the flowmeter FME. The flow-
meter must be connected in such a way that switching-on leads to an
alarm. The alarm limit can be adjusted depending the type of process.
Saving the operating parameters
As soon as the vacuum pump is working under normal conditions after
being switched on:
Measure the working current of the DP and MB motors and save
them as reference values for all future maintenance and repair
work
Recommendations on operation
Application
WARNING
The vacuum pump is designed for use under the conditions
specified here.
If these conditions are not met, there is a risk of damage to or total
destruction of the vacuum pump and its components!
The vacuum pump may only be switched on under the specified
conditions.
The COBRA DS vacuum pumps are designed for use in the field of mi-
croelectronics and similar industries.
They can be used to suck gases and gas mixtures.
WARNING
When using toxic, inflammable and/or explosive gases, make sure
that the system corresponds in design to applicable local and nation
al safety regulations and that all applicable safety measuresare
followed.
All product-specific safety regulations must be observed.
Solid particles must not get into the vacuum pump. Procedural errors
can result in the pump drawing in a certain quantity of liquid. If the
pump has drawn in liquid, a short drying time is necessary at the end of
the procedure.
The allowed maximum inlet gas temperature depends on the inlet pres-
sure and the type of gas: the lower the inlet pressure (Pa), the higher
the drawn gas temperature (TGas) can be.
The following indicative values for air can be considered:
– Pa > 50 mbar, TGas < 80°C
– Pa < 50 mbar, TGas < 200°C
The vacuum pump is intended for use in a potentially non-explosive
environment.
Max. permissible number of startings per hour: 6.
As far as temperature is concerned, the pump is suitable for continuous
duty at any pressure between atmosphere and ultimate pressure.
The vacuum pump is tight down to ultimate pressure.
Installation and start-up
Page 14
DS 8161 F
0870235853
(En)
Summary of Contents for COMBI COBRA DP 600 C
Page 26: ...Note...
Page 27: ...Note...