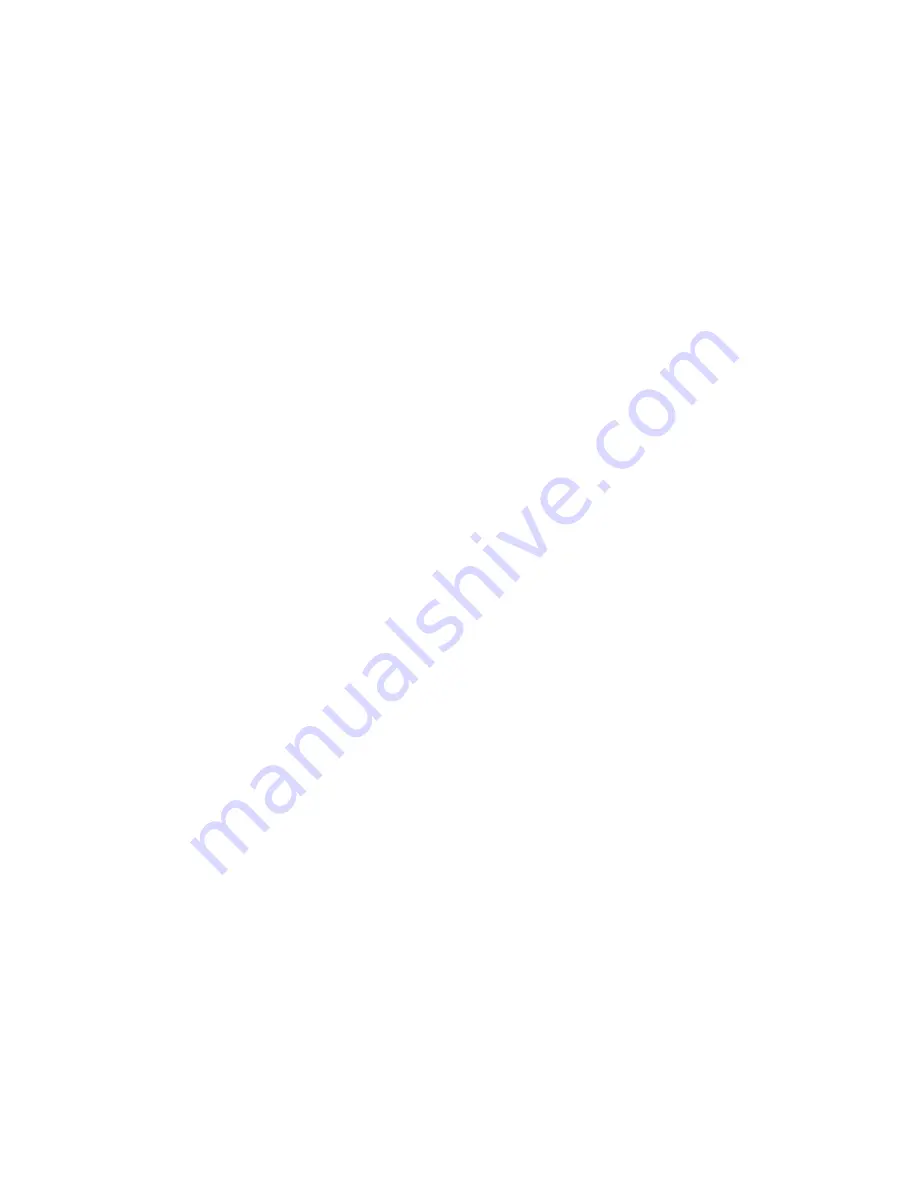
34
Method 1: Primary/Secondary Piping
This method can be used in heat-only applications as shown in Figure 9.2 or with an indirect water heater as shown
in Figure 9.3. This method relies on primary/secondary pumping to ensure that the required
fl
ow is always maintained
through the boiler. In this system, the
fl
ow rate through the boiler is completely independent of the
fl
ow rate through the
heating system. Use the following guidelines to ensure that the boiler will have the required
fl
ow shown in Table 9.1
regardless of the
fl
ow in the heating system.
1) Primary Loop Piping - Size the primary circulator and piping to obtain the design
fl
ow rate through the heating system
as you would on any other heating system. All piping between the expansion tank and secondary connection tees must
be at least as large as that shown in Table 9.5, column (a). In order to keep the
fl
ow rates in the primary and secondary
loops independent of each other, provide at least 8 diameters of straight pipe upstream of the
fi
rst secondary tee and 4
diameters downstream of the second secondary tee. Keep the distance between the expansion tank and the
fi
rst secondary
tee as short as practical.
