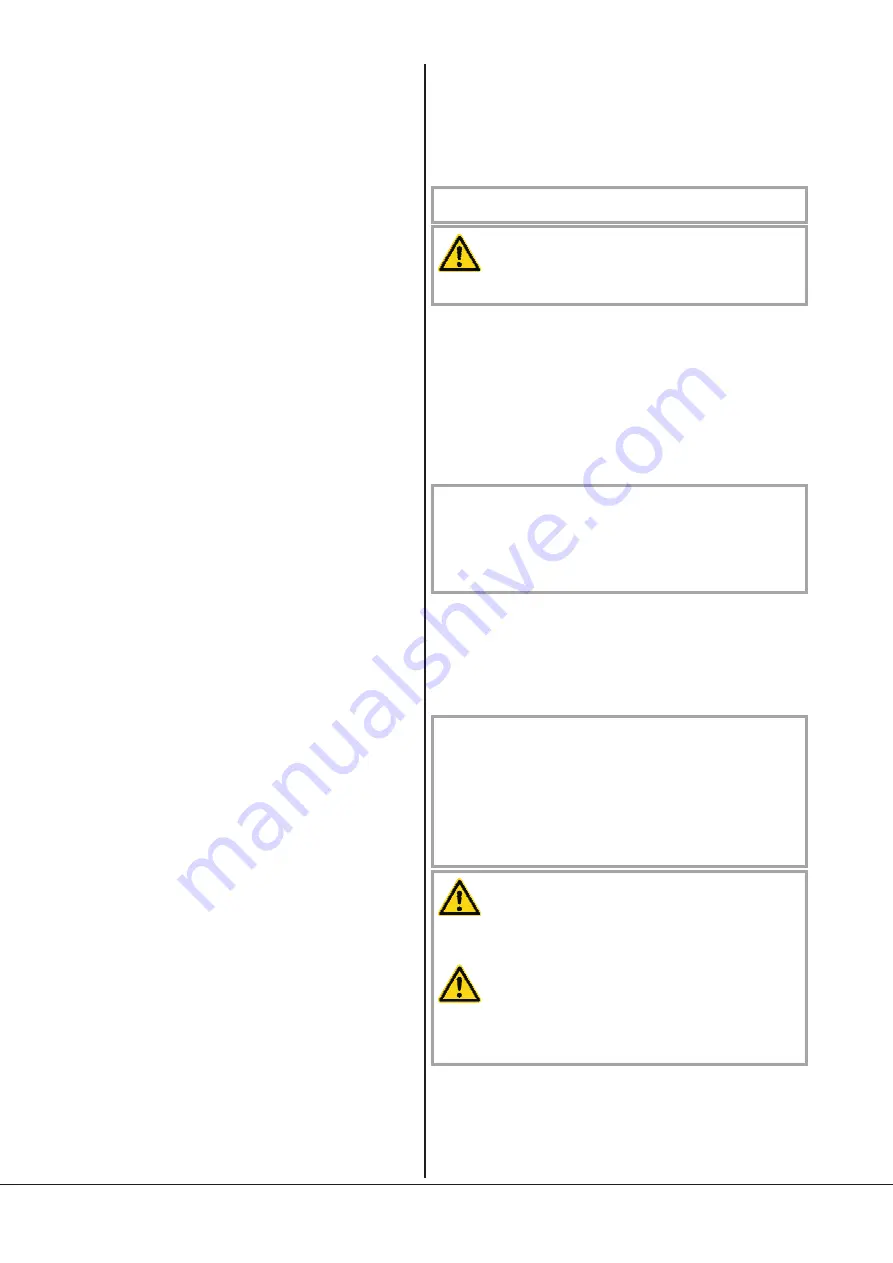
–
Drain the cooling water
u
Pull off the connections for the inlet and outlet of the cooling
water
u
Drain the cooling water completely
u
If necessary, drain the cooling water with the help of
compressed air to prevent any risk of frost or corrosion
NOTE
: When the pump has not been in operation for a few days or
when a sticky substance has been drawn in, it is possible that the two
screw rotors of the NS (DP) vacuum pump will stick to each other. Screw
open the access cover to the screw rotors. Loosen the rotors from each
other with the help of an Allan key by turning them in clockwise direc-
tion by hand.
