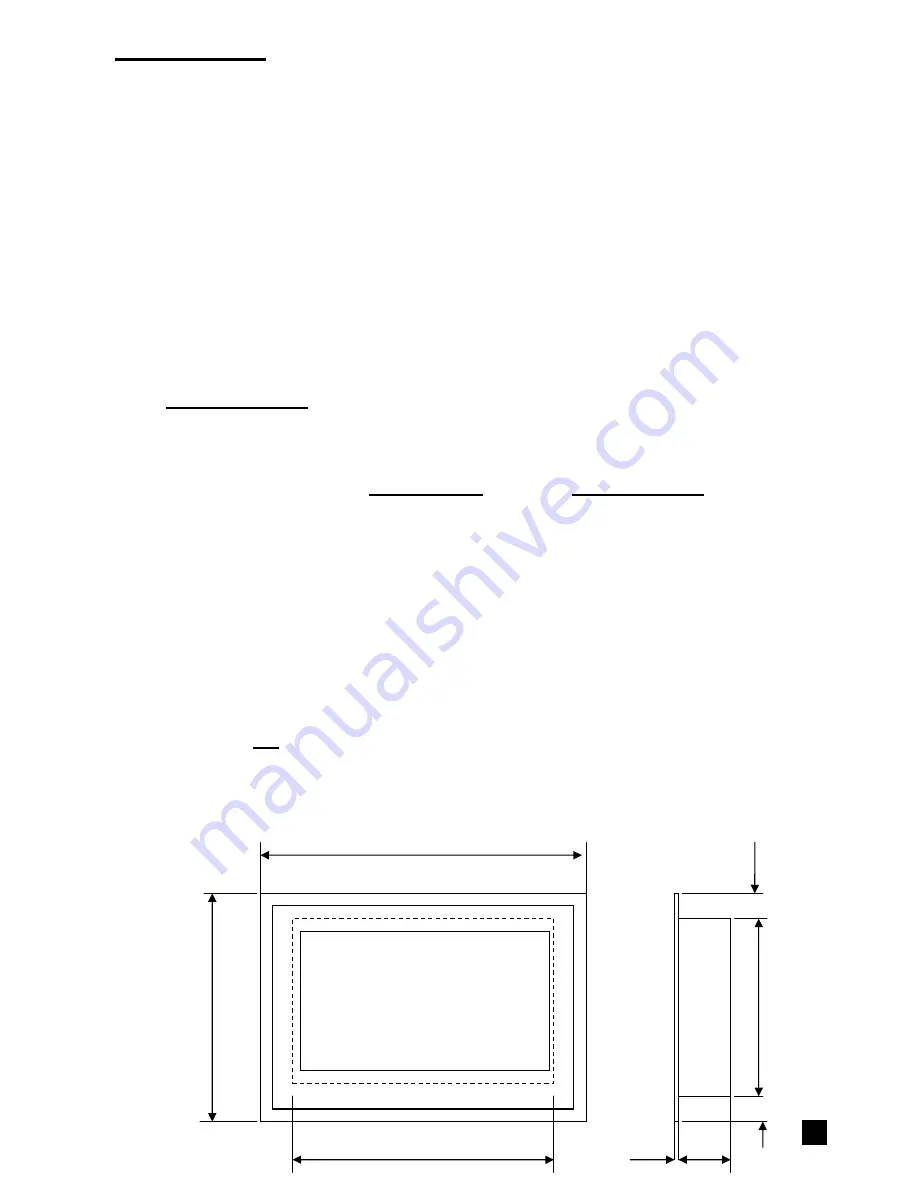
1
153 (78)
72 (12)
660
8
0
5
(
6
7
0
)
30
240
5
8
0
950 (792)
INTRODUCTION
Thank you for choosing this burley product. All of our products carry a CE mark which is awarded
by an independent test house (notified body) and shows the fires have been type tested to meet
the essential requirements of the European Gas Appliance Directive and the appropriate British
Standards.
This is a highly efficient Flueless Inset Live Fuel Effect Appliance. The burner system is very clean
burning and a catalyst cleans the combustion products even further.
A thermostat in the burner control system adjusts heat output to maintain a room temperature,
which can easily be set by the user. The appliance is operated via a battery powered remote
control system. Operation is also possible on the appliance with push button controls. There is also
a separate control to adjust the flame effect as required. Please demonstrate its operation to the
customer before leaving.
An oxygen depletion sensing pilot light is also fitted and will sense any significant oxygen depletion
in the room and shut the fire down safely.
1.
APPLIANCE DATA
Refer to the appliance data badge (this is located on a hinge-out plate )
ENSURE THAT THE LOCAL
CONDITIONS OF USE CORRESPOND TO THE INFORMATION ON THE DATA BADGE.
Natural Gas G20
LPG (Propane) G31
Category
I2H
I3P
Supply Pressure
20mBar
37mBar
Inlet Pressure
20mBar
*
37mBar
*
Heat Input (net)
(High)
4.2KW
4.2kW (180g/h)
(Low)
2.5kW
1.5kW (107g/h)
Inlet Connection
8mm Compression
8mm Compression
Injector (manual valve)
Elbow 92/300
Elbow 92/90
Injector (remote)
Elbow 92/170
Elbow 92/85
Note -
The inlet pressure must be /- 1.0 mbar of specification with
all
gas appliances in the
house switched on and also with just the Burley appliance operating. If outside of tolerance the
fault is most likely to be in the installation pipe work or service governor at the meter. A ‘lazy’
service governor can be the cause of pilot light problems if the problem is not spotted and
rectified. If the problem is the meter governor, this is the property of the gas service provider (e.g.
Transco in the UK or Bord Gais in Rep. of Ireland) and they should be called to rectify this.
Figure 1
Overall
Dimensions
(Figs in
brackets
refer to
model with
narrow
bright satin
trim)