2) Secondary Loop (“Boiler Loop”) Piping – All piping must be the size shown for the boiler in Table 9.5, column (a). To
size the circulator:
a) Select one of the boiler water
fl
ow rates shown in Table 9.5, column (b) for the boiler being installed. When
selecting the required boiler
fl
ow rate, keep in mind that if the
fl
ow rate in the primary loop exceeds the
fl
ow
rate through the boiler, it will not be possible to obtain a 180F supply temperature in the primary loop. This is
because the supply water exiting the boiler will be mixed with cooler system return water before entering the
radiation.
b) Count all
fi
ttings in the planned secondary loop (the secondary loop consists of the shaded piping in Figure
9.4a). In doing so, do not count the secondary connection tees, unions, or the
fi
ttings supplied with the boiler
(these have already been accounted for).
c)
Using Table 9.7,
fi
nd the equivalent lengths of all
fi
ttings in the secondary loop. Total these equivalent lengths
and add them to the total length of planned straight pipe in the secondary loop. The result is the total equivalent
length of the secondary loop.
d) Using Table 9.5,
fi
nd the boiler size being installed and select a boiler secondary circulator that shows a
“maximum equivalent length” (column e) in excess of the total equivalent length calculated in Step (c).
3) Indirect Water Heater Loop Piping (If Indirect Water Heater is Used) – All piping must be the size shown in Table 9.6,
column (a). If the indirect water heater connections are smaller than the pipe size called for in column (a), reduce the
pipe size at the indirect water heater connections. To size the circulator:
a)
Count all
fi
ttings in the planned Indirect Water Heater Loop (the indirect water heater loop consists of the
shaded piping in Figure 9.4b). In doing so, you will be counting some piping and
fi
ttings which are common to
the heating system secondary (“boiler loop”) piping and which were counted in Step 2a above. Do not count the
elbows or
fi
ttings supplied with the boiler.
b) Using Table 9.7,
fi
nd the equivalent lengths of all
fi
ttings in the indirect water heater loop. Total these equivalent
lengths and add them to the total length of planned straight pipe in the indirect water heater loop.
The result is the total equivalent length of the indirect water heater loop.
c)
Using Table 9.6,
fi
nd the boiler size being installed and select an indirect water heater loop circulator that shows
a “maximum equivalent length” (column f) in excess of the total equivalent length calculated in Step b.
Example – Assume that a FCM120 is to be installed in a heating system along with an Alliance indirect water heater.
A total of 15 ft of straight pipe will be installed between the boiler and the primary loop. A total of 20 ft of straight
pipe will be installed between the boiler and the indirect water heater. Fittings are arranged as shown in Figure
9.3. A 9.0 GPM
fl
ow is required in the boiler loop. The MS-40 requires a
fl
ow rate of 8 GPM and has a head loss
of 3.0 ft.
Total
fi
ttings in Secondary loop (“boiler loop”):
6 90 Elbows
2 Runs of Tees
1 Swing Check
2 Isolation Valves
Note: Unions, Secondary Connection Tees, and factory supplied
fi
ttings are ignored.
Calculate total equivalent length from Table 9.7:
15ft Straight Pipe + 6 Elbows x 2.75 + 2 Runs of Tees x 1.75 + 1 Swing Check x 7 + 2 valves x 0.6 = 43.2
equivalent feet straight pipe. From Table 9.5, we see that a Taco 0014 will pump 9 GPM through a FCM120 with 61
equivalent feet of pipe, so the Taco 0014 is OK.
Summary of Contents for FREEDOM FCM120
Page 8: ...8 Figure 5 1 Wall Mounting Hole Locations ...
Page 9: ...9 Figure 5 2 Boiler Mounting Hardware ...
Page 11: ...11 Figure 6 1 Boiler Installed In A Confined Space Ventilation Air From Inside ...
Page 31: ...31 Figure 7 21 Condensate Piping Arrangement ...
Page 44: ...44 Figure 10 1 Wiring Connections Diagram ...
Page 45: ...45 Figure 10 2 Ladder Diagram ...
Page 46: ...46 Figure 10 3 Wiring of Isolation Relay for Control of Two Heating Circulators ...
Page 49: ...49 FCM Series Lighting and Operating Instructions ...
Page 55: ...55 FIGURE 12 2 BASIC MENU TREE ...
Page 64: ...64 ...
Page 66: ...66 ...
Page 68: ...68 ...
Page 69: ...69 ...
Page 70: ...70 ...
Page 72: ...72 150 151 152 153 154 155 ...
Page 73: ...73 156 157 158 159 160 161 ...
Page 74: ...74 162 ...
Page 75: ...75 NOTES ...
Page 78: ...78 NOTES ...
Page 79: ...79 NOTES ...
Page 80: ......