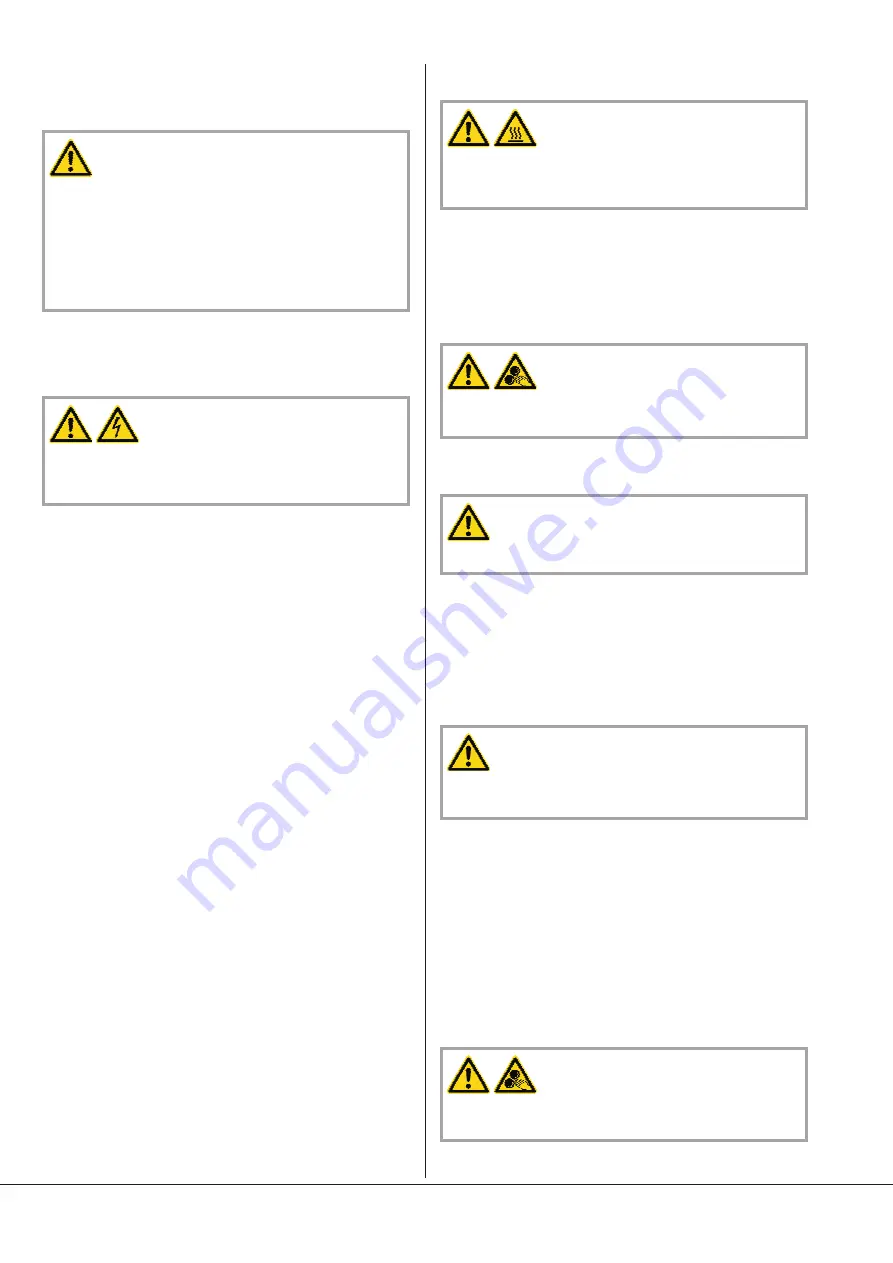
Installation and start-up
Necessary installation instructions
CAUTION
If the necessary installation instructions are not followed and
particularly in the case of inadequate cooling:
Risk of damage to and total destruction of the vacuum pump and its
components!
Risk of personal injury!
