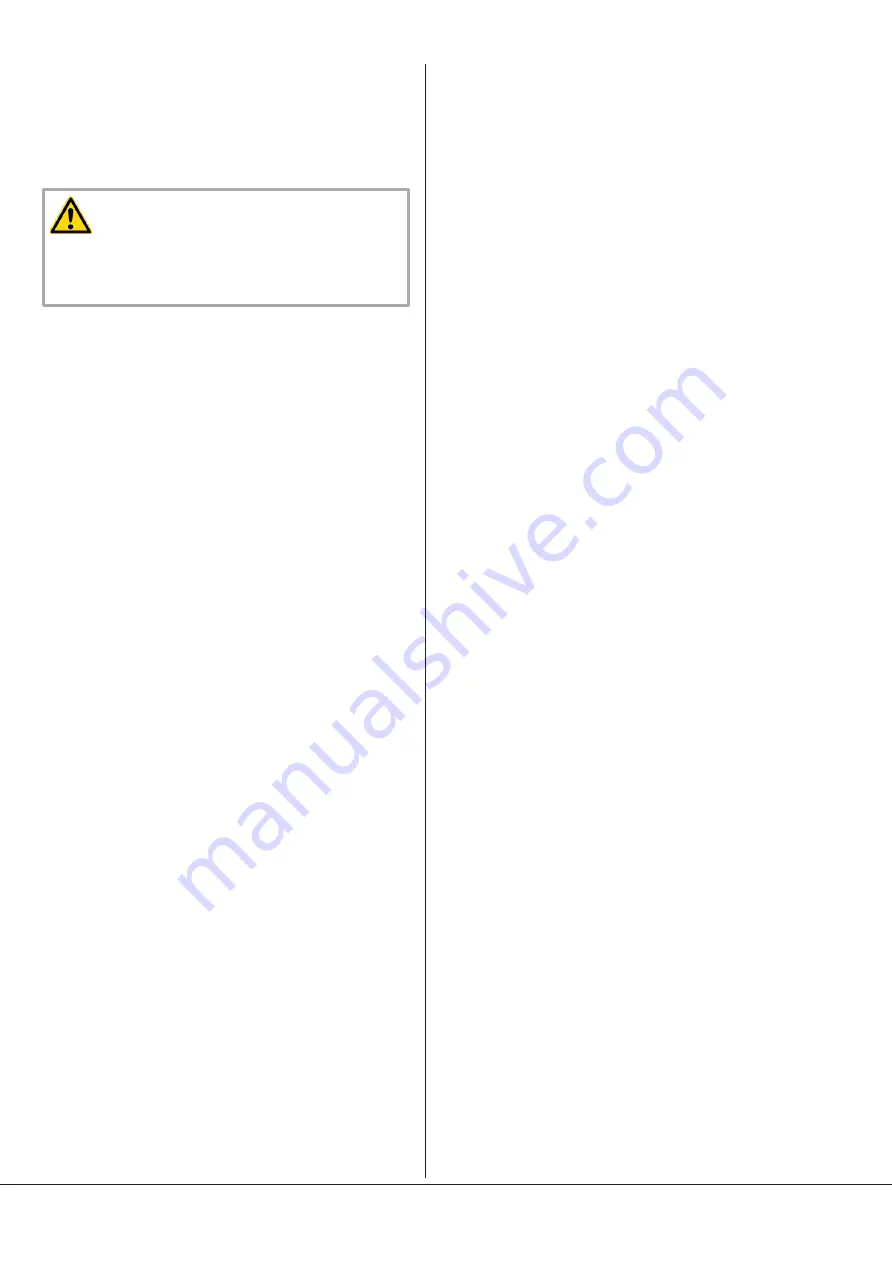
Product description
Use
The COBRA DS vacuum pumps are designed for use in the field of mi-
croelectronics and similar industries.
They can be used to draw in gases and gas mixtures.
WARNING
When using toxic, inflammable and/ or explosive gases, make sure
that the system corresponds in design to applicable local and
national safety regulations and that all applicable safety measures
are followed.
All product-specific safety regulations must be observed.
Solid particles must not get into the vacuum pump. Procedural errors
can result in the pump drawing in a certain quantity of liquid. If the
pump has drawn in liquid, a short drying time is necessary at the end of
the procedure.
The allowed maximum inlet gas temperature depends on the inlet pres-
sure and the type of gas: the lower the inlet pressure (Pa), the higher
the drawn gas temperature (TGas) can be.
The following indicative values for air can be considered:
– Pa > 50 mbar, TGas < 80°C
– Pa < 50 mbar, TGas < 200°C
The vacuum pump is intended for use in a potentially non-explosive
environment.
Max. permissible number of startings per hour: 6.
As far as temperature is concerned, the pump is suitable for continuous
duty at any pressure between atmosphere and ultimate pressure.
The vacuum pump is tight down to ultimate pressure.
Operating principle
The COBRA DS vacuum pumps are a combination of a COBRA NS
0600 C (DP) vacuum pump with cooling water and nitrogen circuits
and a WY8000 A (MB) rotary lobes vacuum pump.
