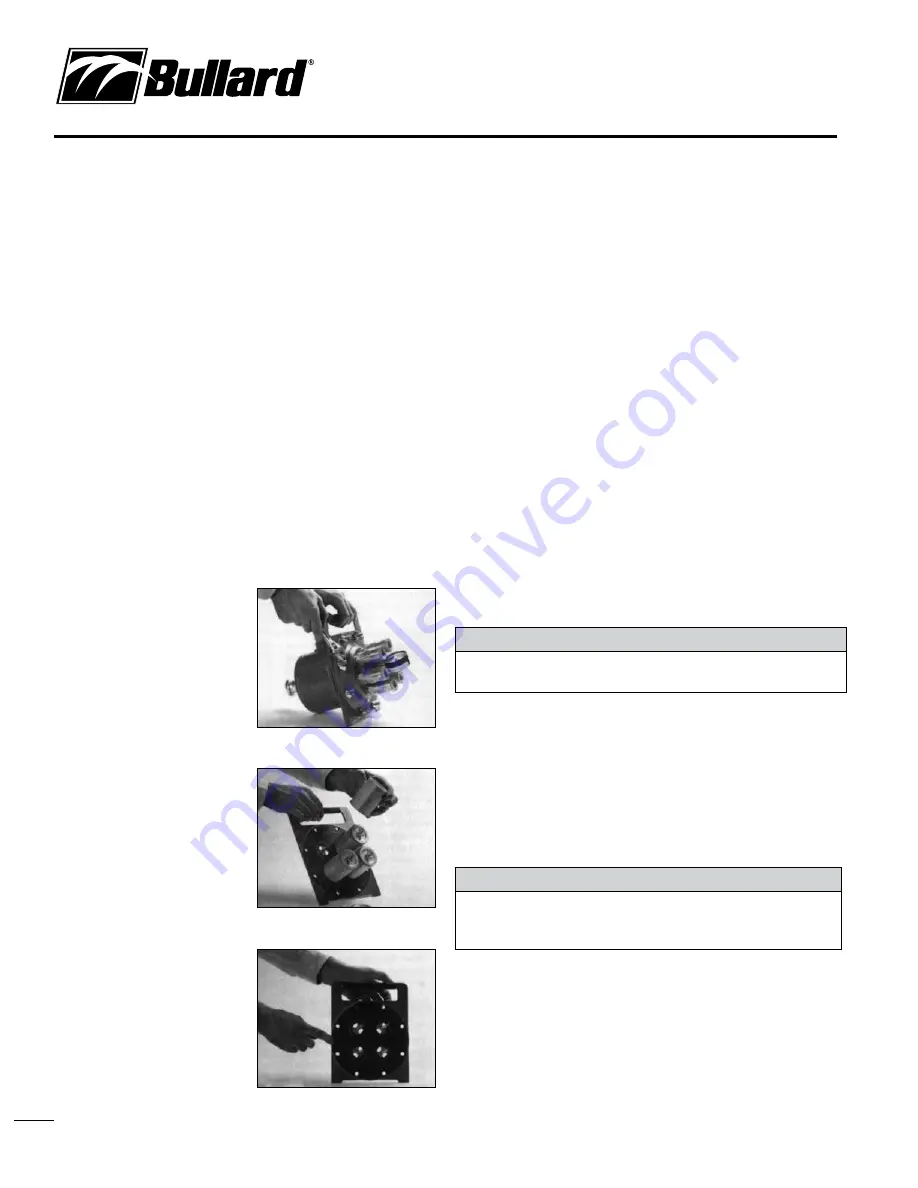
www.bullard.com
8
Maintaining the Fr
ee-Air Pump
Maintaining the Free-Air® Pump
Bullard EDP30 and EDP50 Free-Air Pumps consist of an electrically-
driven air pump with four carbon vanes. The vanes self-adjust as they
wear and should last the following length of time if properly maintained:
EDP30 - 3,000 to 10,000 Hours
EDP50 - 1,500 to 5,000 Hours
For the pump to operate at its optimum performance level, the following
simple maintenance procedures must be performed routinely:
Replace the Inlet and Outlet Filters Regularly
Dirty or clogged filters will restrict air flow to the respirators by causing a
decrease in the pump’s outlet pressure. They may also decrease vane life
and cause eventual pump overheating.