Switching the vacuum pump on/ off
First start-up of the system
l
Make sure that the “Necessary installation instructions” are followed
If the system is equipped with a solenoid gate valve (customer option) in
the cooling water circuit:
u
Open the solenoid gate valve
l
Make sure that the cooling water flow is set correctly
–
The cooling water flow is factory set on 10 Nl/min and can be
adjusted at the regulating cock CWV. This water circuit is used to
cool the motor of the DP and MB vacuum pumps.
l
Make sure that the nitrogen flow is set correctly
–
Nitrogen flow injected in the middle hole (8) is preset at 40 Nl/min
and can be adjusted with valve DGR 2. Nitrogen flow injected in the
hole on cylinder end-plate side (9) is preset at 20 Nl/min and can be
adjusted with valve DGR 1.
l
Switch on the vacuum pump
l
Make sure that the system does not leak
If the system is equipped with a solenoid gate valve at the intake:
u
Open the solenoid gate valve
Switching the system off
If the system is equipped with a solenoid gate valve at the intake:
u
Close the solenoid gate valve
l
Switch off the vacuum pump
l
Shut off the nitrogen supply
l
Shut off the cooling water supply
If the system is equipped with a solenoid gate valve (customer option) in
the cooling water circuit:
u
Close the solenoid gate valve
l
Make sure that the system is electrically isolated
Description of the Load Lock operation
mode:
l
LL Mode = Off
u
The mode « Load Lock » is de-activated, the module DP and the
module MB, when present, operate constantly at their maximum
frequency of rotation.
NOTE:
the parameters « DP (or MB) Current Level », « Time Before »
and « DP Idle » are idle.
CAUTION
LL Mode = Off is not recommended for Load Lock cyclic pumping
due to the current load and the mechanical stress with full speed.
l
LL Mode = Auto
u
The mode Load Lock is activated and de-activated according to
the current load taken in by the module DP (or MB). The current
threshold is adjustable using the parameters « DP/MB Current
Level ». When the current level exceeds the threshold, the
modules DP and MB accelerate to their maximum frequency of
rotation. When the current level drops below the threshold, a
time delay which is adjustable in its duration using the parameter
« Time Before », will start. As soon as the time
delay's duration has elapsed, the modules DP and MB slow
down to their minimum frequency of rotation.
NOTE:
-
If the parameter « DP Idle » is configured to « Disable », the module
DP runs constantly at maximum frequency of rotation.
-
If the module is not controlled by a frequency inverter, module MB
is started if the current level exceeds the threshold and is stopped if
the current level drops below the threshold and if the time delay's
duration has elapsed.
l
LL Mode = External
u
The Load Lock mode is activated and de-activated depending on
the digital input status « Remote Process On » which is available
on the tool interface. When the input changes to status 1, the
modules DP and MB accelerate to their maximum frequency of
rotation. When the input changes to status 0, the modules DP
and MB slow down to their minimum frequency of rotation.
NOTE:
- When the parameter « DP Idle » is configured to « Disable », the
module DP runs constantly at the maximum frequency of rotation.
- The parameters « DP (or MB) Current Level » and « Time Before »
are idle.
- Refer to chapter « Description of MENU 08 TOOL INTERFACE » for
the configuration of the input « Remote Process On ».
- If the module MB is not controlled by a frequency inverter, module
MB is started if the input changes to status 1 and is stopped if the
input changes to status 0.
CAUTION
The mode « Load Lock » will not work when:
- The warming up cycle has not finished.
- The mode maintenance is activated.
CAUTION
- Be careful to set « Current level » and « Time Before » parameters
regarding process cycle time and chamber size to be sure module MB
is stopped or running idle speed before opening inlet valve.
- Be careful to change input status to 0 before opening inlet valve.
Installation and start-up
DS 3010 E
Page 16
0870771509 (En)