The COBRA NS vacuum pumps work by the principle of screw pumps.
Two parallel screws (8) rotate in opposite directions in the pump body.
Entering gases are trapped between the flights of the screws and the
pump body. The gases are conveyed by the rotation of the screws to
the exhaust, where they are discharged.
The COBRA NS vacuum pumps are driven by water-cooled motors.
The WY rotary lobes vacuum pumps operate according to the appro-
ved principle of the Roots type machine. Operation is both simple and
effective. Two lobes rotors (11) with identical profiles rotate in opposite
directions within a casing. As they rotate, gas is drawn into the space
between each rotor and the casing where it is trapped and by the rota-
tion pushed out into the discharge. This action is repeated twice for
each revolution of each rotor and therefore four times for each revolu-
tion of the drive shaft. There is no mechanical contact between rotors
and cylinder. So no oil lubrication is required.
The WY rotary lobes vacuum pumps are driven by water-cooled
motors.
The WY rotary lobes vacuum pumps are equipped with an automatic
by-pass valve that limits the differential pressure between inlet and
outlet.
Oil circuit
Since the complete operating principle works without contact, no oil
circuit is needed in the work area.
Cooling
The COBRA DS vacuum pump is cooled by
–
the filling of cooling liquid (mix of water and glycol) inside the
water chambers (6) of cylinder and end plate of cylinder B-side. An
indirect circuit is made with a water pump mounted at the
endplate of cylinder B-side. The flow of the cooling liquid is
controlled by a flow switch FS 1. If the flow is under 1 l/min during
a minimum time of 30 seconds, then the pump stops.
The temperature regulator TS 2 will give an emergency signal if the
temperature of the cooling liquid is above 100°C. The pump will
stop immediately after the emergency alarm ring.
–
a direct cooling water circuit in the motors in the cylinder covers A
and B side of WY rotary lobes vacuum pump and COBRA NS
vacuum pump. The cooling water flow is preset at 10 Nl/min at
the factory and can be adjusted with regulating valve CWV. The
flow is controlled by flow switch FS 2. The cooling water circuit
stabilizes the temperature of cooling liquid. When flow is too low a
warning then an alarm signal is generated by flowmeter CWM to
the PLC. Status of the pump depends on the alarm function set by
user (factory setting: E
SS
, pump stops after alarm condition)
NOTE
: The COBRA DS vacuum pumps are generally dispatched with
oil and cooling liquid already in the vacuum pump but, without cooling
water. Before vacuum pump first startup, control the oil level and the
cooling liquid level. In the event of absence of one or the other of
these lubricants, please carry out the filling (please refer to the various
chapters of filling). Do not forget to connect the cooling water supply
before the first startup. Operation without these coolants can result in
damage to the vacuum pump.
Nitrogen system
The nitrogen system performs two main functions
–
nitrogen is used as dilution gas. It is injected inside the cylinder on
two ports. Nitrogen flow injected in the middle hole (8) is preset at
40 Nl/min and can be adjusted with valve DGR 2, depending on
the application. Nitrogen flow injected in the hole on cylinder
endplate side (9) is preset at 20 Nl/min and can be adjusted with
valve DGR 1, depending on the application. When flow is too low
a warning then an alarm signal is generated by flowmeter FME to
the PLC. Status of the pump depends on the alarm function set by
user (factory setting : None, pump continues running with an
alarm). Dilution improves the screws functioning, especially when
drawing in corrosive gases.
–
the nitrogen is used as sealing gas. The nitrogen is injected into the
intermediate chamber (5) in the cover of the cylinder of the NS
pump to achieve good closeness.
Optional functions/ Use of available
accessories
The relief valve (SV) prevents excessively high pressure in the expan-
sion tank (EV), relief pressure: 6 bar.
A pressure switch (optional) with normally closed contact mounted in
the expansion tank monitors the pressure of the cooling liquid. It must
be connected in such a way that actuation causes the vacuum pump to
be switched off when the pressure exceeds a value of 3 bar.
A pressure switch mounted at the exhaust, controls the overpressure at
the exhaust. If overpressure is above 0,2 bar, pressure switch gives a
warning then an alarm signal. Status of the pump depends on the alarm
function set by user (factory setting: None, pump continues running
with an alarm).
A temperature sensor PT100 (10) mounted on the cylinder, measures
the temperature inside the cylinder.
A silencer or sound absorber (accessory) at the exhaust reduces the
noise of the pump and collects any condensate.
A leak-protection non-return valve (optional) at the exhaust traps the
condensate in the pump when the pump is switched off.
The nitrogen can also be used as flushing gas. Depending on the appli-
cation, flushing is recommended after every use to ensure troublefree
operation of the vacuum pump. The nitrogen is injected directly into
the intake port. In the absence of nitrogen flushing can also be perfor-
med with the help of air.
Product description
Page 6
DS 8161 F
0870235853
(En)
Summary of Contents for COMBI COBRA DP 600 C
Page 26: ...Note...
Page 27: ...Note...