The necessary installation instructions must be followed.
l
Make sure that the integration of the vacuum pump in its new
environment complies with the safety regulations according to the
Machinery Directive 2006/42/EC (regarding the responsibility of
the manufacturer of the system in which the vacuum pump is to be
integrated, see information in the Declaration of Conformity).
WARNING
Local regulations regarding the motors and electric control
elements must be observed when installing the pump in potentially
explosive environments. Make sure before start-up that all safety
measures have been followed.
Installation site and installation
l
Make sure that the environment of the vacuum pump is not
potentially explosive
l
Make sure that the following ambient conditions are fulfilled:
–
Ambient temperature: 0 ... 40 °C (32 ... 104 °F)
–
Ambient pressure: atmosphere
–
Humidity range: 20 to 95%
–
Altitude: up to 1000 m
l
Make sure that the cooling water fulfills the following
requirements:
–
Temperature: 10 - 25 °C
–
Water pressure: 2 - 5 bar (relative)
–
Approximative flow rate: min. 10 l/min for the standard version
–
Water hardness: < 5° dGH
NOTE:
1° (german degree = 1° dGH) = 1,78° (french degree) = 1,25 e
(english degree) = 17,9 mg/kg CaCO3 (american hardness)
l
Make sure that the cooling water is neutral and clean
l
Make sure that the cooling water outlet is unpressurised
–
Overpressure: 1,5 bar
–
Standard flow rate dil 1: 20 l/min
–
Standard flow rate dil 2: 40 l/min
–
Max. flow rate: 200 Nl/ min
l
Make sure that the ambient conditions correspond to the
protection class of the motor (according to nameplate)
l
Make sure that the vacuum pump is placed on or fastened to a
horizontal surface
l
Make sure that the vacuum pump is level
l
Make sure that the vacuum pump is at least 1 m away from any
wall to ensure good cooling
l
Make sure that the vacuum pump is easily accessible and that the
selected installation site fulfills the requirements for assembly/
dismantling
l
Make sure that no temperature-sensitive parts (for example, of
plastic, wood, cardboard, paper, electronic parts) come into
contact with the hot surfaces of the vacuum pump
l
Make sure that the installation site or assembly area is ventilated in
such a way that adequate cooling of the vacuum pump is ensured
CAUTION
The surface temperature of the vacuum pump can exceed 50°C
when the vacuum pump is in operation.
Danger of burns!
l
Make sure that no-one can touch the vacuum pump accidentally.
If necessary, attach safeguard
l
Make sure that the oil sight glasses are easily accessible
If oil changes are to be made on site:
u
Make sure that the oil drain and oil filler are easily accessible
Inlet connection
CAUTION
Do not put hands into the inlet aperture.
Risk of body damage!
l
Make sure that the protection that was attached to prevent
penetration of particles during transport has been removed before
the vacuum pump is connected to the vacuum line
CAUTION
The intake of liquids or solid particles can lead to the destruction of
the vacuum pump
If the drawn gas contains dusts or solid foreign bodies:
u
Make sure that a filter or protective grating is installed at the
extraction point
l
Make sure that the nominal diameter of the intake line is at least
equal to the diameter of the intake flange of the vacuum pump to
prevent a drop in the performance of the vacuum pump in the case
of a smaller cross-section
l
Make sure that the vacuum pump is connected with leakproof lines
CAUTION
When the intake lines have been connected, make sure that the
system does not leak. Leakages of dangerous substances must be
prevented!
l
Make sure that the intake lines are equipped with a shut-off device
upstream of the intake flange so that the flow of drawn gas can be
stopped
l
Make sure that the intake lines do not exercise any force on the
intake flange. Mount bellows if necessary
l
The inlet flange has the following dimension:
–
DN 160 ISO-K
In the case of long intake lines, the line cross-section should be larger
than the intake flange to prevent a drop in the performance of the va-
cuum pump. If you have any doubts, contact your Busch representa-
tive.
Discharge connection
CAUTION
Do not put hands into the outlet aperture.
Risk of body damage!
Installation and start-up
DS 3010 E
Page 10
0870771509 (En)