• Replace the inlet filter (Cat. No. 23611) at least once every 500 running
hours or once per month, whichever is sooner.
The Inlet Filter keeps particulates larger than 25 microns out of the
air supply and helps protect the pump’s carbon vanes.– Replace the
CARBOFINE outlet filter cartridges (Cat. No. S17101) at least once every
200 running hours or once per month, whichever is sooner.
The following are directions for replacing the outlet filter cartridge. These
steps must be performed outside the
contaminated work area:
a) Turn the pump off and disconnect
it from the power source.
b) Disconnect the air supply hose
attachment pod from the pump
or the V60 extension hose by
releasing the Kamlok clamps.
c) Remove the eight (8) wing nuts
(with a wrench or pliers) and
bolts holding the quick-discon-
nect coupler manifold to the pod
(Figure 12).
d) Remove the filter cartridge plate
from the pod.
e) Unscrew the wing nuts and re-
move the caps holding the outlet
filter cartridges in their seats.
Remove and discard the used
filter cartridges (Figure 13).
f) Visually inspect the rubber
gaskets on the filter cartridge
plate for wear, cracks or tears
(Figure 14).
If any sign of damage is
detected, replace with a new
gasket (Bullard Cat. Nos. 26701,
filter side or 27161, cover side).
The old gasket will have to be scraped off the plate. Glue a new
gasket onto the pod making sure the bolt holes are lined up with the
gasket.
g) Insert four (4) new filter cartridges in the seats and reassemble the
caps and wing nuts to hold the cartridges in place.
h) Reassemble the pod. Tighten the wing nuts and bolts together firmly
with a wrench or pliers, so that no air can escape between the three
parts.
i) Mount the pod back onto the pump or V60 extension hose, locking the
Kamlok clamps so that no air can escape.
j) Plug the pump back into its power source.
Flush the Pump if Necessary
Should excessive dirt, sand, foreign particles, moisture or oil be permitted
to enter the pump, the carbon vanes may become sluggish and the pump’s
performance will deteriorate. This will result in decreased outlet pres-
sure or failure of the pump to operate.If the pump remains idle in a humid
environment for a long period of time, rust film may build up in the pump’s
chamber and/or rotor slots. This will result in decreased outlet pressure or
a failure to operate at all. If the above occurs, the pump should be flushed
with one of the following recommended safety solvents:
• Loctite Safety Solvent (Cat. No. S1791)
• Inhibisol Safety Solvent
• Dow Chemical Chlorothane
�
WARNING
Never use kerosene or other combustible liquids or vapors with this pump.
Their use may result in an explosion which may cause injury or death.
Directions for Flushing Pump:
1. Before flushing, disassemble and remove the following parts from the
pump:
• Disconnect the respirator(s) air supply hose from the pod(s).
• Remove the pod or the V60 extension hose from the pump’s manifold.
• Remove the pump’s inlet filters.
2. With the pump running, pour several ounces of approved safety solvent
into each of the pump’s air inlet ports. Repeat the flushing if necessary.
�
WARNING
Run the pump for a sufficient time to purge all traces of the safety
solvent before reconnecting the pods, inlet filters and air supply
hoses and using the respirators.
Avoid Running the Pump at Excessive Pressure
Avoid running the pump model EDP30 above 30 psig or the EDP50 above
15 psig for any length of time. Running the pumps above the maximum
recommended psig rating could cause motor damage and premature wear
of the carbon vanes.
NEVER LUBRICATE THIS OIL-LESS AIR PUMP. THE MOTOR BEARINGS
ARE GREASE PACKED AND SEALED. THEY REQUIRE NO FURTHER
LUBRICATION.
Figure 12
Figure 14
Figure 13