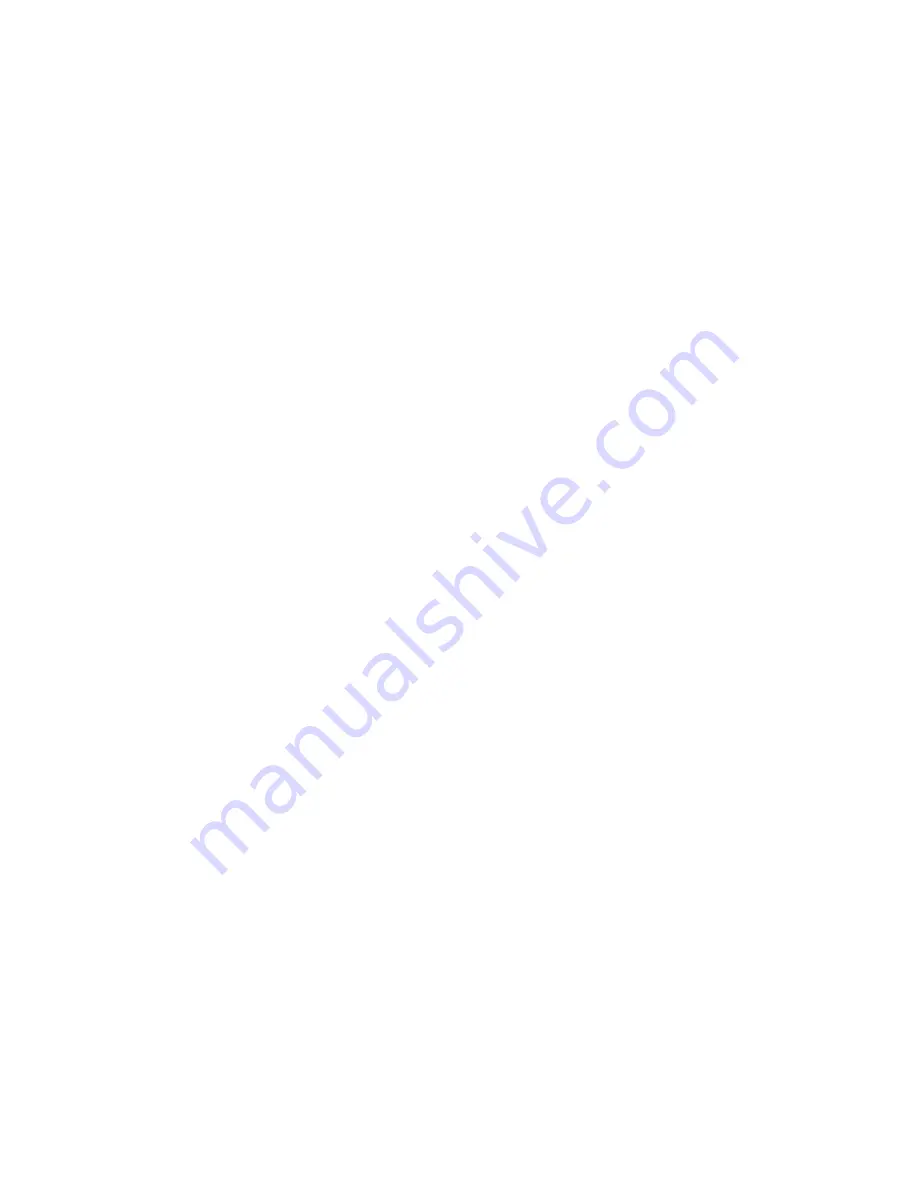
21
i.
Fitting leaks due to misflared tubing or
damaged fitting.
ii.
Fuel line leak due to crushed or bent tubing.
iii. Filter connection leaks.
iv. Tank connection leaks.
The following actions can eliminate air leaks:
i.
Bleed pump as detailed in System Start-Up
Section of this manual.
ii.
Replace flare fittings.
iii. Replace oil supply line.
iv. Repair oil filter leaks
v.
Replace or repair tank fittings.
e. GASKET LEAKS— If 11.5% to 12.5% CO
2
with a #1 smoke cannot be obtained in stack,
look for air leaks around the canopy seal. Such
air leaks will cause a lower CO
2
reading in the
stack. The smaller the firing rate the greater
effect an air leak can have on CO
2
readings.
f. DIRT— A fuel filter is a good investment.
Accidental accumulation of dirt in the fuel
system can clog the nozzle strainer and produce
a poor spray pattern from the nozzle.
g. WATER— Water in the fuel, in large amounts,
will stall the fuel pump. Water in the fuel
pump, in smaller amounts, will cause excessive
wear on the pump, but more importantly water
does not burn. It chills the flame, causes smoke,
and allows unburned fuel to pass through the
combustion chamber and clog the flueways of
the boiler.
h. COLD OIL— If the oil temperature approaching
the fuel pump is 40°F or lower, poor combustion
or delayed ignition may result. Cold oil is harder
to atomize at the nozzle. Thus, the spray droplets
get larger and the flame shape gets longer. An
outside fuel tank that is above grade or has fuel
lines buried in the ground above the frost line is a
good candidate for cold oil. The best solution is
to place the tank and oil lines in the ground
below the frost line.
i.
HIGH ALTITUDE INSTALLATIONS
Typically, the rule to use for high altitudes is to
increase the air supply by 4% per each 1000 ft.
above 2000 ft. altitude from sea level. This
means that the air setting will have to be higher
than the calibration marks in proportion to the
altitude. Use instruments and set for 11.5 to
12.5% CO
2
.
j.
START-UP NOISE — Late ignition is the cause
of start-up noises. If it occurs recheck for
electrode settings, flame shape, air or water in the
fuel lines.
k. SHUT DOWN NOISE — If the flame runs out of
air before it runs out of fuel, an after burn with
noise may occur. That may be the result of a
faulty cut-off valve in the fuel pump, or it may be
air trapped in the nozzle line. It may take several
firing cycles for that air to be fully vented
through the nozzle. Water in the fuel or poor
flame shape can also cause shut down noises.
P
.
TEST CONTROLS
1. CHECK THERMOSTAT OPERATION. Raise and
lower thermostat setting as required to start and
stop burner.
2. VERIFY PRIMARY CONTROL SAFETY FEA-
TURES using procedures outlined in Instructions
furnished with control (See back of Control Cover)
or Instructions as follows:
a. Simulate flame failure:
•
Follow the starting procedure to turn on the
burner.
•
Close the hand valve in the oil supply line.
•
Safety switch should lock out in approxi-
mately 15 seconds. Ignition should stop
and oil valve should close. Blower will stop
after postpurge period.